- Joined
- Apr 10, 2020
- Messages
- 369
- Points
- 323
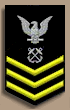
AHOY and HAPPY NEW YEAR
We know how much time is needed to build a wooden hull of a sailing ship. How much patience and skill are needed. Not all modelers have enough time for their hobbies.
We have a solution for that. Santa Claus brought us a new 4-axis CNC milling machine. Whereby we can make a wooden hull in pieces. There will be enough to glue the pieces of solid wood together and to stick with the veneer. The thickness of the shell of the hull from 2.5 mm (0.1 inch) to ..... YOU WILL SAVE TIME.
NEW YEAR – NEW TECHNOLOGIES - NEW POSSIBILITIES - NEW SOLUTION FOR IMPATIENT MODELERS
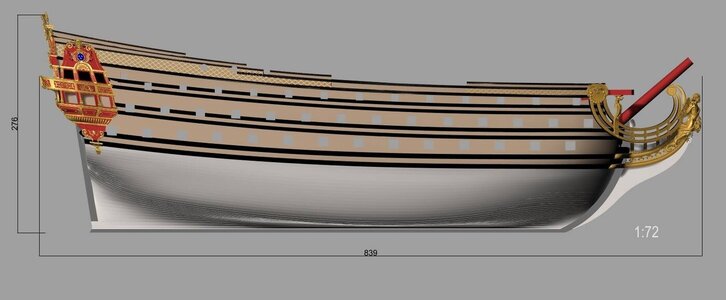
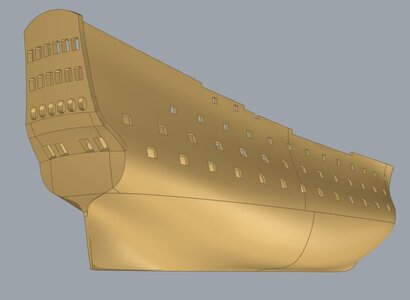
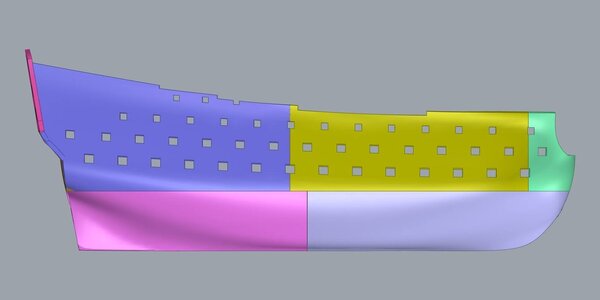
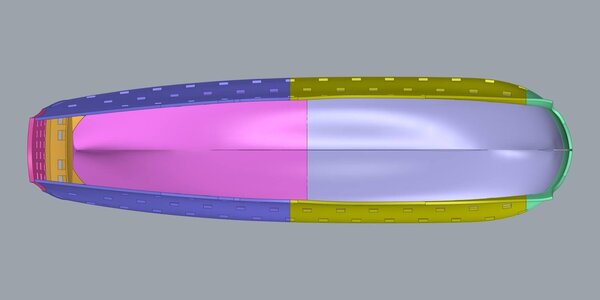
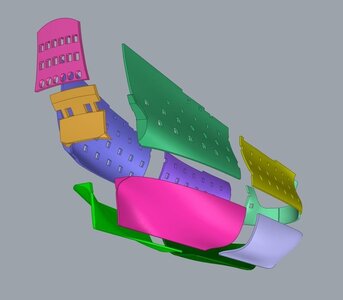
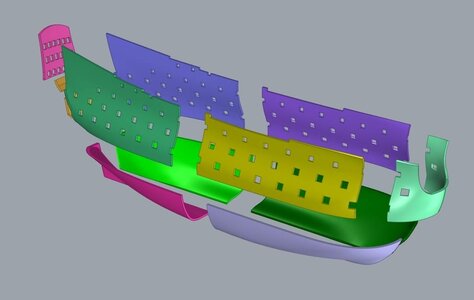
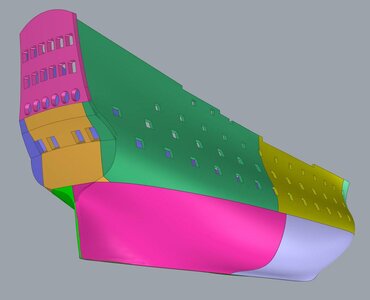
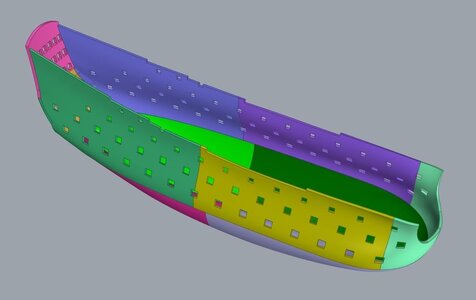

We know how much time is needed to build a wooden hull of a sailing ship. How much patience and skill are needed. Not all modelers have enough time for their hobbies.
We have a solution for that. Santa Claus brought us a new 4-axis CNC milling machine. Whereby we can make a wooden hull in pieces. There will be enough to glue the pieces of solid wood together and to stick with the veneer. The thickness of the shell of the hull from 2.5 mm (0.1 inch) to ..... YOU WILL SAVE TIME.
NEW YEAR – NEW TECHNOLOGIES - NEW POSSIBILITIES - NEW SOLUTION FOR IMPATIENT MODELERS

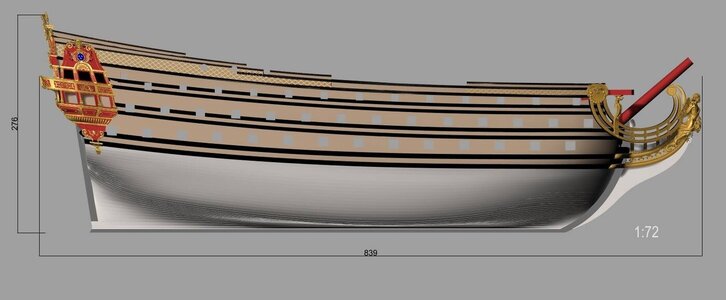
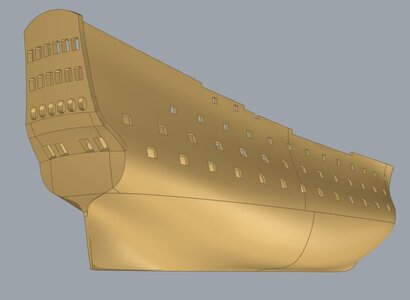
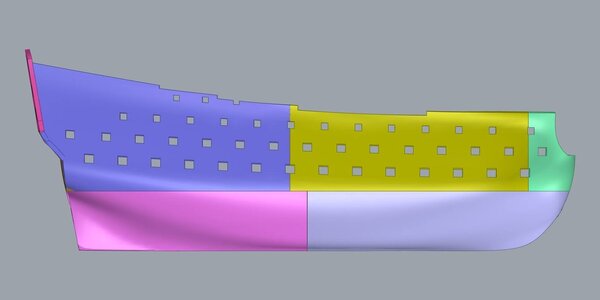
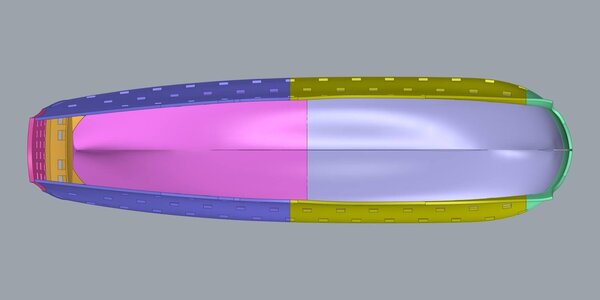
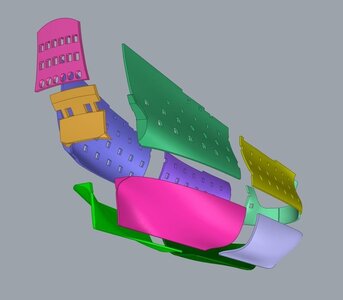
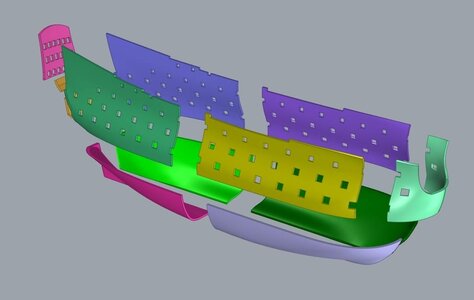
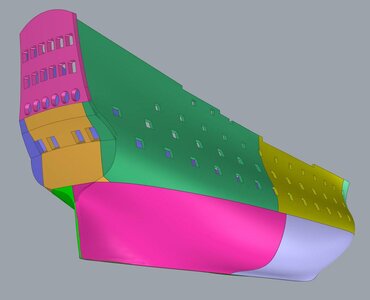
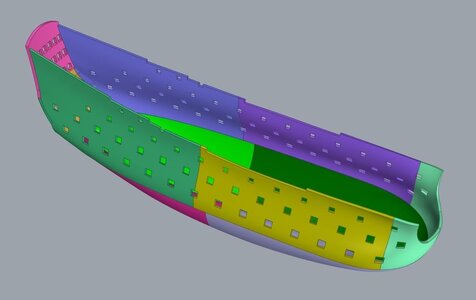