I cannot say that I am an expert at the lathe, but I can tell you that this is
not for a beginner's first turn operation. Therefore, I present the pulleys. The openings of the bitts are a little too large, but it will have to do. When they are finished, then all votes can be cast. Sorry for no documentation on how I made these.
I will say this. I used a 6mm steel stock.
1) Turned down to 5mm.
2) Then drilled a 1.5mm hole into the stock about 40mm deep to have a one pass hole for all pulleys.
3) used a 60° tool bit to make grooves 1mm depth. +/1 about .1mm give or take (can't tell anyway)
4) used a straight cutoff tool to part each one. (each one at a time).
5) repeat the process over and over until you have made each one.
After a much-needed break, I will mount the pulleys. Time invested is about 4 hours straight. Having two sheaves in-one is probably not accurate and I get that. It is mostly for representation anyway. To make two sheaves for each bit would require even more time and effort than I would wish to apply here. And there could only be one sheave per bitt, so don't ask why I chose to do it this way.
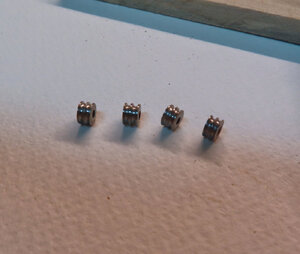