- Joined
- Jan 9, 2020
- Messages
- 10,523
- Points
- 938
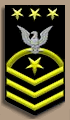
Hi Phil. What can I say? Out of necessity, comes innovation!Where'd you grow that extra hand?

![]() |
As a way to introduce our brass coins to the community, we will raffle off a free coin during the month of August. Follow link ABOVE for instructions for entering. |
![]() |
Hi Phil. What can I say? Out of necessity, comes innovation!Where'd you grow that extra hand?
Thank you my dear friend. The Admiral, as always has been great. But I have to tell you a little story. I said to her that when the time comes to move, the Haarlem, the Sampan, Bluenose, the RC Seaducer, the 1935 Bowman Steamboat and the 1900 Carette Electric Speedboat has to go to her new apartment. I will only take my tools and the WB. Her response? "No, you can take all the others, I want the WB!"
Well, after all Heinrich, she did have a hand in itThank you my dear friend. The Admiral, as always has been great. But I have to tell you a little story. I said to her that when the time comes to move, the Haarlem, the Sampan, Bluenose, the RC Seaducer, the 1935 Bowman Steamboat and the 1900 Carette Electric Speedboat has to go to her new apartment. I will only take my tools and the WB. Her response? "No, you can take all the others, I want the WB!"
Jan the Admiral knows; everything - except the WB - is negotiable.NEGOTIATIONS, NEGOTIATIONS
![]()
That is true Ron, but following that rule, I would not have any ship that I can take with me.Well, after all Heinrich, she did have a hand in it![]()
Thank you Peter. I am also satisfied with the outcome and glad that I could finish this part. I will tell the admiral that she has a lovely hand!That is looking a great ‘gepotdekselde’ wall with both doors, Heinrich. With the lovely third hand of your Admiral.
And a nice picture in natural day light!
Regards, Peter
Thank you so much Johan. The admiral always says she is happy when I am happy - but, she will soon let me know if there is something that she is not happy with! If I have completed something and it passes her QC, then I can also be assured it's OK!An accomplishment you (and the Admiral) can be proud of! Kudos.
Indeed Johan. And, she has a great eye. She was quick to point out that something is missing above the two doors. Only after I showed her this picture of Piet's build with the extra beam that is placed after the bulwarks had been cut to shape, was she satisfied.The Admiral's QC; a hard one to pass...![]()
Loving the doors and layered planks on the wall, it was on my mind to attempt scratch building something similar on my current build but the skills weren't quite up to it yet, now I would be confident to give it a go.Hello Everyone.
This really is my last update before I return to work - and let me tell you straight out - I found this to be a really difficult task to accomplish.
I wanted to finish the canopy by installing the front wall and doors. The goal at the end of this step was to have something similar to @pietsan Piet's final outcome.
View attachment 288870
Photograph: Piet Sanders
Piet's superb-looking front wall and door assembly.
View attachment 288871
Photograph: Piet Sanders. This may look like an easy assembly (and for some people it probably is, but I had my task cut out for me.
For this we will again need the laser sheet I showed you earlier.
View attachment 288872
PART C (marked with the green ticks): Already used.
Blue-marked Parts: Outer Wallposts
Yellow-marked Parts: Inner Wallposts
White-Crossed Parts: Doors.
Orange-marked Parts: Door Posts.
The instructions call for the outer wallposts (blue-marked parts) to be glued underneath the already mounted stanchion posts with the notched part facing forward towards the bow. The supplied part is too long and needs to be cut to the correct length at the TOP!
View attachment 288873
Here you van clearly see the difference between the cut-to-size outer wallpost and the one directly from the laser sheet. On the original one I had already scored the cutting line.
View attachment 288874
The outer wallpost has been glued underneath the stanchion post. The green rectangle indicates the bulwark overlap that will be cut to size and finished off later.
View attachment 288875
To make sure that I mount the wall post plumb, I fabricated a square that is small enough to fit in underneath the canopy.
With the outer wallposts mounted underneath the stanchion posts it was now time to test-fit the doors.
View attachment 288876
This is how the door comes out of the laser-cut sheet. Note that the door post still surrounds the door. Leave this as is for the time being.
Now what Piet has done is to glue two 6mm walnut strips behind both door and doorpost to ensure that it remains one, solid construction.
View attachment 288877
This is what Piet has done in his build. I have just overlaid these planks as means of illustration.
View attachment 288878
However, in my case, if I had used this method as above, the door was too high in relation to the canopy. (In this picture it actually looks as if the door is protruding above the company, but in reality that it was lying flush with the top edge.) Whilst I have seen one or two WB builders who used the doors as above, I was not happy to do so. Therefore, I went a different route.
View attachment 288879
I separated my door post from the door and cut off the bottom part. At the same time I stained the door post with Dark Oak – the fact that I had separated the two parts and stained the door post while not attached to the door, obviously prevented the stain from overflowing onto the door. After the stain had dried, I glued the door frame back around the door.
View attachment 288880
Here you can see my modified construction (on the left) compared to the standard kit one. Note that my modified door now was markedly lower compared to how it came out of the laser cut sheet.
View attachment 288881
Test-fitted, my modification had the desired effect as the door assembly now fits neatly underneath the upper edge of the canopy.
