I have dropped lucky in the Epoxy had gone rock hard after a few hours.Thought it would take longer as it is cold in the workshop.
I removed the assembly and brought it into the house(wife has gone to bed
) On the front face I cut a trough on two sides around each Cathead using a burr,this will be covered by the planking later.
The yellow stuff is mouldmakers wax.I have used this to form a dam at the edges of the bulkhead for the next step.Using a Pipette I added Epoxy finishing resin into each trough.This has a 3hour cure time and is thin enough to flow around the Cathead forming a solid bond between the Catheads and bulkhead.
I adopted this approach because traditional glue would never have remained in the joints whilst I manipulated the three items into position in the bow.Due to capillary reaction the resin has seeped around all the tiny gaps between the parts.
Kind Regards
Nigel
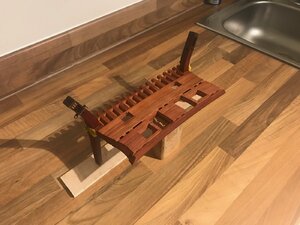
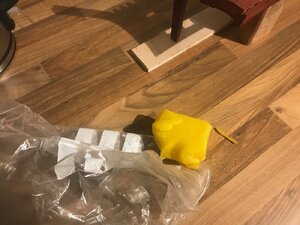
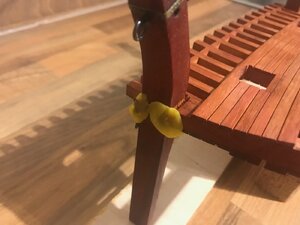
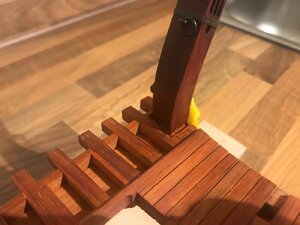
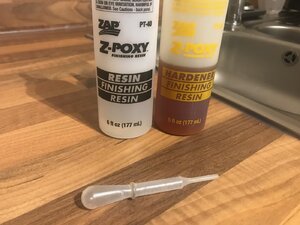
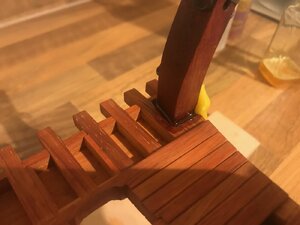
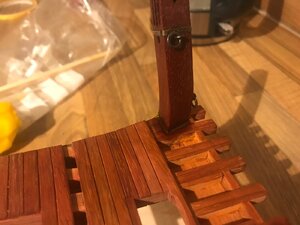
I removed the assembly and brought it into the house(wife has gone to bed

The yellow stuff is mouldmakers wax.I have used this to form a dam at the edges of the bulkhead for the next step.Using a Pipette I added Epoxy finishing resin into each trough.This has a 3hour cure time and is thin enough to flow around the Cathead forming a solid bond between the Catheads and bulkhead.
I adopted this approach because traditional glue would never have remained in the joints whilst I manipulated the three items into position in the bow.Due to capillary reaction the resin has seeped around all the tiny gaps between the parts.
Kind Regards
Nigel
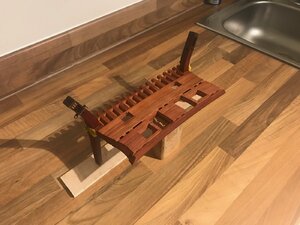
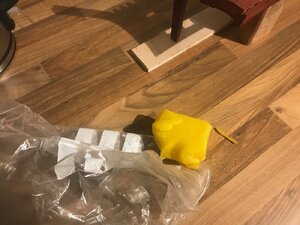
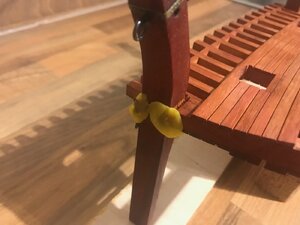
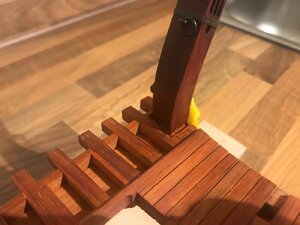
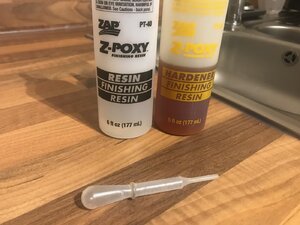
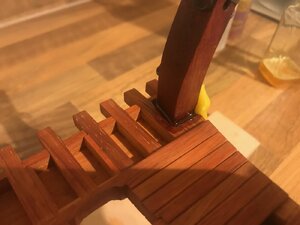
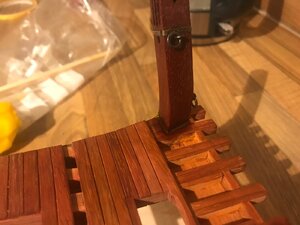