- Joined
- Dec 1, 2016
- Messages
- 6,010
- Points
- 728
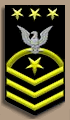
Dave am not sure were the roof over the balcony came in to play and I thought we was talking about the balcony itself.
yes we were talking about the floor of the balcony itself I just mentioned the roof because it too has to extend out.
yes we were talking about the floor of the balcony itself I just mentioned the roof because it too has to extend out.