Enough deadeyes for a while.
Next project was the bell and belfry. I drilled out a 15 mm hole with forstner bit in a suitable block of jacaranda wood then cut the piece to size for the belfry roof.
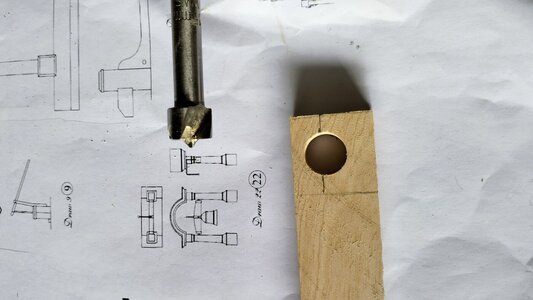
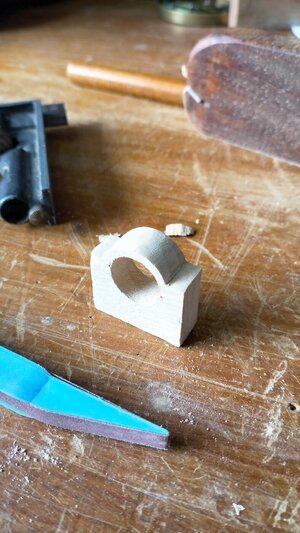
Next I turned the columns on my small lathe.
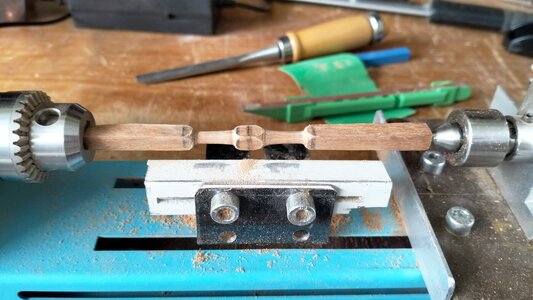
Dry fitted the parts and checked for size.
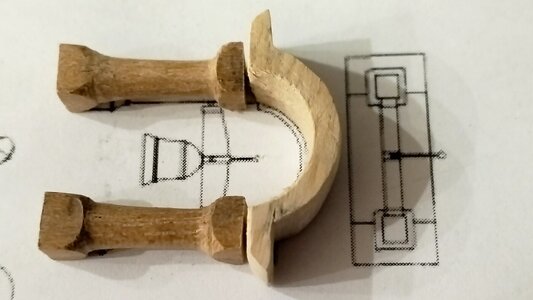
So far so good, but........
Next project was the bell and belfry. I drilled out a 15 mm hole with forstner bit in a suitable block of jacaranda wood then cut the piece to size for the belfry roof.
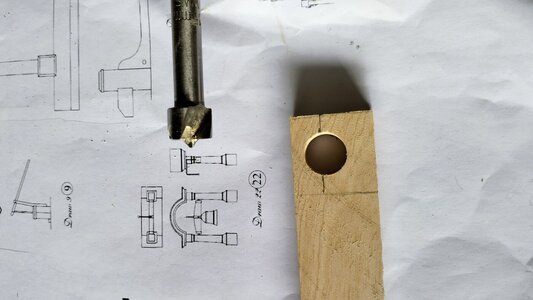
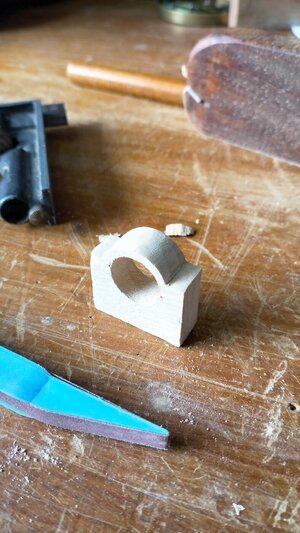
Next I turned the columns on my small lathe.
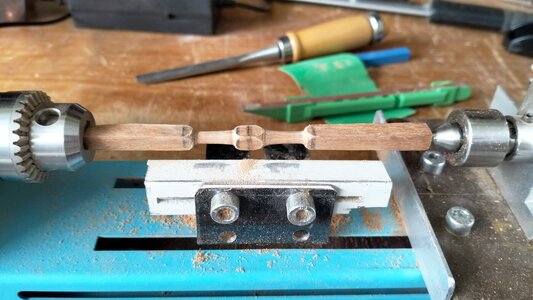
Dry fitted the parts and checked for size.
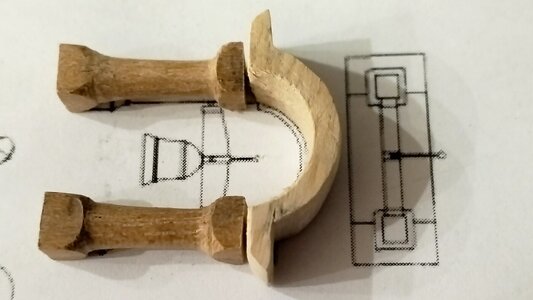
So far so good, but........