- Joined
- Apr 20, 2020
- Messages
- 5,144
- Points
- 738
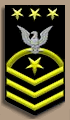
Hello dear friends
Tonight I returned to the ship, after practicing and learning the cnc machine. I was cutting the boards to the bottom deck. Unlike the practicum I decided not to place the deck in the center, instead I chose to build the decks in half, with the upper deck to be built on the opposite side to the lower deck so that in each part an opposite side of the ship would be seen. Hope it turned out nice and quality. Wishing us all a pleasant and enjoyable weekend.
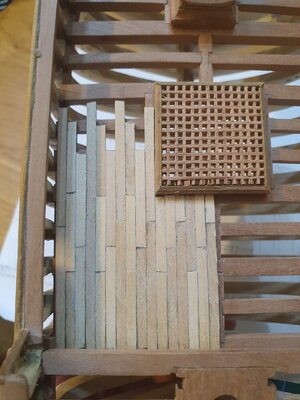
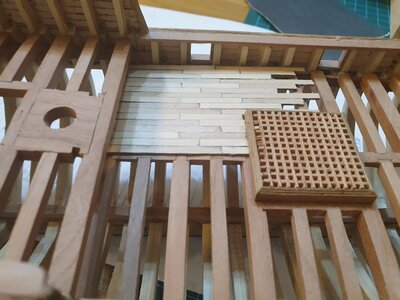
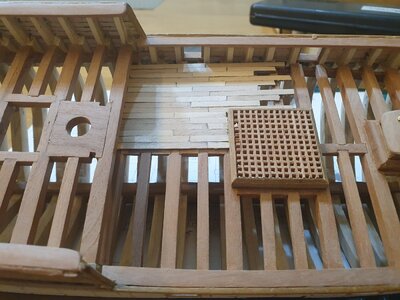
Tonight I returned to the ship, after practicing and learning the cnc machine. I was cutting the boards to the bottom deck. Unlike the practicum I decided not to place the deck in the center, instead I chose to build the decks in half, with the upper deck to be built on the opposite side to the lower deck so that in each part an opposite side of the ship would be seen. Hope it turned out nice and quality. Wishing us all a pleasant and enjoyable weekend.
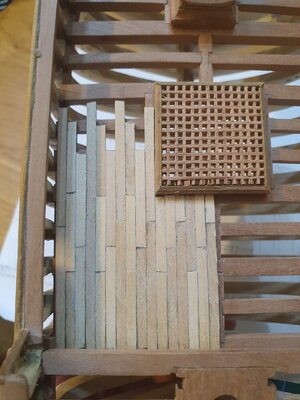
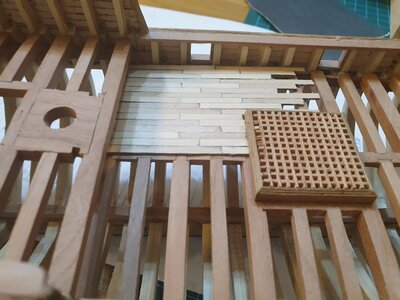
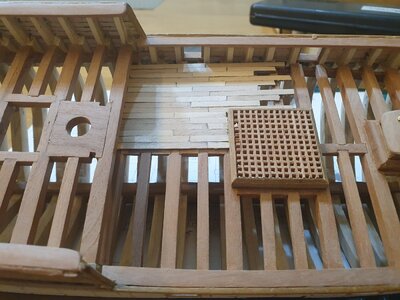