- Joined
- Oct 9, 2020
- Messages
- 1,893
- Points
- 488
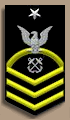
wow. looks great!
Paul, There’s beauty in such symmetry, even if you stopped now it would still be an achievement to have made this, but I know that you’ll just take it to new heights. I’m glad that I’m making Blandford and not this.I had it in my head that I had been posting progress reports, but it turns out I haven't. Herewith is the work I have been doing on the inside of the hull...
After completing the limber strakes and limber boards at the floor of the hull, I spent a day or so trying to figure out how to get the lower deck clamp in the right place (the deck clamp determines the height of the deck beams, so it is important to get it properly located).
I carefully measured the ship plans and cross-referenced several exceptional build logs of other swan class ships. I used a vertical height gauge to transfer my measurements onto the inside of the hull.
View attachment 396426
View attachment 396427
View attachment 396428
The deck clamps are large, heavy timbers on the Kingfisher so I needed to spile the planks in order to get them to run smooth and flat...
View attachment 396429
These specialty clamps are essential for this type of work...
View attachment 396430
Those familiar with swan class ships now know I have chosen to not create the deck clamps with the standard 'top and butt' pattern. I just didn't think I could pull it off on my first POF build (though that pattern will be called for again on the exterior of the ship and perhaps I will give it a shot there - working on the outside of the hull versus the inside should create a more favorable learning environment).
The lower deck clamp is actually two strakes:
View attachment 396431
View attachment 396432
And here is the overall look with the lower deck clamp in place:
View attachment 396433
View attachment 396434
View attachment 396435
Next, I was ready to install the 'thickstuff' associated with the head of the first futtock. Unlike the deck clamp planks which have only a mild taper - the thickstuff planks have a rather substantial taper (and even a drop-plank):
View attachment 396436
View attachment 396437
View attachment 396440
View attachment 396441
In the above images you can see that I have also begun installing footwalling (normal thickness planks) between the limber strakes and the thickstuff:
View attachment 396438
View attachment 396439
I'm not sure I'm a fan of the whiter planking (American holly). On the one hand it provides some visual interest and a nice contrast with other elements of the open frame - but it is rather jolting to look at in isolation. I won't pull it out - but it might be toned down a bit with stain. Stay tuned...
Thank you, Captain Jack!wow. looks great!
A nice comment Roger. But can we ever master something like this? Plus, I know where all the flaws areStunning work Paul. You are becoming a real master of your craft.
I am happy to share this hobby with you Stephan! I think both you and I truly enjoy the creative side...Your updates Paul, are always a warm welcome in the morning. Love your accurate work.
Thanks Ken. A while back (when I had both kits) I asked several people with experience which of the POF ships I should attempt. Universally they recommended the Blandford because of the precision of the laser cutting and the design features incorporated by the manufacturer. In other words, people who know what they are doing fully agree with you!Paul, There’s beauty in such symmetry, even if you stopped now it would still be an achievement to have made this, but I know that you’ll just take it to new heights. I’m glad that I’m making Blandford and not this.
You are far too generous in your assessment, Uwe (though I am grateful). There is a Kingfisher on another forum that makes what I am doing here look like a child playing with blocksExcellent Work - step by step you model will get one of the best POFs .....
magnificent work, it's looks so beautifulI had it in my head that I had been posting progress reports, but it turns out I haven't. Herewith is the work I have been doing on the inside of the hull...
After completing the limber strakes and limber boards at the floor of the hull, I spent a day or so trying to figure out how to get the lower deck clamp in the right place (the deck clamp determines the height of the deck beams, so it is important to get it properly located).
I carefully measured the ship plans and cross-referenced several exceptional build logs of other swan class ships. I used a vertical height gauge to transfer my measurements onto the inside of the hull.
View attachment 396426
View attachment 396427
View attachment 396428
The deck clamps are large, heavy timbers on the Kingfisher so I needed to spile the planks in order to get them to run smooth and flat...
View attachment 396429
These specialty clamps are essential for this type of work...
View attachment 396430
Those familiar with swan class ships now know I have chosen to not create the deck clamps with the standard 'top and butt' pattern. I just didn't think I could pull it off on my first POF build (though that pattern will be called for again on the exterior of the ship and perhaps I will give it a shot there - working on the outside of the hull versus the inside should create a more favorable learning environment).
The lower deck clamp is actually two strakes:
View attachment 396431
View attachment 396432
And here is the overall look with the lower deck clamp in place:
View attachment 396433
View attachment 396434
View attachment 396435
Next, I was ready to install the 'thickstuff' associated with the head of the first futtock. Unlike the deck clamp planks which have only a mild taper - the thickstuff planks have a rather substantial taper (and even a drop-plank):
View attachment 396436
View attachment 396437
View attachment 396440
View attachment 396441
In the above images you can see that I have also begun installing footwalling (normal thickness planks) between the limber strakes and the thickstuff:
View attachment 396438
View attachment 396439
I'm not sure I'm a fan of the whiter planking (American holly). On the one hand it provides some visual interest and a nice contrast with other elements of the open frame - but it is rather jolting to look at in isolation. I won't pull it out - but it might be toned down a bit with stain. Stay tuned...
Thank you, Shota. Your post is very encouraging!magnificent work, it's looks so beautiful
Your inside standings have now paid off, Paul. This inside woodwork looks GREAT. And your picture do also! I think you can now agree that working on a PoF is the best thing in the field of model construction. And adding some scratch parts are the ’surplus’.I had it in my head that I had been posting progress reports, but it turns out I haven't. Herewith is the work I have been doing on the inside of the hull...
After completing the limber strakes and limber boards at the floor of the hull, I spent a day or so trying to figure out how to get the lower deck clamp in the right place (the deck clamp determines the height of the deck beams, so it is important to get it properly located).
I carefully measured the ship plans and cross-referenced several exceptional build logs of other swan class ships. I used a vertical height gauge to transfer my measurements onto the inside of the hull.
View attachment 396426
View attachment 396427
View attachment 396428
The deck clamps are large, heavy timbers on the Kingfisher so I needed to spile the planks in order to get them to run smooth and flat...
View attachment 396429
These specialty clamps are essential for this type of work...
View attachment 396430
Those familiar with swan class ships now know I have chosen to not create the deck clamps with the standard 'top and butt' pattern. I just didn't think I could pull it off on my first POF build (though that pattern will be called for again on the exterior of the ship and perhaps I will give it a shot there - working on the outside of the hull versus the inside should create a more favorable learning environment).
The lower deck clamp is actually two strakes:
View attachment 396431
View attachment 396432
And here is the overall look with the lower deck clamp in place:
View attachment 396433
View attachment 396434
View attachment 396435
Next, I was ready to install the 'thickstuff' associated with the head of the first futtock. Unlike the deck clamp planks which have only a mild taper - the thickstuff planks have a rather substantial taper (and even a drop-plank):
View attachment 396436
View attachment 396437
View attachment 396440
View attachment 396441
In the above images you can see that I have also begun installing footwalling (normal thickness planks) between the limber strakes and the thickstuff:
View attachment 396438
View attachment 396439
I'm not sure I'm a fan of the whiter planking (American holly). On the one hand it provides some visual interest and a nice contrast with other elements of the open frame - but it is rather jolting to look at in isolation. I won't pull it out - but it might be toned down a bit with stain. Stay tuned...
Thanks Charlie!Fantastic!
Thank you kindly, Ken. Yes, I am being stretched. And notwithstanding your generous assessment I sometimes have the urge to start over because I suspect the second time will be easier and better.Paul, A+ stuff. Love the symmetry of all the elements together. Also, your stretching your skill, incorporating elements not in the kit. Great way to prepare for the next challenge. I try to do the same, although unlike mine, your results don't indicate any of this work is your first go at it. KUDOS!
Oh, and I find the somewhat subdued lighting in your photos appealing to my eye.
Sorry if I missed the post but, are your clamps homemade or purchased. If the latter, would you please post a link or post# if already provided. I'm helpless, as you know.![]()
Thanks Peter. A POF model really is the top-of-the-mark if someone wants to show how a hull was constructed...Your inside standings have now paid off, Paul. This inside woodwork looks GREAT. And your picture do also! I think you can now agree that working on a PoF is the best thing in the field of model construction. And adding some scratch parts are the ’surplus’.
Regards, Peter
Much appreciated my friend! Ah...problem management is exhausting work! Sometimes I wish there was a master builder visiting my workshop weekly to get me going in the right direction and see problems faster than I recognize them.Hello Paul, you are hardly on holiday for 3 weeks and you already have to catch up on 10 pages. As I read, there were one or two problems that you managed very well. Your inside looks fantastic as does the rest of it. I am really thrilled with the absolutely accurate work. Ps: I personally really like the light holly, a great contrast that sets it off well.