- Joined
- Oct 15, 2017
- Messages
- 1,177
- Points
- 443
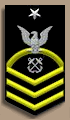
Dear Heinrich, Tobias, Stephan, First thank you all for your input. I have followed each of your builds and truly respect you talents and abilities, maybe more than you know.
I surely can tell from your posts, all of you have given thought to how you present them, in the most respectful way, with the sole intention of providing me with assistance.
The same help that I've learned to respect from the SoS community. THANK YOU>
With that said, I expected this response and it's perfectly OK. This is why I've used the reference to Hans Cristian Anderson's story "The Ugly Duckling". It is ugly now, but trust me, a beautiful bird will be born from it.
@Heinrich, I do understand your point of practicing planking skills. I believe we are all striving to improve our skills in every aspect of ship modeling, especially planking, which, depending on the hull structure can be very difficult. I have confidence in my planking skills. I trust you will see later. Tapering, spilling planks at this stage would provide a good opportunity to practice those skill indeed. In this case I have weighed the ROI (return on investment) in time vs. return on that time and it just doesn't make sense. Keep in mind, I am not going into this blindly. If you knew how much I've obsessed over it before I made my decision, I think you would understand. But let me thank you again. If you didn't already know, I am already a student of yours through your WB build!
@Tobias, thanks for your input. The only difference I see in using hammered nails vs. staples is it would take more time to hammer. Staples are much faster and achieve even a better purchase of planks to the skeleton. Actually, each staple, having 2 prongs is the equivalent of using 2 small nails. In addition to that I will be using approximately 2,000 staples per layer, the equivalent of 4,000 nails per layer. The only function of the staples is to ensure the planks stay firmly attached, until the PVA dries. Now, on the down side of my approach, it will take me longer to extract that many staples. So this is an unknown.
@stephan, Please, there is NO need to apologize. I would never question your intent. I just happen to be a little sensitive in this area as it is something I've dealt with for 66 years. Some people are not nice. You are NOT one of them. And, of course Stephan I do know your true intent and that is to help. Thank you Sir.
When I was young my Dad would take every relevant opportunity to remind me, "If you fail to plan, you plan to fail." I don't think he understood the level to which I would embrace this dictum. It allowed me to organize the complicated, manage risk and provide me with a skill that help me through a rewarding career. While I spend a lot of time planning, no plan is ever perfect. In reality, there has never been a project plan, in my career, I've worked on, mine or others that didn't change. I have come to learn, once that plan has been finalized and it has addressed the "critically important" issues, then you've also addressed the "critically important" risks and the work must begin.
Thank you all again for your input and advice. I am not ignoring you. I hear you. I am confident in my approach in that my method meets the objective. I hope you respect my decision as I respect your knowledge and advice.
Now, I must get back to work. That will not be able to sleep tonight until I get that bolster issue resolved.

Till next time...
Cheers.
I surely can tell from your posts, all of you have given thought to how you present them, in the most respectful way, with the sole intention of providing me with assistance.

With that said, I expected this response and it's perfectly OK. This is why I've used the reference to Hans Cristian Anderson's story "The Ugly Duckling". It is ugly now, but trust me, a beautiful bird will be born from it.
@Heinrich, I do understand your point of practicing planking skills. I believe we are all striving to improve our skills in every aspect of ship modeling, especially planking, which, depending on the hull structure can be very difficult. I have confidence in my planking skills. I trust you will see later. Tapering, spilling planks at this stage would provide a good opportunity to practice those skill indeed. In this case I have weighed the ROI (return on investment) in time vs. return on that time and it just doesn't make sense. Keep in mind, I am not going into this blindly. If you knew how much I've obsessed over it before I made my decision, I think you would understand. But let me thank you again. If you didn't already know, I am already a student of yours through your WB build!

@Tobias, thanks for your input. The only difference I see in using hammered nails vs. staples is it would take more time to hammer. Staples are much faster and achieve even a better purchase of planks to the skeleton. Actually, each staple, having 2 prongs is the equivalent of using 2 small nails. In addition to that I will be using approximately 2,000 staples per layer, the equivalent of 4,000 nails per layer. The only function of the staples is to ensure the planks stay firmly attached, until the PVA dries. Now, on the down side of my approach, it will take me longer to extract that many staples. So this is an unknown.
@stephan, Please, there is NO need to apologize. I would never question your intent. I just happen to be a little sensitive in this area as it is something I've dealt with for 66 years. Some people are not nice. You are NOT one of them. And, of course Stephan I do know your true intent and that is to help. Thank you Sir.

When I was young my Dad would take every relevant opportunity to remind me, "If you fail to plan, you plan to fail." I don't think he understood the level to which I would embrace this dictum. It allowed me to organize the complicated, manage risk and provide me with a skill that help me through a rewarding career. While I spend a lot of time planning, no plan is ever perfect. In reality, there has never been a project plan, in my career, I've worked on, mine or others that didn't change. I have come to learn, once that plan has been finalized and it has addressed the "critically important" issues, then you've also addressed the "critically important" risks and the work must begin.
Thank you all again for your input and advice. I am not ignoring you. I hear you. I am confident in my approach in that my method meets the objective. I hope you respect my decision as I respect your knowledge and advice.

Now, I must get back to work. That will not be able to sleep tonight until I get that bolster issue resolved.


Till next time...
Cheers.