After 1.5 weeks of holiday, back on the iMac. Not with the 3D drawing, but with the preparation for making a test frames.
I can divide this preparations into 3 chapters.
1:
My starting point is the old drawing of the half-drawn 'Grootspant'/ Main frame. It is a scan of the old drawing from the yard "A. de Jong" and was included in the SZB files. It states that the width is 6.60 M. Not for the half, but for the entire frame.
Copied and mirrored that half frame in Photoshop:
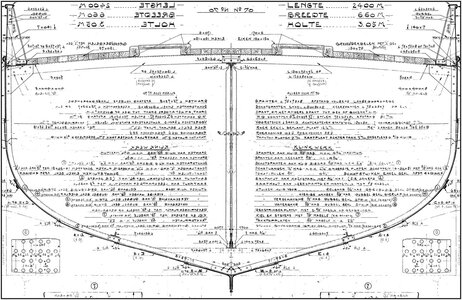
6.60 meters is 13.2 cm in scale 1:50. I brought in the file the outside dimensions of the entire frame to 13.2 cm. Printed out it in also 13.2 cm wide. I can now use that print to make a mold.
2:
The drawing of the main frame also shows almost all the dimensions of the individual parts, such as the L-profiles for the frame but also the patterns of the rivets etc.
I also converted those dimensions from 1:50 and selected various Evergreen strips, profiles and sheet material. The order has gone out.
3:
The files also include a drawing of the 3 frames with watertight bulkheads. I will also make the largest of these, frame 39, as a test, because then I will know whether the ordered sheet material can be used in terms of thickness/thinness:
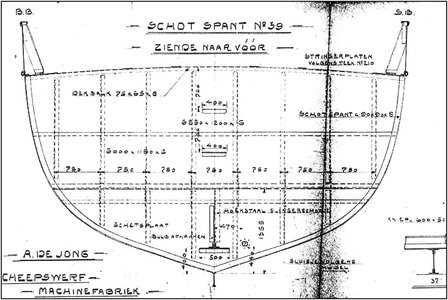
Also a scan of an old drawing of yard " A. de Jong" and part of the SZB files.
There are no dimensions in that image.
Based on the line plan I can now derive dimensions:
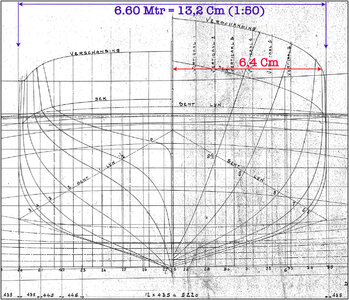
This is the part with the drawn Station Lines.
Right, seen from the front: 9½, 9, 8, 7, 6 and 5
Left, seen from the back: 0, ½, 1, 2, 3, 4 and 5.
-In blue: The largest width is 6.6 meters, because of the size of the Grootspant = 13.2 cm. That are both Station Lines '5' drawn on the left and right side.
On the line plan of the longitudinal section I see that this Station Line '5' is drawn between frame '27' and '28'. For the time being I assume that both of these are the Grootspanten / Main Frames.
-In red: I can now measure half the frame '7' and that is 6.4 cm = 12.8 cm in its entirety.
I chose Station Line '7' because this Station Line is drawn on the aforementioned line plan just behind frame '39'.
Now I can bring the drawing of the frame '39' to the dimensions 12.8 cm and also print it out to that dimension.
To be sure, the main frame was placed on the image of the lines plan in Photoshop:
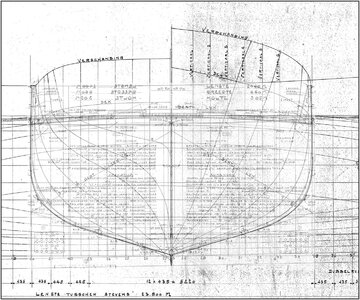
I placed the 2 drawings in 2 separate layers. And in Photoshop I can adjust the opacity per layer. Possibly not completely clear, but still placed to show the entire process.
It's a matter of check, check, double check.
Now just wait until the Evergreen material arrives.
In the meantime, continue with the 3D drawing.
Regards, Peter