As promised, a small update after having returned from our holiday trip. A bit earlier as planned, because very warm weather melted the snow from our skiing tracks almost completely.
As I told earlier the hull was sent to a professional glassfibre shop for making a mold of it, and laminate three final hulls for all of us. The idea was that rows of rivets would be copied into the mold and could be seen on the surfaces of final hulls. That succeeded completely, and it was nice to receive nicely made hulls from the shop for further building.
First longitudinal flanges for deck and half hull were made of MDF to be able to separate the mold halves from each another:
First half of mold laminated:
Both halves laminated and bolted together:
Mold completed and separated from the original hull. Some aluminum plates didn`t resist the chemicals used and came off the original hull. This had however no effect on the surface of the mold:
In the mean time building of steam engine continued. This time machining of the cylinder block was made. First the upper and lower surfaces were smoothed:
All holes were carefully marked and those for upright columns were drilled:
Cylinder block attached to the columns with M3 nuts:
Cylinders were first bored in the milling machine:
And finalized & smoothed in the lathe:
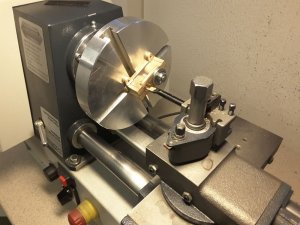