Now I could make a start by planking the sides (the area demarcated in red) using 1.5mm x 6mm walnut planks. They are planked in an overlapping (schotelende) way made easy by the notches in the outer wall post.
View attachment 288882
Before I started the planking though, I dry-fitted the door and then glued the inner wallpost into position - again making sure it was plumb and butted up tightly against the door.
View attachment 288883
With the two side walls planked up to this point. I could make a start with the center section.
View attachment 288884
At this point, I decided to glue the doors into the walls so that they were secure. I thought that that would make it easier then to close the gap off at the top.
But this obviously meant that I had to prepare the doors for installation and that meant hinges and door handles/knobs. I made a decision prior to the build, that I was not going to use any blackening fluid or paint. I could have used brass strips for the hinges, but against the very light-colored doors they just did not show up properly. I thus delved into my wood stash and cut two hinges out of very light-colored pear wood. The idea is this: I know that the tung oil, when applied, is not going to change the color of the door much, but tung oil darkens pear wood considerably. So when the whole assembly is treated with tung oil, the hinges will become a lot darker than what they are now while the doors will remain (more or less) the same color. It was thus more a case of insinuating the hinges rather than having sharply-defined hinges in place. The door knobs were easy - Kolderstok-supplied nails.
View attachment 288885
If the hinges do not work satisfactorily for me, I can always remove them and do something else. They are still easily accessible and since they are just tacked with PVA glue, removing them will be a cinch. Note the uneven lines at the bottom of the doors. They were sanded to fit in with the curvature of the deck.
With the doors in place, the top could be closed. Here I edge-glued two 1.5 x 6mm walnut planks together (the opening at the top was too big to use a single plank) and then filed out the openings for the door tops. This took ages to get it right.
View attachment 288886
And gluing that final clamp into position was even more fun. I quickly realized that I needed a third hand so I asked the Admiral (very nicely) to pull-up a chair opposite me and to provide the third hand/finger for an hour while I whispered sweet-nothings into her ear!
When the glue was dry, it was a case of filing and sanding the top edge of the plank flush with the top edge of the canopy. And finally, when all was said and done, this is where I am tonight.
View attachment 288891
View attachment 288892
Many many hours from now, I will go to bed a very happy Willem Barentsz builder. Never in my wildest dreams would I have imagined that I would get this far in two months. I have thoroughly enjoyed myself and my satisfaction of the build has only been surpassed by the wonderful participation of all of you. Until next time, take care, keep safe, cherish your loved ones and happy shipbuilding.
Thank you so much for the kind words , Richie! The overlapping planks were widely used on Dutch ships and sure adds a nice touch. There is also a simplified way of doing the overlapping wall as I have done on the Haarlem.Loving the doors and layered planks on the wall, it was on my mind to attempt scratch building something similar on my current build but the skills weren't quite up to it yet, now I would be confident to give it a go.
Thank you my friend - I always value your opinion, so I am glad you like it!Very nice job Heinrich !!!!
Cheers
Daniel
Hello my Dear Lawrence - thank you for your very generous compliments. Actually, I am not a fast builder at all - it's just that for the last two months, I could devote all my time to the build. I am glad that you like the results and that you enjoy the historical background. Your Bluenose is really looking great and I am looking forward to see how you progress. I sure will give Anna your message - and yes, it sure is great to have a supporting admiral along the way.Hello Heinrich, You truly amaze me at the speed at which you build along with those great results. Your build is looking very special with your great touch. Say hello to your Admiral for us ok, it sure is nice to have a helping hand along with a very sharp eye for over looked detail. Thanks for the very enjoyable history lesson, such detailed pictures, it is amazing just how these men could live in these conditions and still want to go back for more.
My sour thumps have improved a lot today but I think that I will give them another day before returning to the frame building on my YQ-Bluenose, thanks for your very helpful tips.
Regards Lawrence
Hello Bryian - I agree fully. The kit is of amazing quality and the excellent instructions (a 57-page, full-color instruction manual in Dutch, English and German and 1:1 plans) makes the whole building experience a pleasure!Hello Heinrich,
thats certainly a very impressive looking kit you are building. Well done so far.![]()
Judging from the pictures, they're not tapered or rabbeted.Thank you so much for the kind words , Richie! The overlapping planks were widely used on Dutch ships and sure adds a nice touch. There is also a simplified way of doing the overlapping wall as I have done on the Haarlem.
View attachment 289068
Step 1: Simply cut a piece of MDF, Triplex, or ply to size to fit the opening for which the wall is intended. make sure that you add a few extra millimeters on the sides and bottom.
Step 2: Measure the exact positions of the doors and glue the door frames into position.
View attachment 289069
Step 3: Check for a good fit between door frame and doors. If you are building from a kit, this should not be a problem.
View attachment 289070
Step 4: Start planking. On the Haarlem I used 1.5mm x 4mm strips which gave a "finer" effect to the wall compared to the 1.5mm x 6mm planks that I used on the Willem Barentsz. Either way, you want approximately 2mm of the plank to overlap the previous one, ensuring that there is sufficient surface for the glue to adhere to.
View attachment 289071
Step 5: Finishing. The few extra millimeters on the side allows the wall to be faired along with the rest of the hull prior to planking. The few extra mm on the bottom allow you to sand the bottom nicely into shape to conform with the deck.
So there you have it - it does take more time, but the results are just so much more authentic!