- Joined
- Dec 1, 2016
- Messages
- 6,049
- Points
- 728
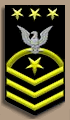
IMHO
I haven’t looked at all the ramifications of this sketch but here it is
.oh? i like it after work i will do a foam mockup of your idea it solves the issue of trying to bend that cap piece at the side.
thanks MavRick
I haven’t looked at all the ramifications of this sketch but here it is
.oh? i like it after work i will do a foam mockup of your idea it solves the issue of trying to bend that cap piece at the side.
thanks MavRick