- Joined
- Dec 5, 2022
- Messages
- 470
- Points
- 158
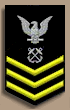
Thank you for your high rating. The answer to your question: yes, it is painted hornbeam wood. Black and blue hornbeam (or any other) is paint that is vacuum-painted through the wood. That is, wherever you cut it, it is the same color everywhere. This is very cool, since it looks like it is not painted, but the color can be any, even unnatural. And you can cut blanks of any shape.
By the way, I am surprised that only you paid attention to this color. I really liked it, and especially my wife.I was sure that there would be a lot of talk about this color, but no
Yes, of course, I understand. There is not a single image of Alert here. These photos are more on the topic of just sailing equipment and that I am already looking forward to working on the rigging. And I posted a separate thread on the Alert rigging and wrote and posted photos of rigging diagrams here. But anyway, thank you
By the way, this illustration clearly shows how two sloops were installed on the deck. This is not something you see often.
View attachment 529266
Hello Sergey,
I have seen wood in the colours yellow, red and blue (dyed maple). You are right, there are colours that do not look natural. This is not the case with your colour. The blue doesn't look artificial. I would like to use such veneers for my Athena. However, this requires absolutely precise processing. In other words, there must be no glue leaks and, of course, the planks must be lined up correctly without large gaps in between. I haven't dared to do that yet ... But maybe I need a little more time.
Your construction method is very accurate and impressive. I am a fan.


Best regards
Günther
