- Joined
- Dec 1, 2016
- Messages
- 6,021
- Points
- 728
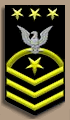
so far the discussion has been around scratch building a plank on frame hull. But scratch building is not limited to plank on frame you can design and build a hull using bulkheads or what is called the bread-and-butter method which is building from lifts.
for now it is back to framing. The problem with framing a hull is keeping all the framing the correct place.
first issue is to make sure the frames are square to the keel, The problem is you only have that little notch over the keel and a frame can move quite a bit.
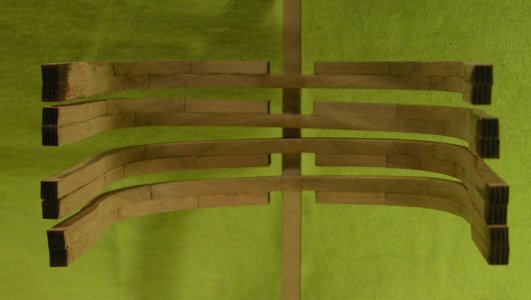
a solution to squaring up the frames as you install them is to use a backing piece. Start with the midship frame and work your way to the bow and stern.
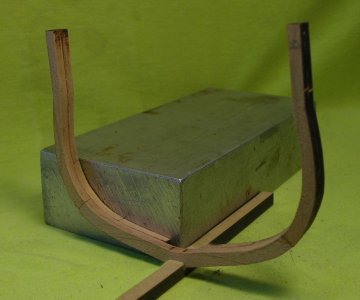
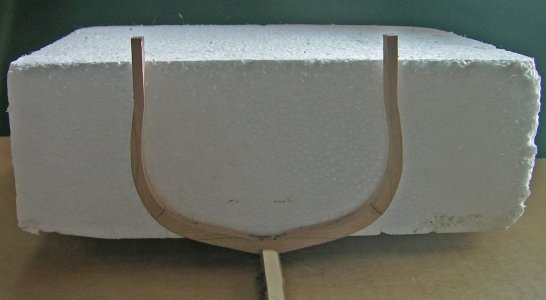
by using a square backing block you also are keeping the frames from leaning, the frame on the left is leaning in.
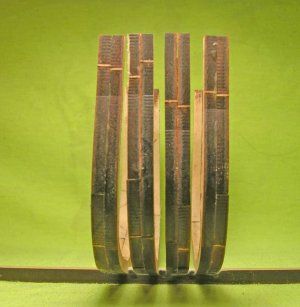
another way to prevent frames from leaning fore and aft is to use blocks between the frames. Once you square up the mid frame the next frame is located in the keel notch and blocks used at the top. I learned the hard way this is not a fool proof method because if all the space blocks are ever so slightly different thicknesses that slight error adds up and the entire structure will lean.
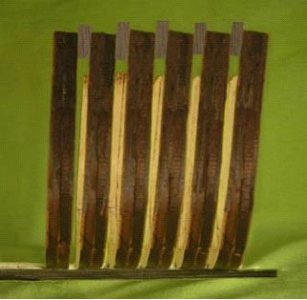
Frames will move side to side and back to front and it is a task to keep everything in line.
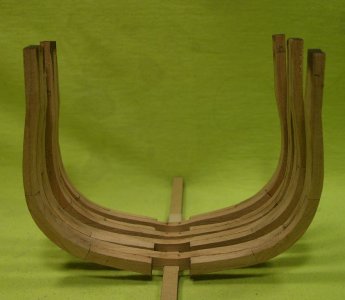
a problem reported by builders using the Hahn jig method found themselves still having a problem keeping the frames level side to side

The problem happens when the extensions are not finished exactly the same, the top extension sits in the jig which located the height of the frame. Hahn used a jig to insure each frame fit tight to the top of the keel and the top of the extensions sat against the jig
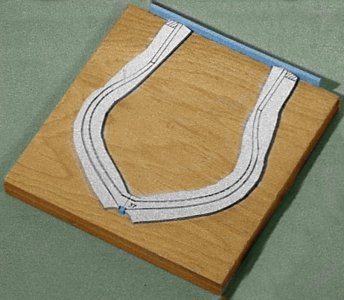
Harold's use of a jig solves the problem of locating the frames and holding the in place.
for now it is back to framing. The problem with framing a hull is keeping all the framing the correct place.
first issue is to make sure the frames are square to the keel, The problem is you only have that little notch over the keel and a frame can move quite a bit.
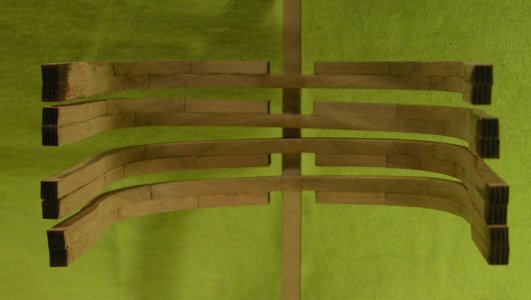
a solution to squaring up the frames as you install them is to use a backing piece. Start with the midship frame and work your way to the bow and stern.
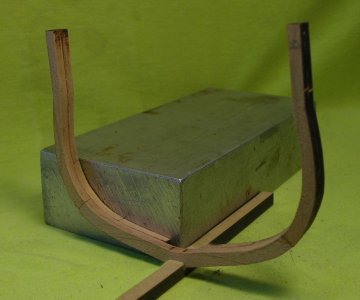
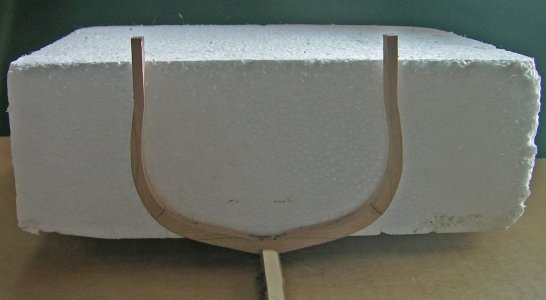
by using a square backing block you also are keeping the frames from leaning, the frame on the left is leaning in.
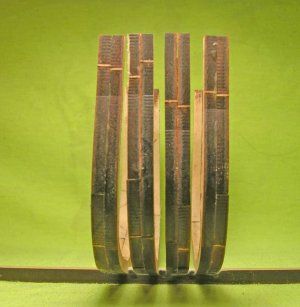
another way to prevent frames from leaning fore and aft is to use blocks between the frames. Once you square up the mid frame the next frame is located in the keel notch and blocks used at the top. I learned the hard way this is not a fool proof method because if all the space blocks are ever so slightly different thicknesses that slight error adds up and the entire structure will lean.
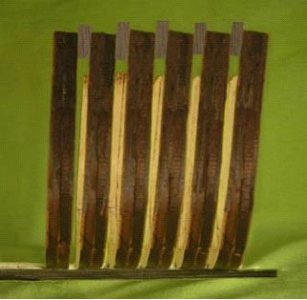
Frames will move side to side and back to front and it is a task to keep everything in line.
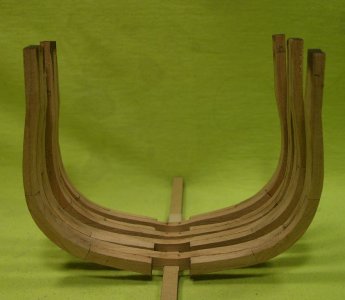
a problem reported by builders using the Hahn jig method found themselves still having a problem keeping the frames level side to side

The problem happens when the extensions are not finished exactly the same, the top extension sits in the jig which located the height of the frame. Hahn used a jig to insure each frame fit tight to the top of the keel and the top of the extensions sat against the jig
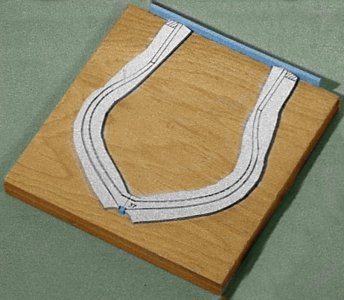
Harold's use of a jig solves the problem of locating the frames and holding the in place.
Last edited: