On to the catheads. They are to be made out of 5mm square walnut, but I didn't think I could make nice, closely fit 5x5mm square holes to retain them. And, I want anything sticking out of the hull to be sturdy, so wanted the catheads to extend toward the center of the hull, into a bulkhead. I felt I could to this best with a round hole and shaft, rather than square. So, I needed to turn round ends on my 5x5mm stock.
I first chucked the 5x5 stock up in my electric drill:
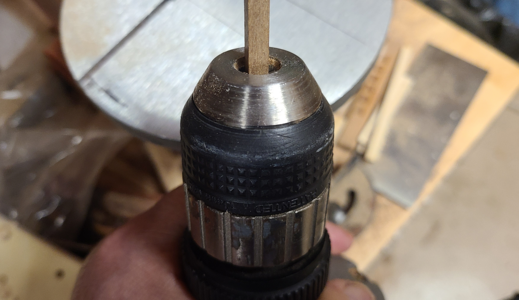
No, it doesn't chuck up well or centered, but it's in the ballpark (a saying I should probably use throughout this build: "It's in the ballpark!").
I then placed the walnut square strip through a piece of plastic tubing I had on hand. Holding the tubing, and rotating the square strip using the drill, I roughly turned the end of the strip to 3/16" diameter using my belt sander:
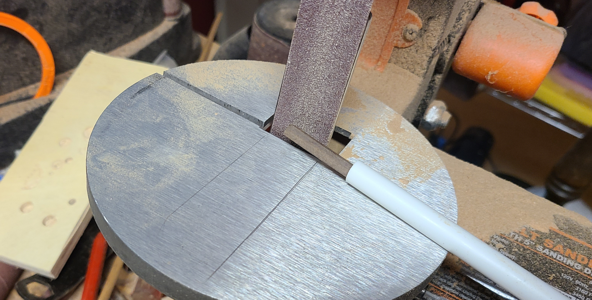
This wasn't extremely accurate, due to the loose fit of the tube, but at least it held it in place. If it were a snugger fit, it would be more accurate. I then chucked this turned round end in the drill, and did the same to the other end of my 5mm strip (one cathead would be at each end).
I then used tape to allow me to accurately locate and mark the center hole for the catheads:
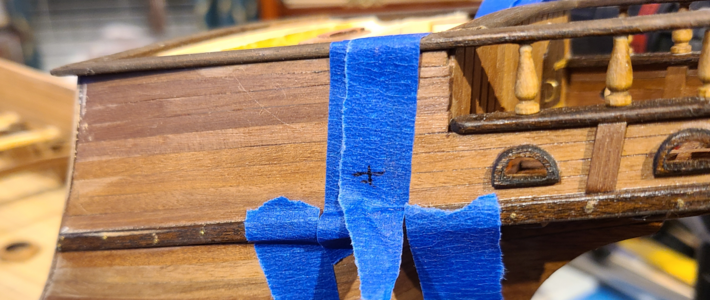
and drilled 3/16" holes for them. I like to use a bradpoint drill when drilling holes like this, as they are both easy to center, and cleanly cut the OD of the hole:
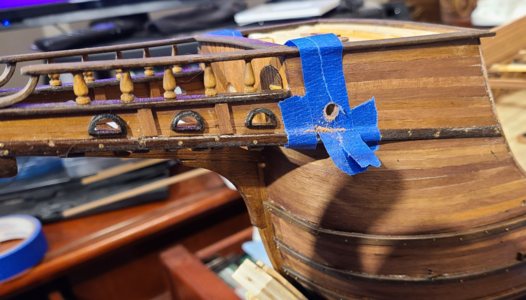
I inserted the 3/16" drill to help locate the correct angle for the extended drill to the inside bulkhead. Using a level, I could measure the angle from horizontal of the drill, then marking where it hit the bulkhead:
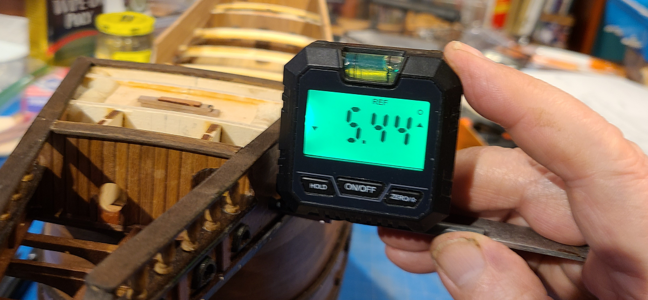
ANGLE MEASUREMENT DEVIATION:
Using Paintshop Pro, I measured the angle of the catheads above horizontal to be about 3 degrees; also, they are square to the hull, horizontally, where they attach. So, I used my trusty angle measurement device to mark where the drill bit hits the inner bulkhead:
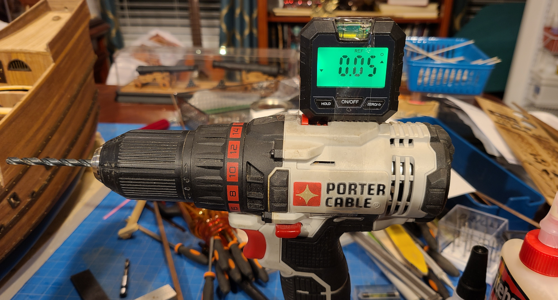
I also taped the angle device to the top of my drill to attempt to get the angle right.
