- Joined
- Sep 28, 2020
- Messages
- 285
- Points
- 168
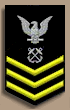
Like a Nudelwalker 

![]() |
As a way to introduce our brass coins to the community, we will raffle off a free coin during the month of August. Follow link ABOVE for instructions for entering. |
![]() |
How much time the modeler loses on the cleaning of remainders after the laser char?The next working step on the Le Coureur is the final cleaning of the frames from rest of laser char.
For this work I am using a sharp chisel
This is depending off course how much a modeler wants to clean.Ahoy!
How much time the modeler loses on the cleaning of remainders after the laser char?
Frankly speaking, I have been wondering about this tooAhoy!
How much time the modeler loses on the cleaning of remainders after the laser char?
Another thought (dream) I had in this connection: That way it should also be possible for the kit manufactures to make some really nice POF kits in scale 1:36 and 1:24
Small tip for the planking works
-> I call it "Dry Bending"
If you do not want to water or steam the planks for bending, these planks can also be bend (for 90% of the cases on this ship model dry.
I show in principle this way I did on most of my planks for the Le Coureur.
Here you see a plank streight and only sanded on top of a hobby / cutting mat - The black rod next to the plank is a small metalic chisel
View attachment 212514
Now take the rod with two hands (for the photo I needed the right one for making the photo) and run up and down (green arros) above the plank with relatively high pressure (red arrows)
View attachment 212519
after some run you will realize, that the plank is starting to bend
View attachment 212516
View attachment 212517
The reduction of the thickness is minimal - the bending is suitable for most areas of this model
View attachment 212518
OK, some more of my two cents on this subject.Frankly speaking, I have been wondering about this tooLe Coureur is my first and only kit and till now have only build a small part of it but for some of the parts I feel quite certain that I could have made a new part from scratch in less time than I used to remove the char. My conclusion (based on extremely little experience): For some parts I would have preferred if the kit manufacture had supplied a blank plate / lists of wood in the right thickness and a technical drawing of the individual part. It is not only the time to remove the char but in some cases also time to make simulated joints between virtual planks etc. Even more important: then we could also avoid parts where the grain is running across a plank perpendicular to the length.
Another thought (dream) I had in this connection: That way it should also be possible for the kit manufactures to make some really nice POF kits in scale 1:36 and 1:24