Hello all!
It has been a while. Long working hours and young children
....
However, now that I have received some wood from my Russian friends (Dr Mike and Bibigon) I am able to start planking my hull as per the process I described in an earlier post. Attached are photos of black hornbeam, yellow hornbeam and 2 shades of pear although they are very, very similar.
I can vouch for the quality of Bibigon's wood. Additionally, he really did go above and beyond to ensure I received it safely. Shipping to Australia is not easy and we have tried a few different options before discovering the most efficient methods.
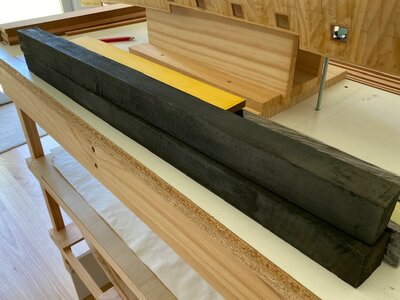
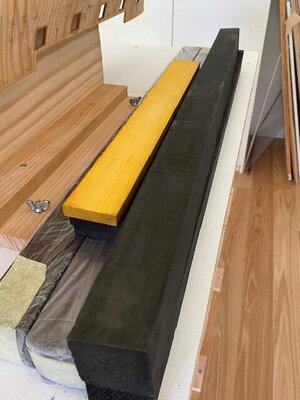
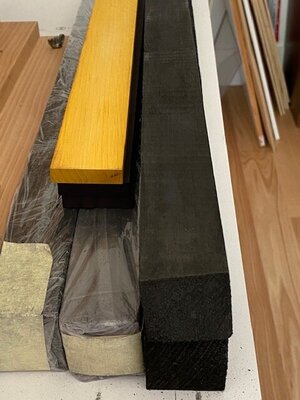
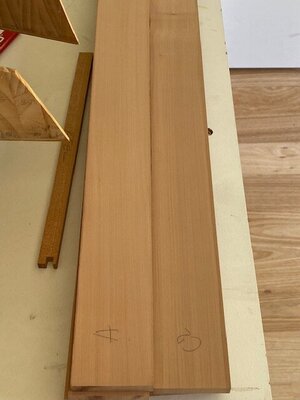
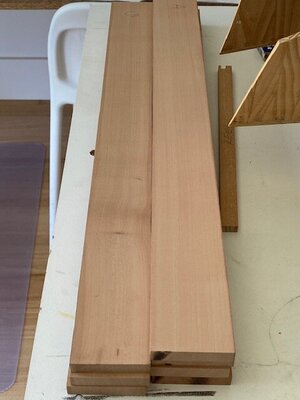
It has been a while. Long working hours and young children

However, now that I have received some wood from my Russian friends (Dr Mike and Bibigon) I am able to start planking my hull as per the process I described in an earlier post. Attached are photos of black hornbeam, yellow hornbeam and 2 shades of pear although they are very, very similar.
I can vouch for the quality of Bibigon's wood. Additionally, he really did go above and beyond to ensure I received it safely. Shipping to Australia is not easy and we have tried a few different options before discovering the most efficient methods.
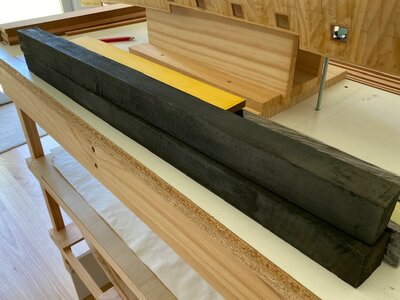
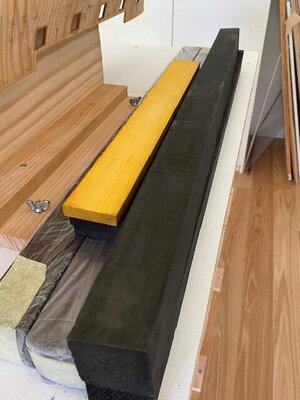
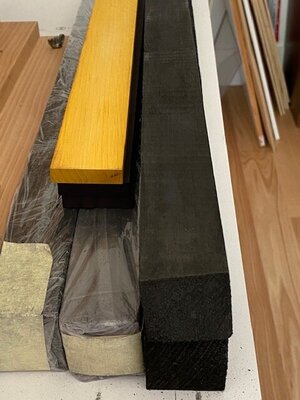
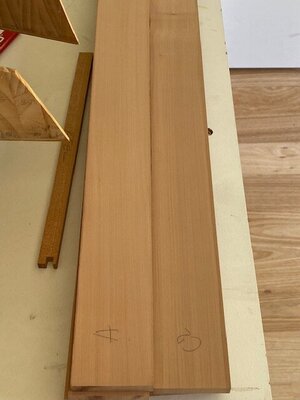
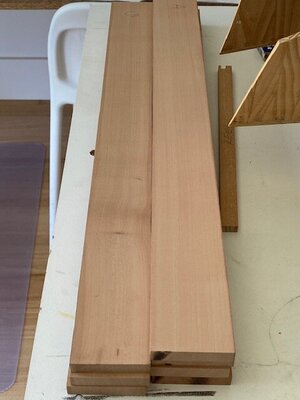