Then a measurement to be sure I'd obtained (approximately) the correct angle:
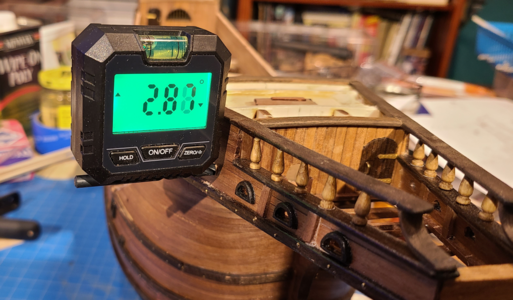
and also square to the sides:
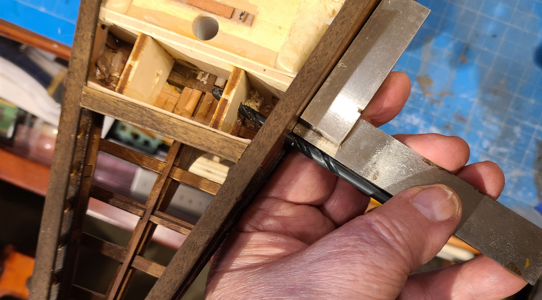
The above view clearly shows where the drill enters the inner bulkhead.
I then made the same measurements and confirmations using the cathead material, with each end rounded and inserted. The inner hole can be easily adjusted, if necessary, to get the right angle and square:
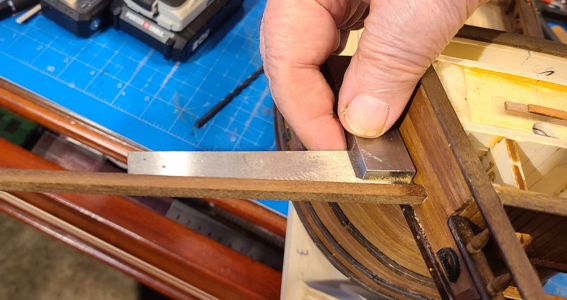
Then the catheads were cut to the correct length, with about 2cm extending beyond the round section, and holes/slots were drilled to simulate pulleys in the catheads for the anchors:
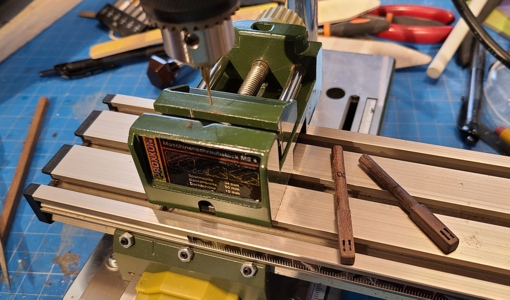
For each slot, a through hold was drilled at each end, and a recessed, rounded area was milled to simulate the pulleys that would be mounted within. I would like to have used the brass pulleys I have, but the smallest are 1mm wide, and my slots are only 0.7mm wide. They'll be partly covered by the ropes, anyhow.
Catheads are now glued in place, all from the inside, to the hull and inner bulkheads:
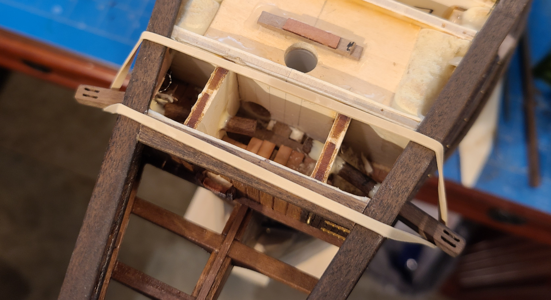
I took some time to lay out the planking on the forecastle, as I wanted the planking sequence to match the remainder of the decking, but I wanted to be sure that the invisible crossmembers to which the planks were nailed, and on which ends of planks ended, were in logical positions (i.e. not right at the foremast, as that would be impossible), nor were any joints excessively close to the foremast. I laid this out on my computer and printed it out as a guide to planking:
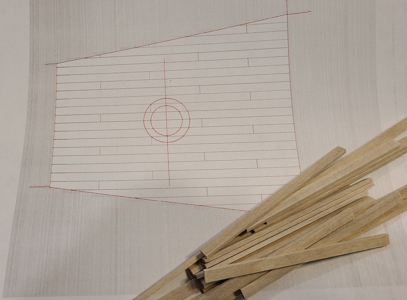
Planking here is about half done, with hole for foremast marked:
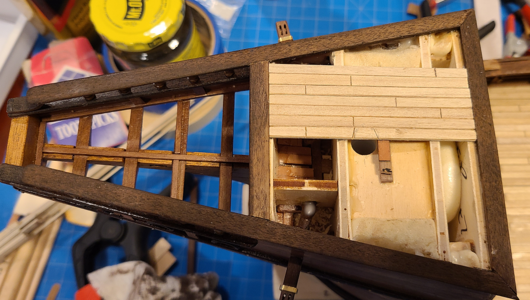
As noted earlier in this build, I shimmed up around all the masts so that planking would be well supported near them.
Also notice in the above photo the last remnants of the expanding foam filler I used on the hull. Hard to believe at one point it looked like this:
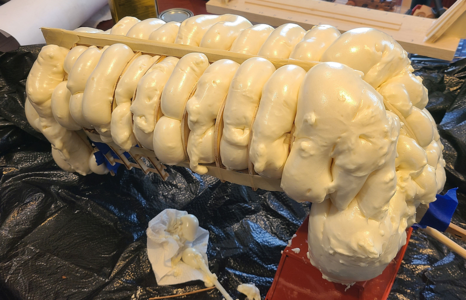
Planking of the forecastle is now complete:
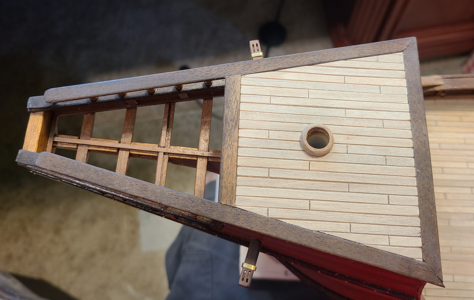
and brass bands have been added to the catheads, and the mast coat for the foremast.
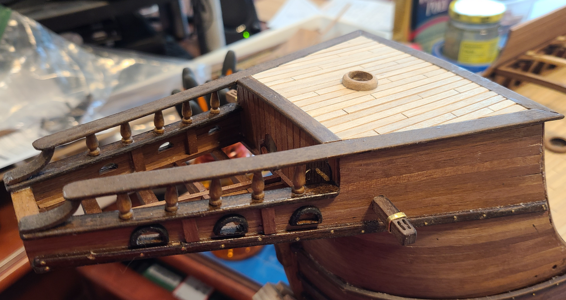
The brass for the bands was taken from the "sprue" of the photo-etched brass parts included with the kit. Thicker than I'd like at 0.5mm, but I had no other thinner strip to use.
Not sure what to work on next. I have to make a bunch of cleats to fit on vertical braces on decks, but I hate working on those little things. Guess I'll have to see. Until next time!
I first chucked the 5x5 stock up in my electric drill:
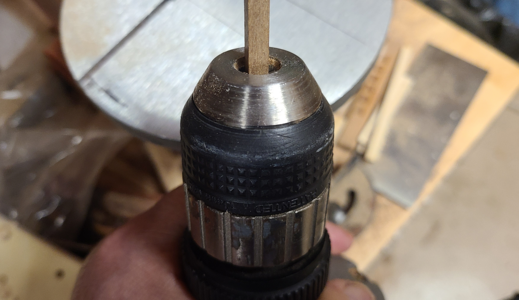
No, it doesn't chuck up well or centered, but it's in the ballpark (a saying I should probably use throughout this build: "It's in the ballpark!").
I then placed the walnut square strip through a piece of plastic tubing I had on hand. Holding the tubing, and rotating the square strip using the drill, I roughly turned the end of the strip to 3/16" diameter using my belt sander:
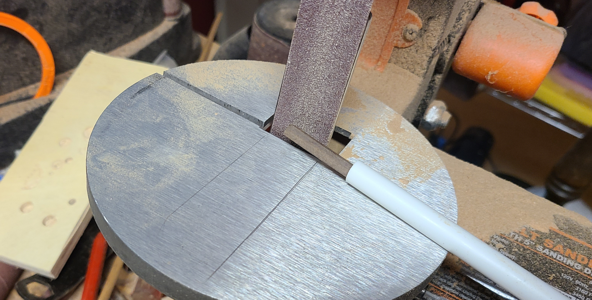
This wasn't extremely accurate, due to the loose fit of the tube, but at least it held it in place. If it were a snugger fit, it would be more accurate. I then chucked this turned round end in the drill, and did the same to the other end of my 5mm strip (one cathead would be at each end).
I then used tape to allow me to accurately locate and mark the center hole for the catheads:
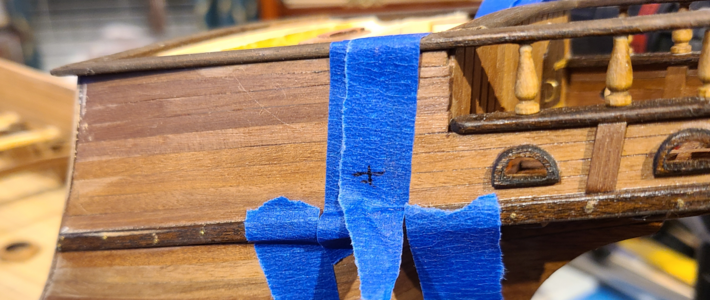
and drilled 3/16" holes for them. I like to use a bradpoint drill when drilling holes like this, as they are both easy to center, and cleanly cut the OD of the hole:
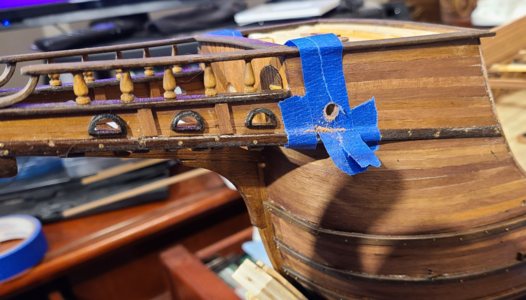
I inserted the 3/16" drill to help locate the correct angle for the extended drill to the inside bulkhead. Using a level, I could measure the angle from horizontal of the drill, then marking where it hit the bulkhead:
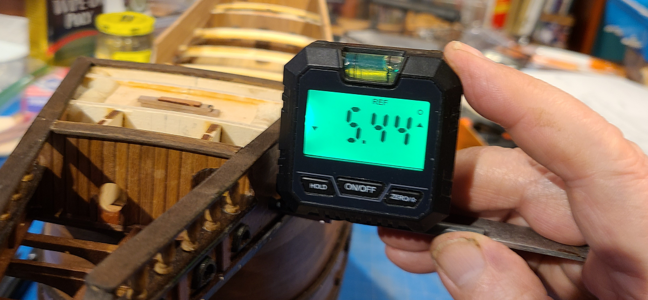
ANGLE MEASUREMENT DEVIATION:
I will deviate a bit from my build to discuss level and angle measurement. I like to make sure various angles in my build are as accurate as I can make them. I've had the plans for this build scanned at Staples into PDF format, and converted that to PNG, so I can view the plans at any magnification on my 32" computer monitor. And I can bring the PNGs into my paint program of choice (the old Paintshop Pro), where I can accurately measure distances and angles, among other things. The scans converted to 100 dpi, so I can accurately measure any distance in pixels, and divide by 100 to get inches to 1/100".
Paintshop Pro allows me to draw lines at angles, and by doing so and tracing over elements on the drawing, I can easily, quickly and accurately measure angles of masts, decks, basically anything. I can then go to my model, using those angle measurements, and accurately adjust those items on my model.
Until recently, I had used a phone app called Bubble Level, to set these angles. I don't even have to have a true level surface; the app can be zeroed on my work desk, then I can measure the angle from that. This worked well with the phone, except 1) I had to remove the case, to get a more accurate measurement, 2) The phone is larger than ideal to fit in some areas and 3) I couldn't take photos of using it.
Enter Temu.com. This recent (for me) gadget shopping paradise has given me the pictured above Digital Protractor Angle Finder for $6.37. It comes calibrated, with instructions on how to recalibrate, but can be temporarily "zeroed" to any surface (like my desk which is close but not quite level), reads to 0.01 degrees, with readings available in degrees, % slope, mm/m and in/ft. I now use this to measure angles on my model, vertical angles on my belt sander, pretty much everything. It's magnetic base holds to anything steel, and can be placed on a stiff straightedge for more accurate and longer-based measurements.
Continuing:Using Paintshop Pro, I measured the angle of the catheads above horizontal to be about 3 degrees; also, they are square to the hull, horizontally, where they attach. So, I used my trusty angle measurement device to mark where the drill bit hits the inner bulkhead:
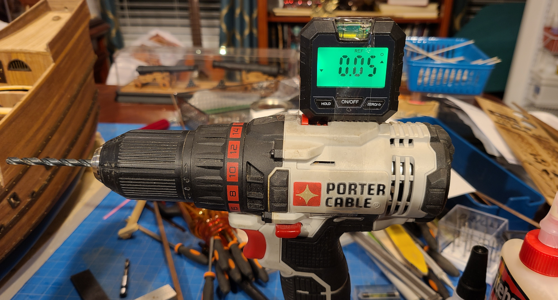
I also taped the angle device to the top of my drill to attempt to get the angle right.
Then a measurement to be sure I'd obtained (approximately) the correct angle:
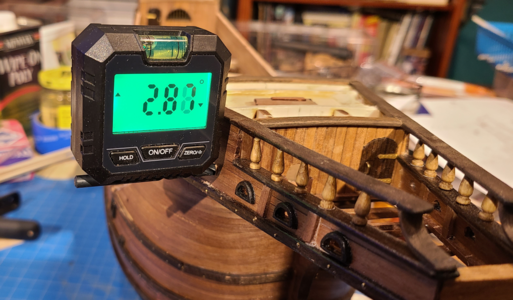
and also square to the sides:
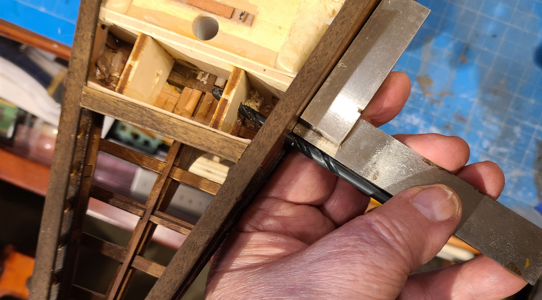
The above view clearly shows where the drill enters the inner bulkhead.
I then made the same measurements and confirmations using the cathead material, with each end rounded and inserted. The inner hole can be easily adjusted, if necessary, to get the right angle and square:
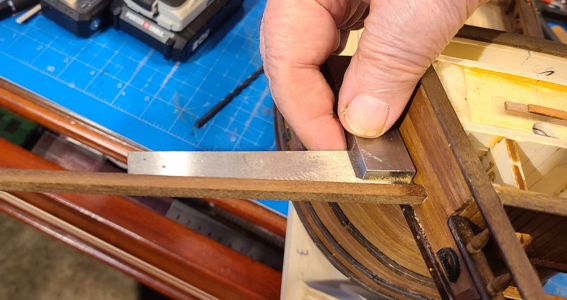
Then the catheads were cut to the correct length, with about 2cm extending beyond the round section, and holes/slots were drilled to simulate pulleys in the catheads for the anchors:
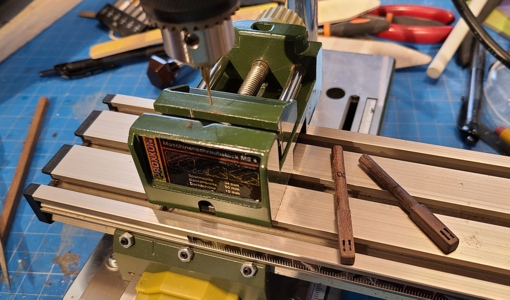
For each slot, a through hold was drilled at each end, and a recessed, rounded area was milled to simulate the pulleys that would be mounted within. I would like to have used the brass pulleys I have, but the smallest are 1mm wide, and my slots are only 0.7mm wide. They'll be partly covered by the ropes, anyhow.
