Hello everyone,
Just like I mentioned in Yesterday's post, I started working on the deck beams. The toughest part was determining the dimensions I would run with. If you look at Mr. McKay's drawings, you will notice that certain beams are constructed with three sections of timber due to the distance from port to starboard. While it seemed simple enough, I noticed that the middle section of the beam varied in length from beam to beam. Being retired from the military, I have not lost the sense of uniformity and decided that I would cut all the middle sections of the beams the same length. Having this concept in mind I drove in and started cutting timber.
After cutting all the timber for the orlop and lower deck beams, I came to the realization that I needed a jig in order to cut the scarfs in a uniform matter. After pondering how I would go about it, I made the jig ensuring that all the cuts would have the same angle and having the same distance. Once that was complete, I tried the cuts for the first beam and was happy with the results.
Now that I had the angle jig situated, I also realized that I would need another jig in order to glue the pieces together. What I did was cut some paneling material and pine boards and set it up in such a way that the outer extremities would butt up against a stop so that each of the sections would have a 1 inch gap (25 mm) between them and then it would be a matter of gluing the middle section to them. Once glued, I placed another pine board against it and clamp it in place applying pressure to the full beam. After a few minutes I would remove it, place it to the side and continue with the next beam.
Once I had all the beams for the orlop deck completed, it was a matter of finally adding the chamfer. This was fairly easy due to just taking the time and making a master pattern that will be used for all of the deck beams. After making the master pattern, I transferred the lines to the raw deck beam and used my table belt sander. While it does raise a lot of dust, it is a lot safer then trying to use the band saw and risking going to far to the line and ruining the beam.
Below are a few photos depicting what I have explained. In the event there are any questions please ask away.
Raymond
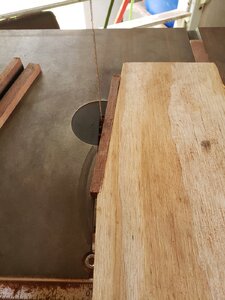
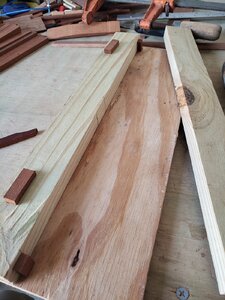
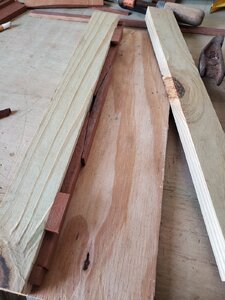

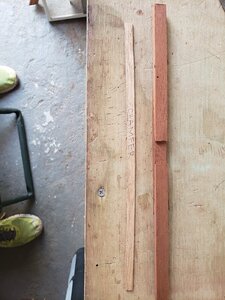
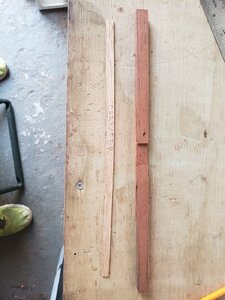
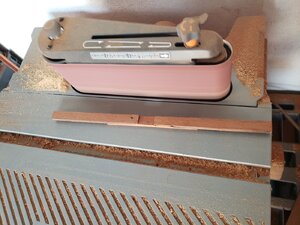
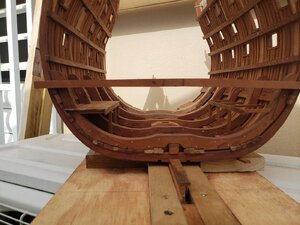
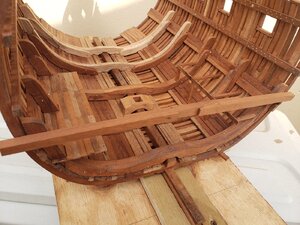