I am sure you all heard "i don't need instructions" i know what i am doing. Or asking for advice only to get "did you read the instructions?"
Building a model ship from scratch you would think there are no instructions, but you would be wrong there are instructions just not in a little booklet with step by step how to do something. To become a shipwright required schooling and or years of being an apprentice under a master shipwright. So the rules are out there just scattered over many years of published books and first hand knowledge. In modern times all over the web and scattered in forums.
Then again scratch building allows you the builder the freedom to follow your own methods rather than those of someone who may or many not be correct. You also have the opportunity to learn by your mistakes and learn how to "fix" those mistakes and correct problems.
To exercise my freedom what should i do now? well i can start building deck structures like coamings, companion way, skylight etc. Maybe do the hull planking above the wales.
I went out in the shop and milled out pearwood planking then came back in and sat down with the hull to plan out the planking. It did not take long to realize what i intend on doing and what the sequence of the build dictates is not the same thing.
No problem at the stem that is pretty much straight forward and where to start the first plank is also a no brainer at the top of the wale!
The issue became clear at the stern this is what is should look like.
looking down on the hull there is a space where the ends of the planks are just flapping in the wind and nothing to nail them to.
the red arrow shows the outer face of the hull frames so it seems i forgot something. the hull planking does not glue very well to air. Looks like i got my next step defined "finish the stern" first.
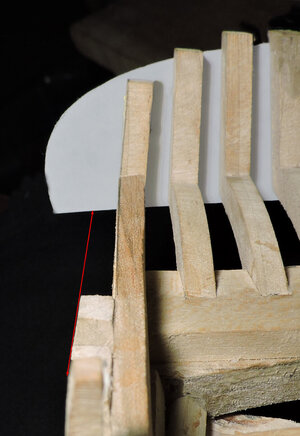