The time has come to embark on my NEW build - The HMS Victory using the POF wood kit of Caldercraft (Jotika). As most would know, HMS Victory remains one of the most 'modelled' of all model ships. Like the ship Vasa, it exists today, can be physically touched/seen and examined (albeit currently undergoing a MAJOR restoration at Portsmouth with an estimated £45m price tag - Refer to the Royal Navy site here).
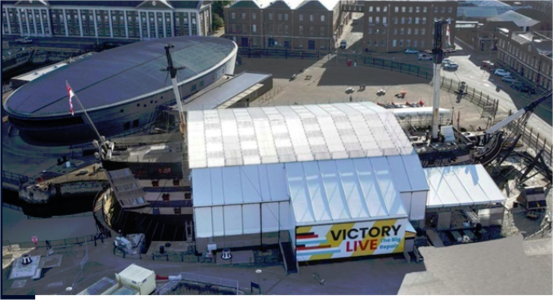
One of the other benefits of having the physical ship existing is that there is a plethora of research material, books, plans and people available to ask questions, not only here at SOS but also the British Royal Navy Conservation foundation where a detailed Conservation Log is being provided - A bit like a Build Log only applicable to the REAL ship!!).
My Build Log here commenced as a gift I received while completing my Vasa model about half way through the 'Covid years' from The Admiral. With transition from work to retirement, plus the Covid lockdowns and also maintaining a working farm (in the reaches of the Snowy Mountains of southeast New South Wales, Australia), my time was limited to commence the build, but things have cleared a little now and I have some time, so the start has begun. As is my habit, I like to approach things carefully and so with a bit of research, and after a few searches of this forum (SOS), I noticed that although there are MANY entries and Build Logs for the Victory, strangely, there are actually not many describing the Caldercraft 1/72 wooden kit on Ships of Scale. To illustrate this, on the recently provided Index of Wooden Ships, there are 124 Victory build entries (or similar). Of these 124, there are SEVEN which I can find that are specifically related to the Caldercraft Kit and of these only 5 are actual Build Logs!!
One of these by Hoss6262, exceptionally describes the entire kit, its 15 kg of enclosed material and all the exceptionally well prepared cut-out sheets etc. This is an expensive kit, but you pay for what you get. The quality is excellent, the parts fit together with very tight tolerances (and in some cases, too tight, as I will explain) and I have no complaint about the professionalism in preparing this kit. Even registration of the kit with the manufacturers, Jotika, brings benefits if parts require replacement or updating.
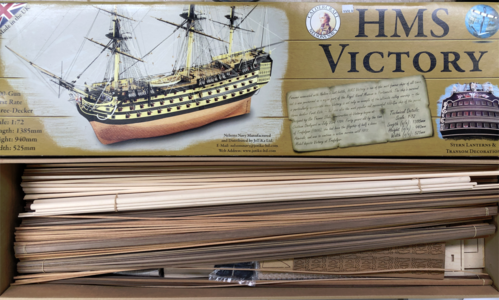
One of the other Build Logs (plus a comprehensive set of Youtube videos) has been provided by Paul1958 (a fellow Aussie!!) and this has proved to be exceptionally useful. I will not attempt to emulate Paul's excellent work, but on the way through the build, I will refer to his work, but also add a number of observations and comments of my own which might assist following builders.
So to start. I commenced by substantially modifying my 'workshop dry dock' after the Vasa build, to accommodate this bigger build and larger ship (both in scale and overall size). One of the things I did was change around the build area which meant I had the luxury of TWO desks with a 1.0 metre gap in the middle with a swivel chair, and the 'build desk', being an extended kitchen bench top that was considerably longer than the model, but which also allowed me to access the ship on BOTH sides. However as an added advantage (and one I found exceptionally useful with the Vasa build), was the use of a baseboard with keel clamps (similar to Paul1858's dock), but mounted on a large 'Lazy Susan'. A Lazy Susan is a circular, roller bearing mounted 'plate' which can be easily and cheaply purchased (Google 'Lazy Susan'). A Lazy Susan is a turntable (rotating tray) placed on a table or countertop to aid in distributing food, but in our case, provides the ability to simply rotate our baseboard-mounted ship which can then be rotated easily around the vertical axis.
A little unconventionally, but a good place to start, I wanted to eventually mount the Victory on a baseboard for display. The Manual describes the use of three 1/8" brass rods, drilled into the central keel area where brass rods can be inserted to mount the finished ship. I wanted something a little more sturdy, and so in the keel, I drilled three holes but then mounted three cross-threaded round push-through nuts (as obtained and used from Ikea furniture), and these then allowed me to insert thin screws (size M5), and actually bolt down the ship once mounted.
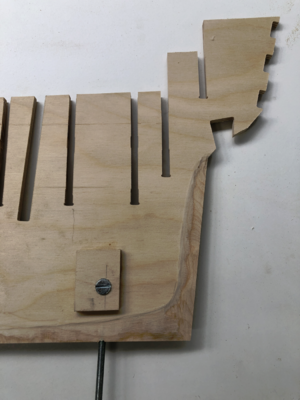
I reinforced these nuts with additional 5mm ply (making sure their placement did not interfere with the bulkheads on either side, and this allows a VERY rigid and firm securing of the model along its keel. Note in the photo above too, I have already chamfered the base ends of the keel as described on Plan 2 of the kit. This MUST be done early in the build, and I recommend it be done BEFORE placing any bulkheads as it means you are working on a flat surface to sand and Dremel machine off the required chamfer. I ALSO recommend that you LEAVE OFF the stern walnut keel extension and base keel at this time. The stern walnut will be applied later when the planking is completed to make a neat and clean finish, but the base keel stern walnut piece can be left until just before first planking. So, the mounted centre keel/spine is as shown below. Note the three mounting nuts, plus the bracket supports (as used by Paul1958 in his first Youtube video).
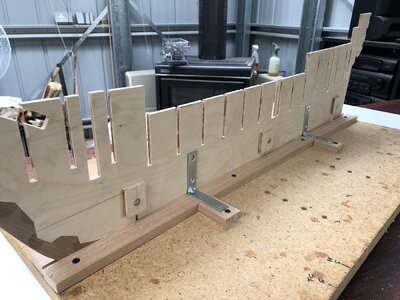
The NEXT stage is the placement of the bulkheads. I will leave this to the next build log entry.
Regards,
PeterG
Expended hours: 32 hours.
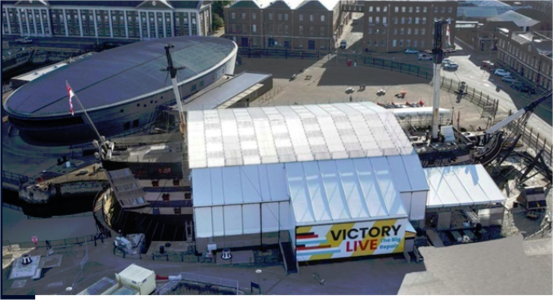
One of the other benefits of having the physical ship existing is that there is a plethora of research material, books, plans and people available to ask questions, not only here at SOS but also the British Royal Navy Conservation foundation where a detailed Conservation Log is being provided - A bit like a Build Log only applicable to the REAL ship!!).
My Build Log here commenced as a gift I received while completing my Vasa model about half way through the 'Covid years' from The Admiral. With transition from work to retirement, plus the Covid lockdowns and also maintaining a working farm (in the reaches of the Snowy Mountains of southeast New South Wales, Australia), my time was limited to commence the build, but things have cleared a little now and I have some time, so the start has begun. As is my habit, I like to approach things carefully and so with a bit of research, and after a few searches of this forum (SOS), I noticed that although there are MANY entries and Build Logs for the Victory, strangely, there are actually not many describing the Caldercraft 1/72 wooden kit on Ships of Scale. To illustrate this, on the recently provided Index of Wooden Ships, there are 124 Victory build entries (or similar). Of these 124, there are SEVEN which I can find that are specifically related to the Caldercraft Kit and of these only 5 are actual Build Logs!!
One of these by Hoss6262, exceptionally describes the entire kit, its 15 kg of enclosed material and all the exceptionally well prepared cut-out sheets etc. This is an expensive kit, but you pay for what you get. The quality is excellent, the parts fit together with very tight tolerances (and in some cases, too tight, as I will explain) and I have no complaint about the professionalism in preparing this kit. Even registration of the kit with the manufacturers, Jotika, brings benefits if parts require replacement or updating.
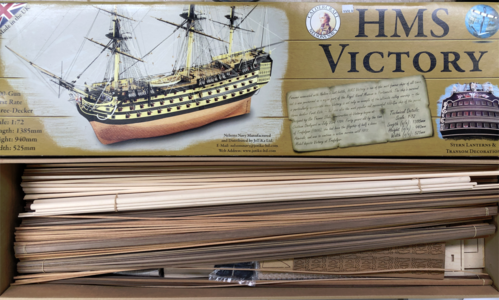
One of the other Build Logs (plus a comprehensive set of Youtube videos) has been provided by Paul1958 (a fellow Aussie!!) and this has proved to be exceptionally useful. I will not attempt to emulate Paul's excellent work, but on the way through the build, I will refer to his work, but also add a number of observations and comments of my own which might assist following builders.
So to start. I commenced by substantially modifying my 'workshop dry dock' after the Vasa build, to accommodate this bigger build and larger ship (both in scale and overall size). One of the things I did was change around the build area which meant I had the luxury of TWO desks with a 1.0 metre gap in the middle with a swivel chair, and the 'build desk', being an extended kitchen bench top that was considerably longer than the model, but which also allowed me to access the ship on BOTH sides. However as an added advantage (and one I found exceptionally useful with the Vasa build), was the use of a baseboard with keel clamps (similar to Paul1858's dock), but mounted on a large 'Lazy Susan'. A Lazy Susan is a circular, roller bearing mounted 'plate' which can be easily and cheaply purchased (Google 'Lazy Susan'). A Lazy Susan is a turntable (rotating tray) placed on a table or countertop to aid in distributing food, but in our case, provides the ability to simply rotate our baseboard-mounted ship which can then be rotated easily around the vertical axis.
A little unconventionally, but a good place to start, I wanted to eventually mount the Victory on a baseboard for display. The Manual describes the use of three 1/8" brass rods, drilled into the central keel area where brass rods can be inserted to mount the finished ship. I wanted something a little more sturdy, and so in the keel, I drilled three holes but then mounted three cross-threaded round push-through nuts (as obtained and used from Ikea furniture), and these then allowed me to insert thin screws (size M5), and actually bolt down the ship once mounted.
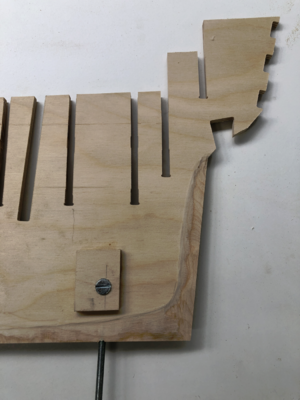
I reinforced these nuts with additional 5mm ply (making sure their placement did not interfere with the bulkheads on either side, and this allows a VERY rigid and firm securing of the model along its keel. Note in the photo above too, I have already chamfered the base ends of the keel as described on Plan 2 of the kit. This MUST be done early in the build, and I recommend it be done BEFORE placing any bulkheads as it means you are working on a flat surface to sand and Dremel machine off the required chamfer. I ALSO recommend that you LEAVE OFF the stern walnut keel extension and base keel at this time. The stern walnut will be applied later when the planking is completed to make a neat and clean finish, but the base keel stern walnut piece can be left until just before first planking. So, the mounted centre keel/spine is as shown below. Note the three mounting nuts, plus the bracket supports (as used by Paul1958 in his first Youtube video).
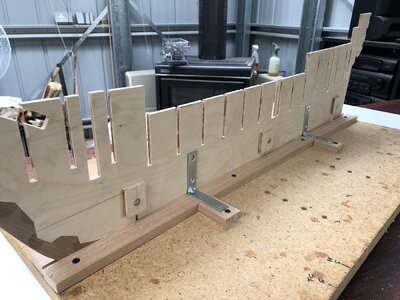
The NEXT stage is the placement of the bulkheads. I will leave this to the next build log entry.
Regards,
PeterG
Expended hours: 32 hours.
Last edited: