The black painted parts provide beautiful accents:
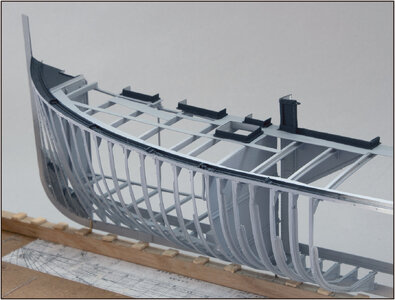
If the hatches, superstructures and planks are installed later, only the flat black parts will be visible.
The unforgivable macros show that the rivets are still visible in black:
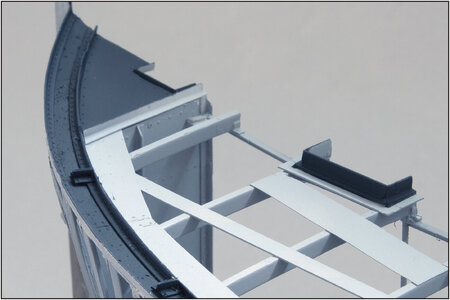
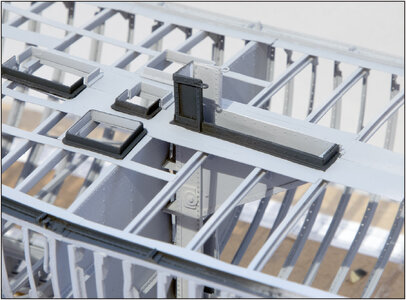
The photos have to be slightly overexposed, otherwise the matte black with the rivets will not stand out.
The contrast between the two parts will only increase:
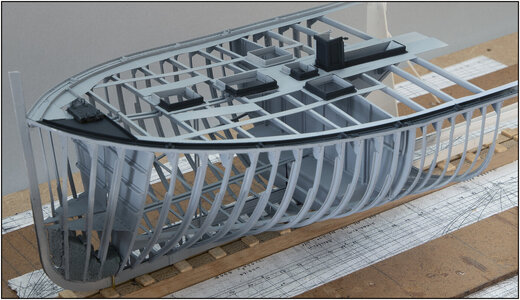
The starboard part is and remains only the pure construction.
Regards, Peter
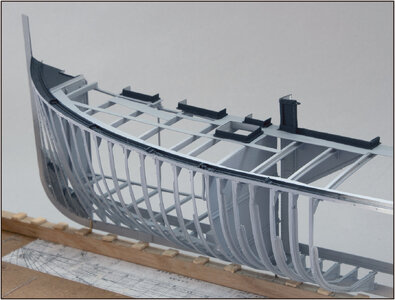
If the hatches, superstructures and planks are installed later, only the flat black parts will be visible.
The unforgivable macros show that the rivets are still visible in black:
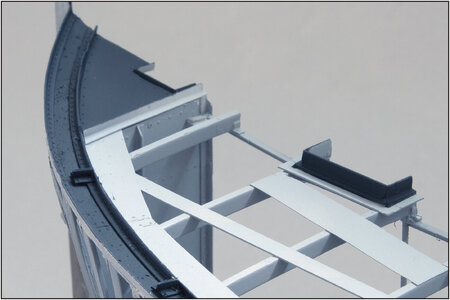
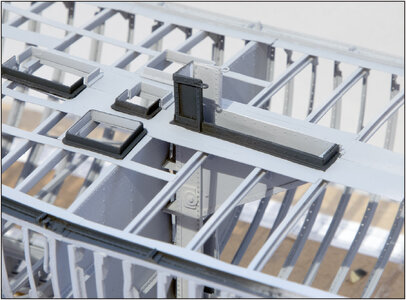
The photos have to be slightly overexposed, otherwise the matte black with the rivets will not stand out.
The contrast between the two parts will only increase:
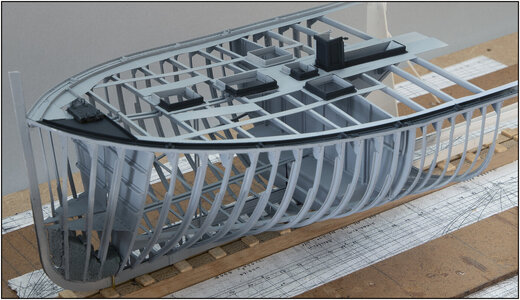
The starboard part is and remains only the pure construction.
Regards, Peter
Last edited: