The beakhead bulkhead was made today, but it will not be not be permanently attached until the kit plywood bulkhead is completely removed. It was made in three layers of wood, so that when gun parts are cut, there will be no space between the inner and outer planking layers. Since the forecastle has a waisted profile when viewed from the front, with a slight flare at the top, a jig for making the beakhead bulkhead was made to create the double curve of the bulkhead using planks.
First, the overall shape of the curved bulkhead was established by the bottom piece of what will be a three-piece jig. This shape of this first piece was made using French curves and cut with a band saw. These pieces of made from balsa which will make cutting them away from the finished bulkhead later.
Knowing what the profile of the bulkhead allows the planks at the front edge of the foremast reinforcement to be trimmed by chisel cutting the line and removing the unwanted parts from the deck, all with a chisel bladed razor knife.
You can see the edge of the foremast reinforcement flush with the front surface of the jig piece.
The middle and top pieces of the jig are cut from balsa using a band saw. Note that the middle piece was cut and shaped to be at the level where the forecastle is the most narrow, so it is shorter than the ones above and below it.
Sticks of spare linden wood are CA glued to the back of the three jig forms to create the jig.
A few more sticks of linden wood are added to the jig to stiffen it.
The bulkhead is now built as follows. Sticks of 4mm wide pliable basswood are glued edge-to-edge to each other in vertical planks, but only glued to the middle form of the jig, not at the top or bottom. The three outboard basswood planks on each side are soaked into water and pre-curved. This is so they do not have any spring in them as they are glued to each other and the middle form of the jig.
Once all the planks are dry, the upper and lower forms of the jig are removed, but the center form is left glued to the planks to hold the shape of the bulkhead. The edges of the bulkhead are trimmed and sanded to fit the hull. Vertical trim made from thin mahogany sheet, are cut as glued to the outboard edges of the bulkhead. One these trim pieces is shown attached below.
Here the top view of the bulkhead held in place.
Here is the inside surface after sanding. You can see the waisted profile of the forecastle in the outboard edges. You can also see the middle jig form still in place.
Here is the front again.
The final planking pattern is borrowed from John McKay's design.
Horizontal mahogany planks were glued to exterior side.
Planks of mahogany are beginning to be layered on the inside.
Now that the final exterior planking and some of the inside final planking is finished, the bulkhead is stiff enough to remove the middle jig form.
The final planking on both sides is sanded and lacquered. However, it is not yet attached to the hull. Perfect fit!
Inside view. The cross support at the top of the forecastle and most of the the vertical plywood at the corner edges will be removed before the beakhead bulkhead is permanently attached, leaving a clean looking interior.
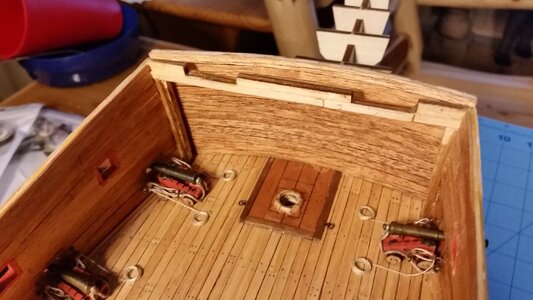