This next level of the amortisement is fun to make because, while it seems simple, it is actually a pretty complex form. Without having drawn a top plan view, I have to wing-it, a little, when it comes to establishing depth and taper.
The first step was to make up a styrene billet. The canopy is 1/4” in height, between the top and bottom mouldings. I made my billet stock a little wider, in order to file in the top and bottom taper necessitated by the tumblehome of the ship’s sides (see pic below).
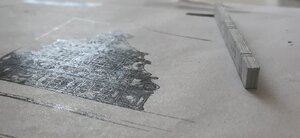
Once I had billet stock, I could lay out all of the paneling and the outer parameters of the canopy:
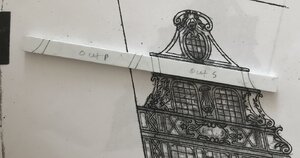
The tricky thing about this aspect of the project is that there does need to be some depth to the canopy - which will be further overhung by the top and bottom mouldings - because the upper-most section of the amortisement has at least some depth, at its center, which tapers out to the sides (where they abut the pixies). Considering that, the canopy must also diminish, slightly, in depth, from top to bottom. And, on top of all of that - there are a series of reverse curves that define the bombastic form of the canopy.
In layout, and looking at it from the top view, that all looks like this (excepting for the reverse curves, at the ends, which I did not draw-in):
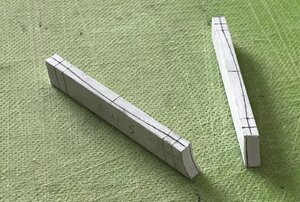
With the layout pencilled-in, top and bottom, and on the outer face, I could then make a series of shoulder cuts, with a fine back saw. After hogging out the bulk of waste, at the ends, this is what that looks like:
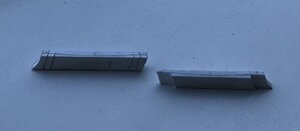
Once all of the shoulders were neatlydefined, I could set-to shaping the subtly curves ends and middle:
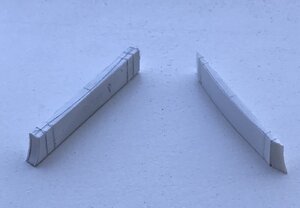
The end scallops are set-down about 1/32” lower than their adjacent short flats, so that when I apply the panel framing details, in the next step, there will remain a stepped demarcation between the ends and middle section.
As I had hoped, the second Xs moulding came out much more cleanly than the first. These decorations are springy enough to accommodate the tapering surface, without appearing to become distorted. Once, I have the port-side canopy made and both canopies paneled, I can use them to pattern the exact top and bottom overhang of the mouldings.
More to follow...