- Joined
- Dec 1, 2016
- Messages
- 6,021
- Points
- 728
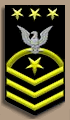
So, as a recap. Dave is the Sir Edward Hawk still going to be the first lesson and if so when do you (we) plan to start?
Donnie
the Sir Edward Hawk will indeed be the subject of a build. I will attach a set of "modeling plans" for those who want to do all the work from square one cutting and milling there own wood, OR i will also provide milled framing stock for those who do not have the power tools to cut and mill their own. This will be where frames blanks are built up and frames cut out, the next offer will be a set of laser cut frames which a builder will have to build the frames and can start building a hull. Believe me this is semi-scratch and a lot can go wrong. There are no fittings, no deck structures it will all be built from scratch.
Because this is a "school for model ship building" and NOT a build log there is a lot to cover before anyone starts cutting wood or building a scale model ship. There is no point in jumping into a build if the builder does not know how to get there in the first place. I was or actually still am a mechanical drawing that is what they called it back then. It involves taking a 2d drawing and projection the front, sides, back and bottom views. So a machinist or anyone can use the drawings to produce a part or structure.
I wondered about the shipwrights who came here in the wilds of the Great Lakes region and built warship with no mold loft and no drawings. After researching these master shipwrights i realized they were trained surveyors. They built ship with only a sheet of numbers. It was called a table of offsets that converted a 2D drawing into X,Y,Z Coordinates.
One of my grandsons is a civil engineer and i showed him a drawing like the one i posted and asked can you build this without any instructions? He said "oh ya it is a 2d drawing of a 3D object no problem" You can find any point anywhere on the hull from the drawing.
Donnie
the Sir Edward Hawk will indeed be the subject of a build. I will attach a set of "modeling plans" for those who want to do all the work from square one cutting and milling there own wood, OR i will also provide milled framing stock for those who do not have the power tools to cut and mill their own. This will be where frames blanks are built up and frames cut out, the next offer will be a set of laser cut frames which a builder will have to build the frames and can start building a hull. Believe me this is semi-scratch and a lot can go wrong. There are no fittings, no deck structures it will all be built from scratch.
Because this is a "school for model ship building" and NOT a build log there is a lot to cover before anyone starts cutting wood or building a scale model ship. There is no point in jumping into a build if the builder does not know how to get there in the first place. I was or actually still am a mechanical drawing that is what they called it back then. It involves taking a 2d drawing and projection the front, sides, back and bottom views. So a machinist or anyone can use the drawings to produce a part or structure.
I wondered about the shipwrights who came here in the wilds of the Great Lakes region and built warship with no mold loft and no drawings. After researching these master shipwrights i realized they were trained surveyors. They built ship with only a sheet of numbers. It was called a table of offsets that converted a 2D drawing into X,Y,Z Coordinates.
One of my grandsons is a civil engineer and i showed him a drawing like the one i posted and asked can you build this without any instructions? He said "oh ya it is a 2d drawing of a 3D object no problem" You can find any point anywhere on the hull from the drawing.