For the 2nd test, I started working with the watertight bulkhead, frame 39. Cut a test plate of 16 cm wide and glued the drawing of the frame on it:
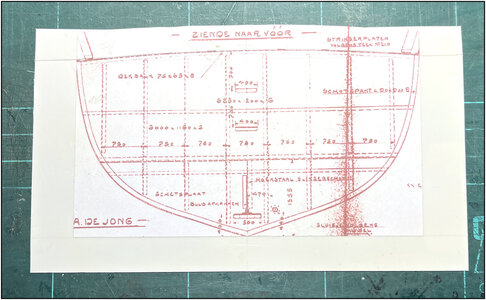
The point where the frame meets the keel beam is glued 12.5 mm from the bottom. That will be the starting point for all the frames.
Cut as precisely as possible along the outer edge:
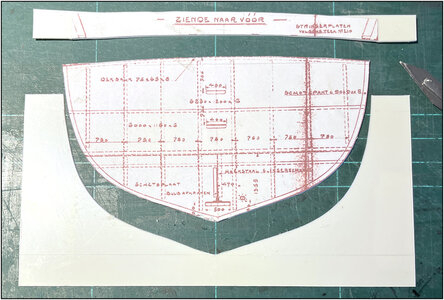
The top of the plate depends on the top of the frame. That depends on the height of the deck that has a sheer.
Because the profile will go around the cut-out mold, first cut off a thin edge:
The watertight bulkhead is reinforced with cross-placed profiles:
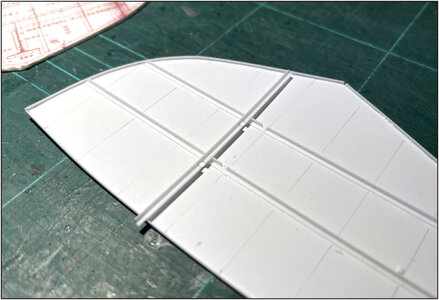
To make them coincide, both cut out a piece.
Then they both come to rest flat on the plate of the bulkhead:
Then it will look like this:
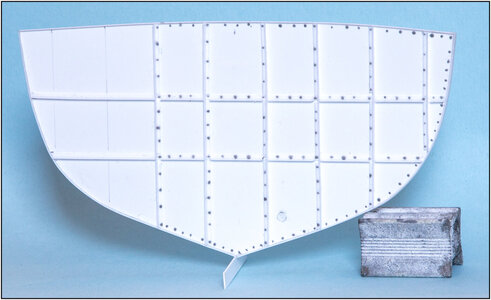
I was through my first bag of 1.5x1.5 cm profiles.
Still not happy with tipping the rivets with the (grayed) glue. Still too much difference in size.
Coincidentally, Maarten
@Maarten had asked yesterday whether applying the plates would not put too much tension on the frame. I didn't want to reveal it, but I was just doing that.
A first flat piece was applied at the height of the deck beam:
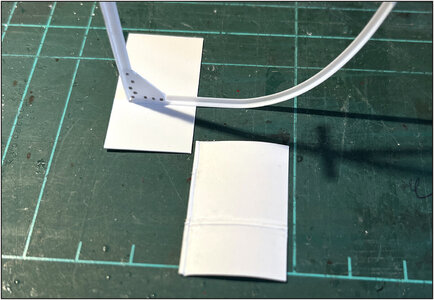
The second one is bent at the beginning of the curve. This is also heated against the warm side of the kettle. Also added a small flanged edge at the top.
The old drawing clearly shows that the plates are installed from the top down. The overlap therefore extends upwards.
Perhaps the flanges are not necessary and not used with the original. I just wanted to test it.
The hull is fitted with 6 rows of skin plates on 1 side:
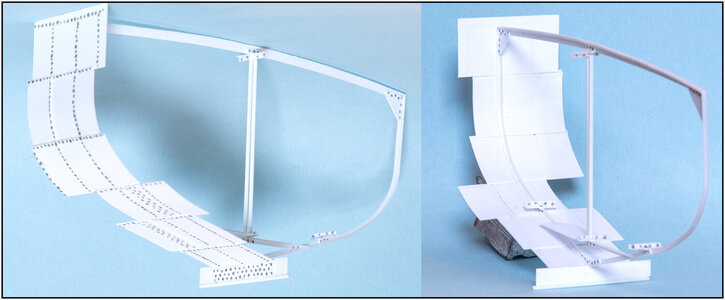
Tried different overlaps. From narrow ones with the width of 1 rivet and the wider ones with 3 rows.
The profile on the side remains neatly in shape.
I gave myself a hard time on the outside by putting rivets. I still have to find a mode that I'm happy with. Rivets have also been placed on various parts every 9.5 mm, the distance between the frames.
I used 0.25mm / .01” plate here. As mentioned, I will probably start with the bow during construction. Then more deformations are needed. I may then use the 0.12 mm / .005” plate.
Now start spraying to see how the whole thing turns out.
Regards, Peter