Of all the carved work that I have done for this project so far, the trailboard has been the most vexing, by a long-shot.
While I usually double-stick the work to a scrap of masonite, I reasoned that I would need to work this carving, constantly, from one side to the other. The necessity of this approach, as I quickly discovered, is underscored by the fact that - despite a sound indexing point, in the half-round forward notch - the paper patterns were just askew of each other, from one side to the other.
I wonder whether this can be attributed to the paper expanding unevenly, upon application of the water-based glue stick. I don’t use solvent-based spray adhesives because of the plastic.
Whatever the case may be, working both sides enables you to meet at the middle and smooth a transition between the two sides. It’s all just extremely time consuming, but then, I’m a glutton...
While it seemed like a good idea to work from the outside, in - my mistake was in relieving the Xs, first. I should have saved this for last because doing so made the work especially fragile. The design calls for shell reliefs inside these X’s, but I just did not think I could pull that off in this scale. Instead, I opted for the lightness and visual interest that opening up the negative space provides. These pictures don’t reflect the current, near finished state of the carving, but they do provide a sense of scale:
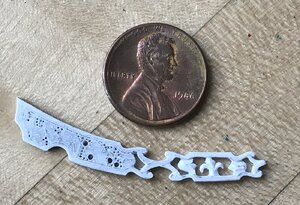
Presently, I’m carving the year marker, and will soon clear up any fuzzy bits, re-join the broken bit and paint before installation. I am happy with the way that it came out, but it was a real devil of a job to get there.
The other project that has consumed an in-ordinate amount of time was fairing back the knee extensions of the head.
This has been a process of adding back plastic and slowly fairing to the new contour of the bow, until I had a solid joint at the cut-off point, all along the top edge of the knee extension and connection at the side.
What makes all of this difficult, of course, is that the bow extensions that I installed, earlier, flatten the bow a bit, near the stem. But, then, I also filled the space between the lower two wales, as an extension of the anchor lining. And, for good measure, I padded-out the leading edge of the stem by a 1/16”; that is all a lot of new reality to fair to. As such, I decided not to worry about connection along the bottom edge, as long as I had a solid glue joint at the joint, top and sides:
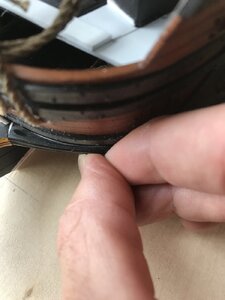
In these two pics, you can see how the first round of shims didn’t quite get me where I needed to be.
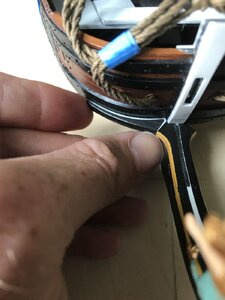
After more shimming, I finally got the port side secured:
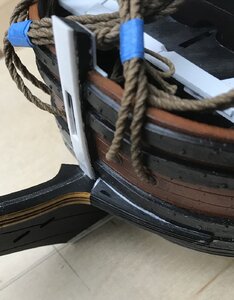
But, the starboard side was a real PITA; I’d shim, file away too much in the wrong spot, then re-shim, etc. Eventually, I got it right:
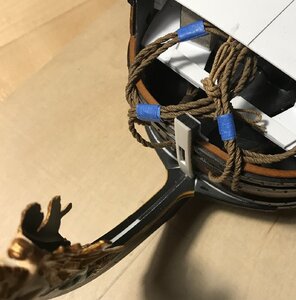
Though, I still have some putty work to do, before painting these extensions, you can see that they align neatly with the wales and present a fair transition:
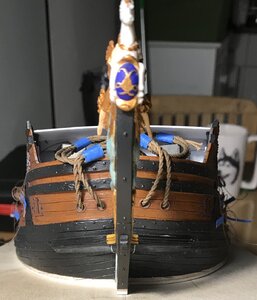
With that at an acceptable state, I set to work making a few slight modifications to the upper knee.
I filed more of a hook for the collar of the main stay, and added a half round moulding to the profile just above:
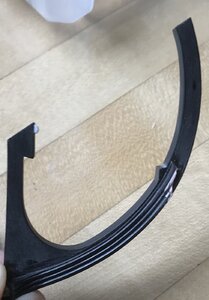
You can see the bit of BONDO patch to the forward end of the fluted moulding. That was because of this gap between the tail of the figurehead and the moulding:

All of the parts of the head are warped just enough that problems like this are un-avoidable, despite best efforts to fair and straighten things out as I glued the figurehead to the cutwater assembly. This gap does not exist on the port side. Leaving the gap, though, spoils the illusion that this is more than just a plastic model.
Re-shaping the patch didn’t take long, and it was time well spent:
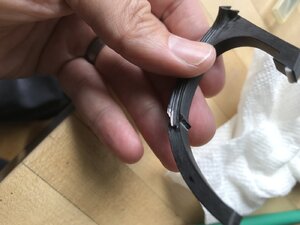
Unfortunately, I made a dog’s breakfast of my first attempt to paint the upper knee. The black went on gloppy, and I had to scrape the whole thing clean and re-do it. I’ve also painted in the yellow ocher and now this part is ready for installation, following the trailboard piece.
SOS BONUS SHOT
I’m home now, and cleaned up the trailboard so that I could glue it back together. I set it in place, temporarily until the glue dries:
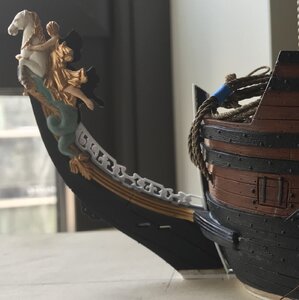
As a side note, I have found the Tamiya acrylics to be very difficult paints for brushing; they practically dry on the brush before you can apply them, and it takes multiple applications for the necessary depth of color. Does anyone know of any additives or conditioners that make them more user-friendly for brushing?
Next, I will tackle the short beakhead deck and the beakhead bulkhead. I have figured out ways to re-cycle the stock kit parts, which saves me from the sort of frame and plank job I did on the lower transom.
Many thanks for the birthday wishes, and as ever - thank you for your interest, your likes and your comments.
Be well!