i read a lot of comments on kit instructions or lack there of. To make a bold statement you do not need instruction, for example a patient does not come with instructions a doctor "knows" what to do, a carpenter does not need detailed instructions for every house he builds because he is a "carpenter" and knows the construction of a building. Same with a Mason he knows how to lay brick or stone so he can build anything. This also applies to ship building if you are a shipwright and know and understand the basic principles you can build a ship be it from a kit or scratch.
From this point on the Tecumseth is built from ship building knowledge, logical construction methods and known ship building practices of the period. There are no "instructions to follow".
the deck structure is now complete and it looks like random beams and carlings but actually there is a logical reason why the carlings are where they are. A drawing of the deck layout did survive so we know what it looked like but there is no constructiuon detail and nothing survived on the wreck. The deck construction you see is a "reconstruction"
the red tinted areas are hatch ways and the companion way and skylight so those carlings frame in the five hatches so the coamings can sit on the beams and carlings. The blue tinited areas are where guns will be placed so those carlings are acting as supports for the heavy guns. I found it interesting how solid and strong the entire deck became once all the carlings were in place.
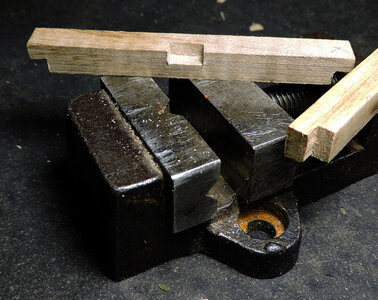
it is much easier cutting the joinery off the model and in a vice rather then and cutting the joinery on the model. You get clean and sharp joinery because you have more movement with the knife. you may wonder why bother with cutting a clean, square sharp notch when it will be covered? Well let me tell you
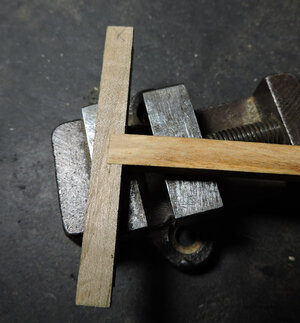
this is why, when the notch is clean and sharp the final fit is tight.
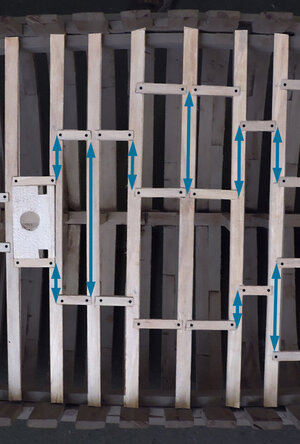
i chose to cut all the joinery on the model because all the carlings line up from beam to beam and with one another. So all the dots have to be exactly in the right place. Taking the deck apart and pulling out the beams to cut the notches for every carling seemed to be a real big problem making sure everything will line up from side to side. That is a lot of dots so i glued in the beams and placed carlings in one at a time right where they should go.
The model being at a large scale of 3/8 = a foot gave me enough room to work.
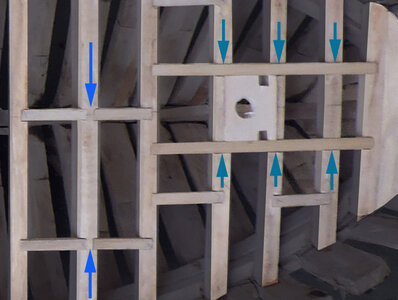
What we are looking ar here is builders license or "doing it my way" when two carlings are in line with each other it creates a space on the beam pointed to by the arrows on the left. That beam is wider than the rest of the beams because it is the one the gun will sit on. The rest of the beams that space is pretty small. On the right is a long carling and as you can see there is no space on the beams between the carlings. Some expert on deck construction may argue you can't do that carlings notch between beams from beam to beam they do not cross a beam.
Well i say so what my logic is these beams will take a lot of stress because of the mast, pin rail up right posts and the samson post where the bow sprit ends so to me it was logical to make a long carling notched over the beams locking them in from side to side and front to back. Then again some shipwright might think hum? good idea. Whatever! thats what i did.
all in all a final comment on building a deck it was more a feel of "woodworking" than assembling a kit. Personally this is why i scratch build to have to figure out what and how to do something and the fabrication of parts and wood working rather than assembling prefab parts.