Catheads are now glued in place, all from the inside, to the hull and inner bulkheads:
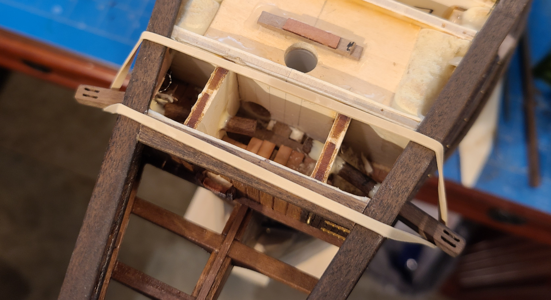
I took some time to lay out the planking on the forecastle, as I wanted the planking sequence to match the remainder of the decking, but I wanted to be sure that the invisible crossmembers to which the planks were nailed, and on which ends of planks ended, were in logical positions (i.e. not right at the foremast, as that would be impossible), nor were any joints excessively close to the foremast. I laid this out on my computer and printed it out as a guide to planking:
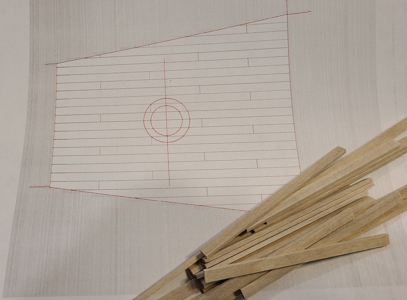
Planking here is about half done, with hole for foremast marked:
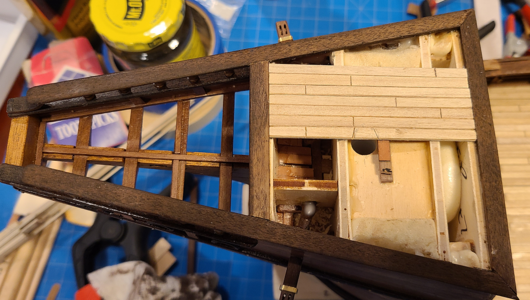
As noted earlier in this build, I shimmed up around all the masts so that planking would be well supported near them.
Also notice in the above photo the last remnants of the expanding foam filler I used on the hull. Hard to believe at one point it looked like this:
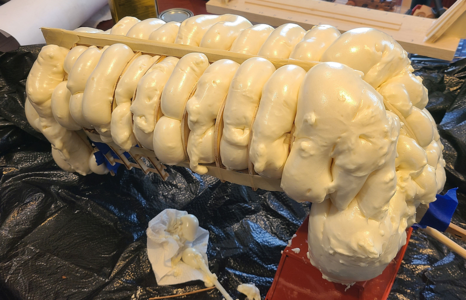
Planking of the forecastle is now complete:
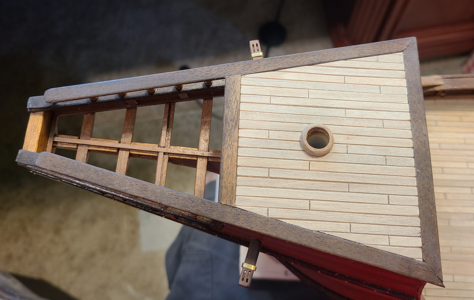
and brass bands have been added to the catheads, and the mast coat for the foremast.
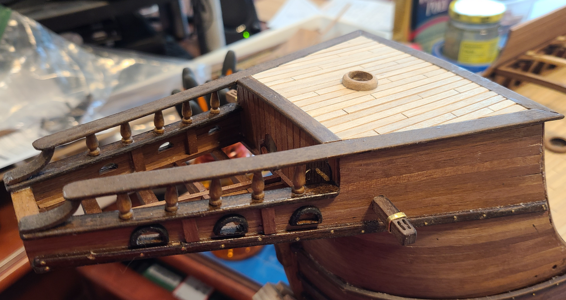
The brass for the bands was taken from the "sprue" of the photo-etched brass parts included with the kit. Thicker than I'd like at 0.5mm, but I had no other thinner strip to use.
Not sure what to work on next. I have to make a bunch of cleats to fit on vertical braces on decks, but I hate working on those little things. Guess I'll have to see. Until next time!
Last edited: