Thank you for your comment Paul. It's scary when you think back at the history in this hobby you and I have!! However, you are correct, the aesthetic appeal is probably the most important, but so too is accuracy to honour the original, which after all, we are trying to emulate. So I asked myself the question you asked, and the answer was 'No!! I am not happy with it." This meant a rethink and so a bit more research was required and as you said, there is a LOT of controversy about it.
"HMS Victory is undergoing a major refit and renovation at the moment. As part of this exercise, there has been some intense research to determine the exact colours she was at Trafalgar. She has now received her new coat of paint, and this has left many somewhat surprised. Despite wearing the common yellow ochre for many years, her stripes are now a pale pink ("salmon", "peach", "pale red" depending on your perception). This is not a joke - the best estimate is this is the colour she showed in 1805. A smaller change is that the font used for her name on the stern will also be modified."
An interesting forum discussion about the re colouring here.
I guess this poses a challenge for all those models of Victory out there, especially those that have taken great pains to depict the ship as she was at Trafalgar. UK readers can see a TV report on the Meridian TV website, but I don't think that is available outside the UK.
For example, one post has the colours as:
Revell 36135 Flesh for the new light (yellow) bands on the hull
Revell 36109 Anthracite for the 'black' bands on the hull.
Humbrol 71 Oak for the masts and
Humbrol 132 Satin Red for the cannon ports.
A second is "This is the basis of our choice: a reply from the (Victory) restoration team to our colour request.
"The pantone colour codes, as supplied by the Historic Ships Conservation Team for the hull are below. You can view the shades for reference at:
http://ncscolour.com/products "
Victory Hull Ochre. NCS S 3020-Y40R
The hull black is : NCS S 8500-N
Now if you Google search NCS S 3020-Y40R, you get the colour image as below:
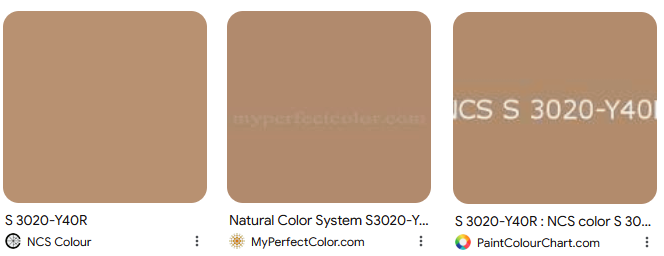
To me, these are ALL too brown, given the Yellow and Brown Ochre typically quoted as the ship colour of today. We also have to be mindful of the colours the ship has been over time. At the time of Trafalgar, eg from the Portsmouth Historic Dockyard in 2015 "Careful research has shown that she was painted externally in a combination of pale yellow and dark grey at the time of her famous victory, when Admiral Lord Nelson was fatally wounded. It would have been the Captain, Thomas Hardy, Nelson's trusted right-hand man, who was responsible for the painting of the ship."
An older (10 years old) article of interest is: The bumble-bee stripes of orangey brown and black of one of the most famous ships in the world, Horatio Nelson's HMS Victory on which he fought and died at the battle of Trafalgar in 1805, may have to be repainted after a team of historic paint detectives recovered hundreds of fragments of the original paint surfaces.
"What you see today is largely an early 20th century invention of what an 18th century warship looked like," said Michael Crick-Smith, a founder with his partner Ian Crick-Smith of the conservation institute at Lincoln University specialising in historic decorative finishes.
The pair claim that the colour they describe as "that hideous orange" is part of much later attempts to restore the ship when it had become a symbol of British naval power. The cherished legend is that it was repainted in his favourite colours at Nelson's orders, when the already elderly ship, launched in the 1760s when he was just a school boy, was refitted as his flagship.
But the Crick-Smiths' analysis – which in some places involved disentangling 72 layers of paint – suggests the hull was originally mostly black, with a lot of varnished timber above the water line. It was later partly repainted in an ochre shade, probably before Nelson took it over, but a much paler colour than the present vivid shade.
The orlop deck, where desperate attempts were made to save Nelson's life after a French sniper's bullet went through his shoulder and lungs and lodged in his spine, leaving him drowning in his own blood, was a pale creamy stone colour. The surgeon's cabin and the other small cabins on that deck were a surprisingly grand two shades of blue – good quality paint, compared to the cheap limewash and poor quality oil paint used in much of the ship.
The spaces now shown as Nelson's admiral's cabin, and the captain's cabin of Thomas Hardy (the "kiss me, Hardy" in whose arms Nelson died) are entirely comparatively modern reconstructions, but the Crick-Smiths are convinced from contemporary sources that they would have been much plainer, and probably painted a light blue.
"These were working spaces, not country houses at sea as they appear now," Michael Crick-Smith said.
The good news for the current guardians of the ship, the National Museum of the Royal Navy at Portsmouth Historic Dockyard, is that the Crick-Smiths discovered a remarkable amount of original material.
The upper decks are almost entirely reconstructions, but on the lower decks they discovered mainly original timber and hundreds of patches of original paint, dating all the way back to the very first paint scheme in 1765.
They also picked through a warehouse full of thousands of samples of timber removed from the ship in generations of repairs, and found many more. One sample of the ochre paint – "diabolical quality", Ian Crick-Smith said - came from an old capstan which was once used as a plinth for a bust of Nelson at Windsor Castle.
The Crick-Smiths came to the project after a heated Twitter exchange about some of the most unusual objects ever brought to the BBC's Antiques Roadshow: two battered wooden columns, claimed to have been taken from Victory at the period of the battle. Unfortunately their work demolished the claim: the timbers are from a ship, but not Victory.Their research is part of the most comprehensive restoration project since the ship was built at Chatham and the findings of the research will be taken into account.
For an excellent photo montage of HMS Victory with photos taken on a very bright sunny day is the album link here by Rob Durant.
Below is the current restoration colour which you can see is quite different to the NCS colour scheme Ochre above, but also very different to the hull colour ochre as in the terracotta ochre images before about 2017:
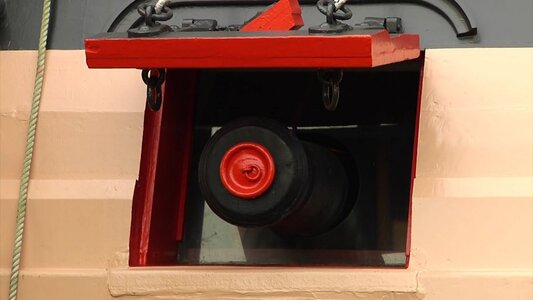
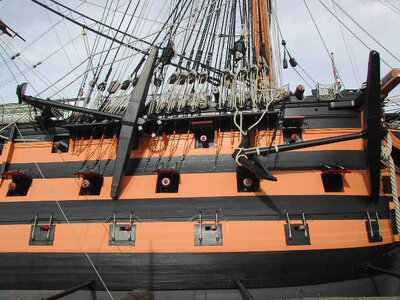
OK, so where does that leave me and my painting? Aesthetically, I am not happy, so I think a lighter, more yellow finish is to be applied. I will post some images as I go.
Best Regards,
PeterG
"HMS Victory is undergoing a major refit and renovation at the moment. As part of this exercise, there has been some intense research to determine the exact colours she was at Trafalgar. She has now received her new coat of paint, and this has left many somewhat surprised. Despite wearing the common yellow ochre for many years, her stripes are now a pale pink ("salmon", "peach", "pale red" depending on your perception). This is not a joke - the best estimate is this is the colour she showed in 1805. A smaller change is that the font used for her name on the stern will also be modified."
An interesting forum discussion about the re colouring here.
I guess this poses a challenge for all those models of Victory out there, especially those that have taken great pains to depict the ship as she was at Trafalgar. UK readers can see a TV report on the Meridian TV website, but I don't think that is available outside the UK.
For example, one post has the colours as:
Revell 36135 Flesh for the new light (yellow) bands on the hull
Revell 36109 Anthracite for the 'black' bands on the hull.
Humbrol 71 Oak for the masts and
Humbrol 132 Satin Red for the cannon ports.
A second is "This is the basis of our choice: a reply from the (Victory) restoration team to our colour request.
"The pantone colour codes, as supplied by the Historic Ships Conservation Team for the hull are below. You can view the shades for reference at:
http://ncscolour.com/products "
Victory Hull Ochre. NCS S 3020-Y40R
The hull black is : NCS S 8500-N
Now if you Google search NCS S 3020-Y40R, you get the colour image as below:
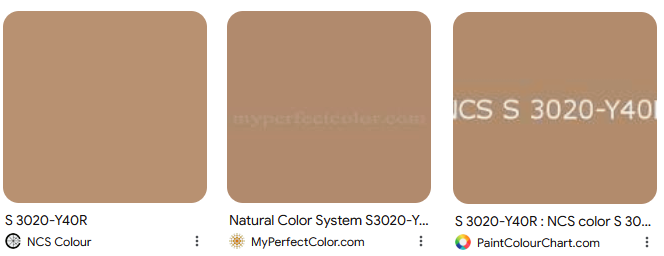
To me, these are ALL too brown, given the Yellow and Brown Ochre typically quoted as the ship colour of today. We also have to be mindful of the colours the ship has been over time. At the time of Trafalgar, eg from the Portsmouth Historic Dockyard in 2015 "Careful research has shown that she was painted externally in a combination of pale yellow and dark grey at the time of her famous victory, when Admiral Lord Nelson was fatally wounded. It would have been the Captain, Thomas Hardy, Nelson's trusted right-hand man, who was responsible for the painting of the ship."
An older (10 years old) article of interest is: The bumble-bee stripes of orangey brown and black of one of the most famous ships in the world, Horatio Nelson's HMS Victory on which he fought and died at the battle of Trafalgar in 1805, may have to be repainted after a team of historic paint detectives recovered hundreds of fragments of the original paint surfaces.
"What you see today is largely an early 20th century invention of what an 18th century warship looked like," said Michael Crick-Smith, a founder with his partner Ian Crick-Smith of the conservation institute at Lincoln University specialising in historic decorative finishes.
The pair claim that the colour they describe as "that hideous orange" is part of much later attempts to restore the ship when it had become a symbol of British naval power. The cherished legend is that it was repainted in his favourite colours at Nelson's orders, when the already elderly ship, launched in the 1760s when he was just a school boy, was refitted as his flagship.
But the Crick-Smiths' analysis – which in some places involved disentangling 72 layers of paint – suggests the hull was originally mostly black, with a lot of varnished timber above the water line. It was later partly repainted in an ochre shade, probably before Nelson took it over, but a much paler colour than the present vivid shade.
The orlop deck, where desperate attempts were made to save Nelson's life after a French sniper's bullet went through his shoulder and lungs and lodged in his spine, leaving him drowning in his own blood, was a pale creamy stone colour. The surgeon's cabin and the other small cabins on that deck were a surprisingly grand two shades of blue – good quality paint, compared to the cheap limewash and poor quality oil paint used in much of the ship.
The spaces now shown as Nelson's admiral's cabin, and the captain's cabin of Thomas Hardy (the "kiss me, Hardy" in whose arms Nelson died) are entirely comparatively modern reconstructions, but the Crick-Smiths are convinced from contemporary sources that they would have been much plainer, and probably painted a light blue.
"These were working spaces, not country houses at sea as they appear now," Michael Crick-Smith said.
The good news for the current guardians of the ship, the National Museum of the Royal Navy at Portsmouth Historic Dockyard, is that the Crick-Smiths discovered a remarkable amount of original material.
The upper decks are almost entirely reconstructions, but on the lower decks they discovered mainly original timber and hundreds of patches of original paint, dating all the way back to the very first paint scheme in 1765.
They also picked through a warehouse full of thousands of samples of timber removed from the ship in generations of repairs, and found many more. One sample of the ochre paint – "diabolical quality", Ian Crick-Smith said - came from an old capstan which was once used as a plinth for a bust of Nelson at Windsor Castle.
The Crick-Smiths came to the project after a heated Twitter exchange about some of the most unusual objects ever brought to the BBC's Antiques Roadshow: two battered wooden columns, claimed to have been taken from Victory at the period of the battle. Unfortunately their work demolished the claim: the timbers are from a ship, but not Victory.Their research is part of the most comprehensive restoration project since the ship was built at Chatham and the findings of the research will be taken into account.
For an excellent photo montage of HMS Victory with photos taken on a very bright sunny day is the album link here by Rob Durant.
Below is the current restoration colour which you can see is quite different to the NCS colour scheme Ochre above, but also very different to the hull colour ochre as in the terracotta ochre images before about 2017:
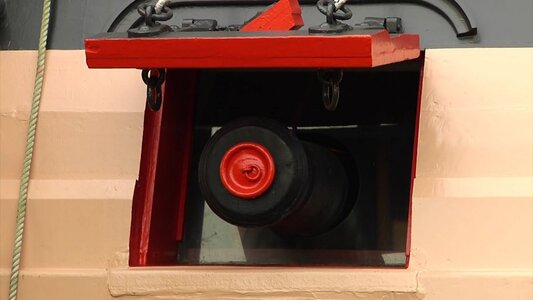
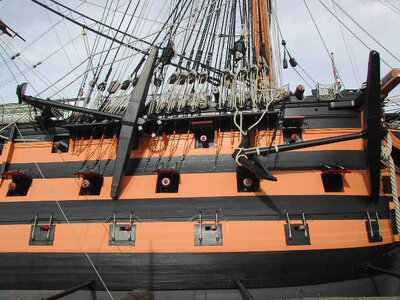
OK, so where does that leave me and my painting? Aesthetically, I am not happy, so I think a lighter, more yellow finish is to be applied. I will post some images as I go.
Best Regards,
PeterG
Last edited: