Thankyou Michael
I will say though that at first I thought the joints were a little prominent.This is due to the Epoxy.It leaves a dark line as opposed to wood glue.However,when I cleaned everything with white spirit which shows what the timber will look like when finished I was happier.
The reasoning behind Epoxy is that it leaves no glue stains that will show through the shellac to be applied later.Any Epoxy residue just blends into this finish.Before on other builds I have used wood glue but this is easier to remove from a conventional plank on bulkhead builds,on this it is a knightmare.You have to clean off with water,this and the moisture in wood glue swell the pear and stuff starts moving.Because of the zero water content in Epoxy you can get away without clamping things that you would have to using wood glue.
Moving on,some seemingly random pictures but I hope they will help explain what is next.Firstly I would add that I have lowered the waterline 2mm as the intersection on the rudder blade would result in a splice between Ebony and Pear in an awkward and aesthetically unpleasing place,right at the return of a scroll.
I have bit the bullet and had to go with getting numerous copies of the drawing to cut up and make templates.There are too many parts and pencil lines do not show up on Ebony.I am deviating from Frolich's approach of morticing the two timbers together and also from the two housing joints shown on the plan.I propose on drilling from the back and inserting brass pins epoxied in place.These are overscale but will not be seen inside or out when finished.I am undecided as to whether I illustrate the bolts on the cutwater's front edge.These could not be used for structural purposes as I cannot get a 1mm drill long enough to go through all the timber sections.If I could,I doubt it would follow the correct line,even with everything set up in my pillar drill.
The hard part here is the carved trailboard which is a very ornate piece of fret work.It is not solid but is more of a lattice as seen on Soleil Royal according to Berain's drawings.In order to prevent this very fragile piece from collapsing I am going to add a slim frame incorporated in the boxwood carving.This will fit in a channel in the prow timbers.The cutter to produce this channel is shown in one of the pictures.
This channel will need milling in the respective pieces before final assembly and the carving will also have to be fitted during assembly.I am reasonably proficient at carving,but this is not only going to stretch my ability but also going to take a considerable amount of time to produce.Some of the details are ridiculously small and it is a long time since I did the 1.6mm diameter faces on my Sovereign build
Kind Regards
Nigel
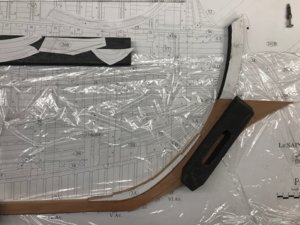
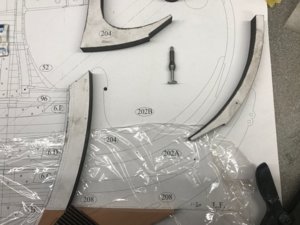
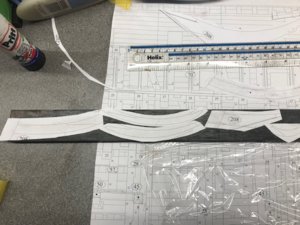
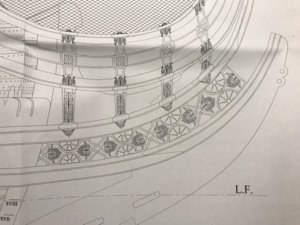