Almost a week without a blog but very eventful.(as you can see by end of saga)
Reread opening chapters of B.Frohlich’s “Art of ship modelling” with a bit more understanding.
He mentions the change of weather opening gap of 5mm over 100cm model because of change in weather.
Well, we had the first rain after 6 months.Its a humid area anyway (coastal) but this cannot explain the accumulated error after fitting the first 6 cants. I hadn’t forgotten the foot bevel. I think the main culprit was an overly tight hawse filling piece.I also think I should have made a couple of the cants better.
Unstuck cant and filler pieces ans while waiting to dry,gave thought to alternative ways of aligning and holding the cant pieces while glue dries.
I’ve used building jigs but here, the alignment is by the timberline which is sloping.So I took heights from plans for the sides, cut both floor and “roof” together so as to set on board plans, and will be able to turn over and use for other side. Held in place by weight,removable for visualization and access.
Shaved down filler piece, remade some cants and cleaned up others and started to place them. Seems better and jig works
A friend sourced a supply of PEAR trees that a fruit farmer was selling as kindling!!
So with a patient and long-suffering wife for company, drove to the north of the country -couple of hours each way.
The trees had been cut to logs and branches last year, to lengths suitable for wood stoves i.e. about 40cms. The thicker logs were mainly split from drying out.
Selected half a boot load (it was free) and drove home.(Had said to wife maybe see some local sites or have a meal out, but still semi lockdown precluded this).
Drove home and while my wife was making supper, thought I’d see if and how much of the wood was usable.
Prepared a couple of pieces with my 10in table saw and with last pass, lost concentration for a second and felt a bag to my thumb. HIT by the saw teeth. A bloody mess, that I couldn’t treat by myself with superglue. Off to local casualty(emergency room) some stitches where possible and bandaging.Declined overnight stay.
Will be ok but feeling terribly stupid. Every instruction, Utube etc emphasises safety. I did for most part use sticks, But familiarity and tiredness caused that stupid lapse.
I said, in my first blog, that you could learn from my mistakes- this accident is the most important of lessons.
PLEASE BE SAFE
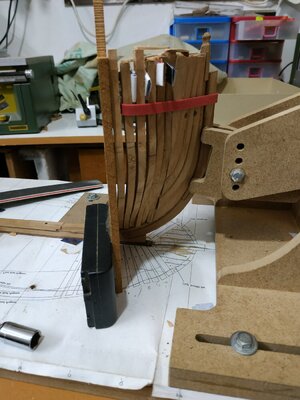
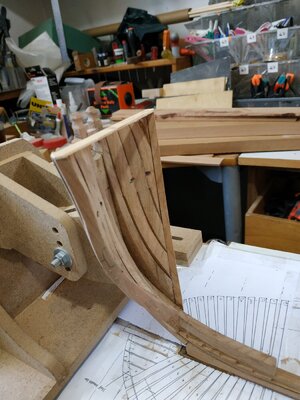
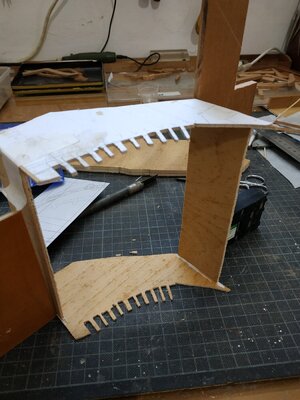
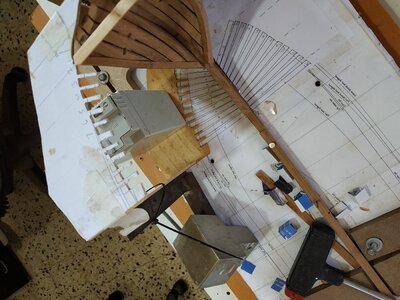

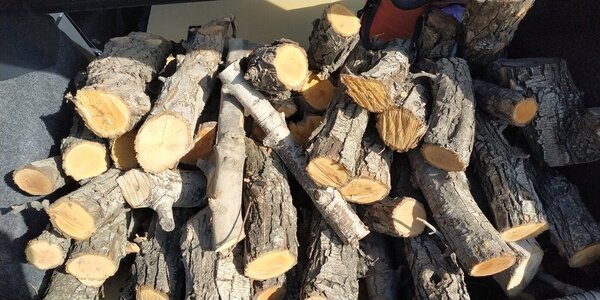
Reread opening chapters of B.Frohlich’s “Art of ship modelling” with a bit more understanding.
He mentions the change of weather opening gap of 5mm over 100cm model because of change in weather.
Well, we had the first rain after 6 months.Its a humid area anyway (coastal) but this cannot explain the accumulated error after fitting the first 6 cants. I hadn’t forgotten the foot bevel. I think the main culprit was an overly tight hawse filling piece.I also think I should have made a couple of the cants better.
Unstuck cant and filler pieces ans while waiting to dry,gave thought to alternative ways of aligning and holding the cant pieces while glue dries.
I’ve used building jigs but here, the alignment is by the timberline which is sloping.So I took heights from plans for the sides, cut both floor and “roof” together so as to set on board plans, and will be able to turn over and use for other side. Held in place by weight,removable for visualization and access.
Shaved down filler piece, remade some cants and cleaned up others and started to place them. Seems better and jig works
A friend sourced a supply of PEAR trees that a fruit farmer was selling as kindling!!
So with a patient and long-suffering wife for company, drove to the north of the country -couple of hours each way.
The trees had been cut to logs and branches last year, to lengths suitable for wood stoves i.e. about 40cms. The thicker logs were mainly split from drying out.
Selected half a boot load (it was free) and drove home.(Had said to wife maybe see some local sites or have a meal out, but still semi lockdown precluded this).
Drove home and while my wife was making supper, thought I’d see if and how much of the wood was usable.
Prepared a couple of pieces with my 10in table saw and with last pass, lost concentration for a second and felt a bag to my thumb. HIT by the saw teeth. A bloody mess, that I couldn’t treat by myself with superglue. Off to local casualty(emergency room) some stitches where possible and bandaging.Declined overnight stay.
Will be ok but feeling terribly stupid. Every instruction, Utube etc emphasises safety. I did for most part use sticks, But familiarity and tiredness caused that stupid lapse.
I said, in my first blog, that you could learn from my mistakes- this accident is the most important of lessons.
PLEASE BE SAFE
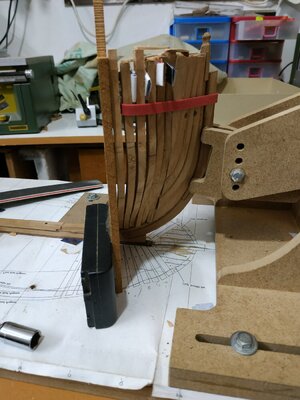
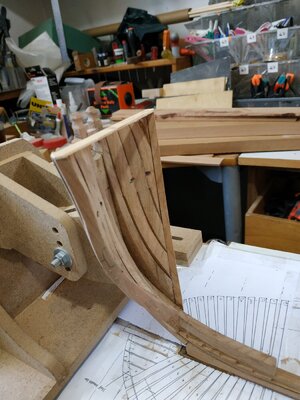
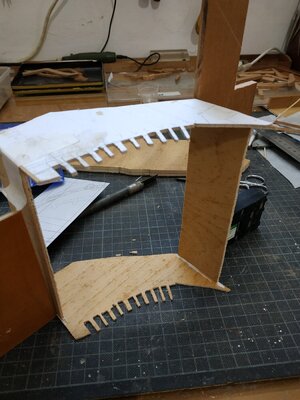
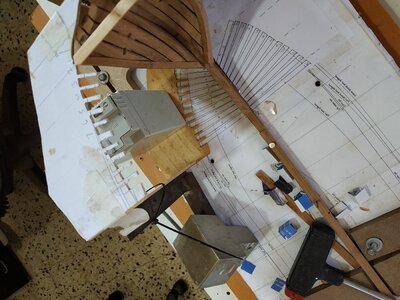

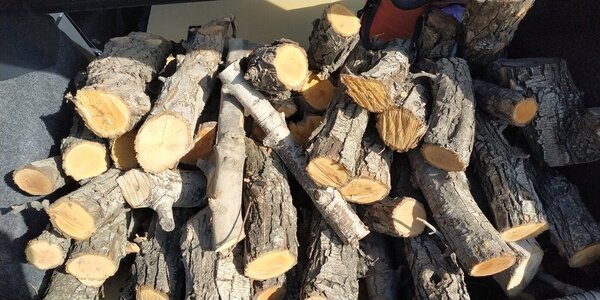
Last edited by a moderator: