Planking Section C:
If you refer to the photo you now have a series of dots from the very stern of the hull all the way to the front of Section B. These dots are shown as blue dots in my photo. You also have dots at the very bow - shown in my photo as C1, C2, C3, C4 and C5. (Please disregard the pencil lines in my photo as these would not be there at this stage).
Now, using my flexible piece of plastic and trying to preserve proportionality between the widths of the bands I simply join B1 to C1, B2 to C2, B3 to C3 and so on and each time mark this with a pencil. Each line must then be carefully checked from all angles to ensure it runs smoothly. If it doesn't you need to make adjustments.
You can reference the plans here for additional key points or details if you need to. For example, you will notice in my image the section B4 - C4 - C5 - B5 has 3 planks tapering down to only 1 plank at the very bow. This is shown on the plans and has been preserved on my hull.
You now need to extend the solid line all the way to the stern of the model. Join all dots for each band from section B back to the very stern using the same flexible plastic. Again, the line must be smooth all the way from bow to stern. This might mean you have to fudge a dot here or there. If you have high quality and reliable plans and pay attention to accuracy with measurements it will pay off royally at this time.
One key point to ensure is that the band widths don't go from narrow to wider and then narrower again as you move back towards the stern. If a band does this then the band needs to be adjusted slightly to esnure a constant narrowing as you move sternwards.
Now it is a case of planking each band separately ensuring you stay within the lines for each band. I haven't started this process yet but I will post photos as I do.
I am now experimenting with caulking options for the hull planking.
Also, I will use Swiss pear for the hull planking.
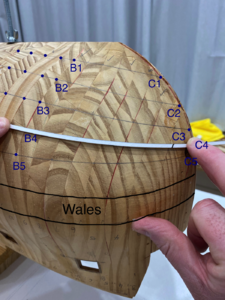
If you refer to the photo you now have a series of dots from the very stern of the hull all the way to the front of Section B. These dots are shown as blue dots in my photo. You also have dots at the very bow - shown in my photo as C1, C2, C3, C4 and C5. (Please disregard the pencil lines in my photo as these would not be there at this stage).
Now, using my flexible piece of plastic and trying to preserve proportionality between the widths of the bands I simply join B1 to C1, B2 to C2, B3 to C3 and so on and each time mark this with a pencil. Each line must then be carefully checked from all angles to ensure it runs smoothly. If it doesn't you need to make adjustments.
You can reference the plans here for additional key points or details if you need to. For example, you will notice in my image the section B4 - C4 - C5 - B5 has 3 planks tapering down to only 1 plank at the very bow. This is shown on the plans and has been preserved on my hull.
You now need to extend the solid line all the way to the stern of the model. Join all dots for each band from section B back to the very stern using the same flexible plastic. Again, the line must be smooth all the way from bow to stern. This might mean you have to fudge a dot here or there. If you have high quality and reliable plans and pay attention to accuracy with measurements it will pay off royally at this time.
One key point to ensure is that the band widths don't go from narrow to wider and then narrower again as you move back towards the stern. If a band does this then the band needs to be adjusted slightly to esnure a constant narrowing as you move sternwards.
Now it is a case of planking each band separately ensuring you stay within the lines for each band. I haven't started this process yet but I will post photos as I do.
I am now experimenting with caulking options for the hull planking.
Also, I will use Swiss pear for the hull planking.
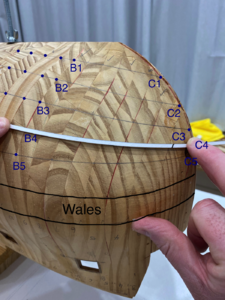