Framing the stem/side Counters
(TFFM mentions a 9th port- at present this would be an unnecessary complication and I’m still on chapter 2.)
The practicum gives a detailed explanation which encourages reading to the end. I don’t really understand, so I turn to Kevin’s video-he says something similar, so we go ahead and make the pieces.
Before attempting to make the piece, a jig of some sort needs to be made to align and support the aft end, at the correct height, and angle so the pieces are separated by the correct distance. Additionally, the stem needs support to maintain the vertical 90deg position.
The hobby building slip has a vertical plan holder. By adding the stem clamp to this (with the body plan underneath)it supports the stem, the new side counter while controlling its position and angle.
Instructed to draw line parallel and 3.34cm aft of AP line on the breadth plan. This intersects with the end of the timberline and is aft position of the pieces and the mark for the vertical plan holder.
On the body plan, vertical lines, 3.9 cm either side of the midline are drawn and the point this intersects with the height of timberline, is marked.(A simple drawing on the page makes this very simple).
Fortunately the book gives a (correct 1/48)scale image because I spent a half an hour searching the plans.Note this is for the starboard side - it took me a while to be sure of this.
Photocopies for templates, 7.95mm blanks, and using the sanders, made the pieces in 2 stages ie dimensions.
The timber line is marked on the pieces and the inner aspect aligned to the mark on the plan (again the drawing in TFFM is self explanatory)
The “foot” needs some refining to accommodate angle of #1 cant and slope of wing transom.
This is (if only temporary)a fragile joint so I used 5min epoxy while the plan holder supports the end and vertical plane is maintained.
An additional measure is used- 9.22 cm between the 2 upper knuckles-this is checked while glue is still semi-flexible.
Finally, if sure OK, a spall or beam is temporarily stuck to the tops for additional stability.
PS accumulating lots of photocopies of part plans/templates. Filing them in separate plastic envelopes in a file makes for order.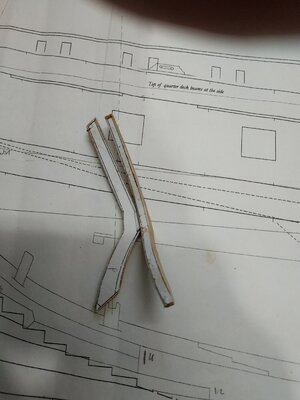
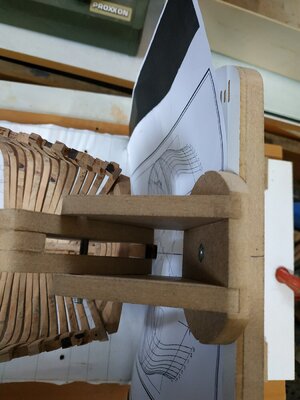
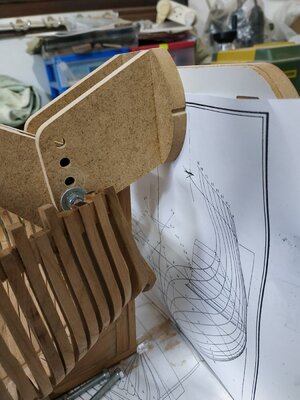
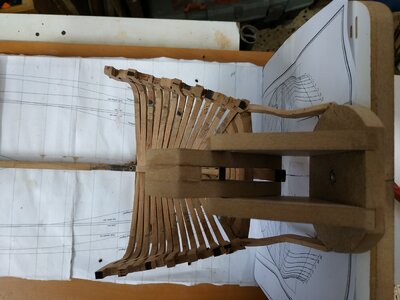
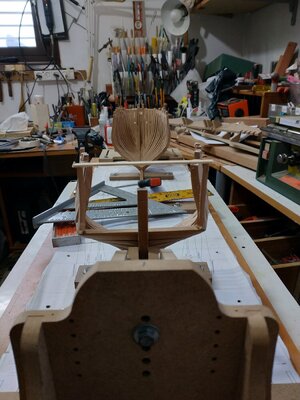
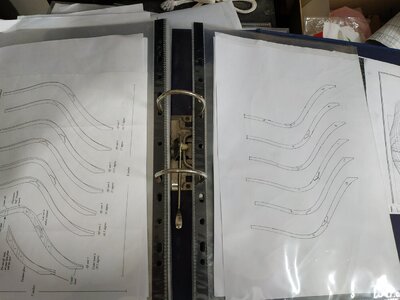
(TFFM mentions a 9th port- at present this would be an unnecessary complication and I’m still on chapter 2.)
The practicum gives a detailed explanation which encourages reading to the end. I don’t really understand, so I turn to Kevin’s video-he says something similar, so we go ahead and make the pieces.
Before attempting to make the piece, a jig of some sort needs to be made to align and support the aft end, at the correct height, and angle so the pieces are separated by the correct distance. Additionally, the stem needs support to maintain the vertical 90deg position.
The hobby building slip has a vertical plan holder. By adding the stem clamp to this (with the body plan underneath)it supports the stem, the new side counter while controlling its position and angle.
Instructed to draw line parallel and 3.34cm aft of AP line on the breadth plan. This intersects with the end of the timberline and is aft position of the pieces and the mark for the vertical plan holder.
On the body plan, vertical lines, 3.9 cm either side of the midline are drawn and the point this intersects with the height of timberline, is marked.(A simple drawing on the page makes this very simple).
Fortunately the book gives a (correct 1/48)scale image because I spent a half an hour searching the plans.Note this is for the starboard side - it took me a while to be sure of this.
Photocopies for templates, 7.95mm blanks, and using the sanders, made the pieces in 2 stages ie dimensions.
The timber line is marked on the pieces and the inner aspect aligned to the mark on the plan (again the drawing in TFFM is self explanatory)
The “foot” needs some refining to accommodate angle of #1 cant and slope of wing transom.
This is (if only temporary)a fragile joint so I used 5min epoxy while the plan holder supports the end and vertical plane is maintained.
An additional measure is used- 9.22 cm between the 2 upper knuckles-this is checked while glue is still semi-flexible.
Finally, if sure OK, a spall or beam is temporarily stuck to the tops for additional stability.
PS accumulating lots of photocopies of part plans/templates. Filing them in separate plastic envelopes in a file makes for order.
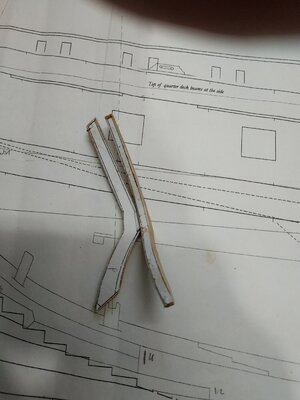
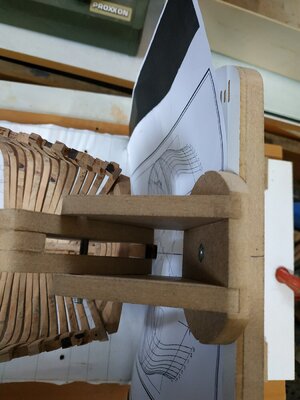
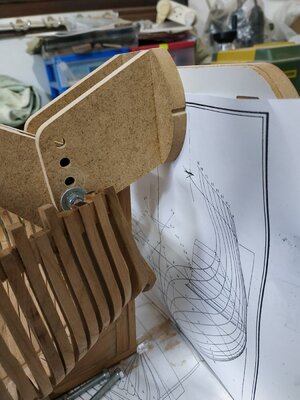
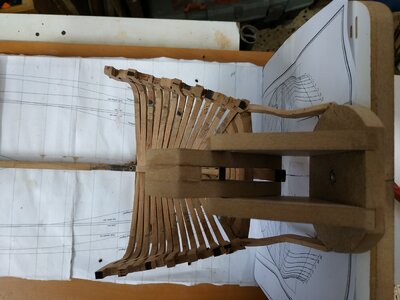
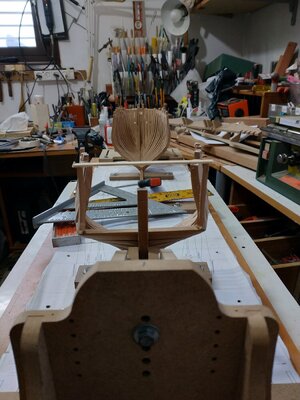
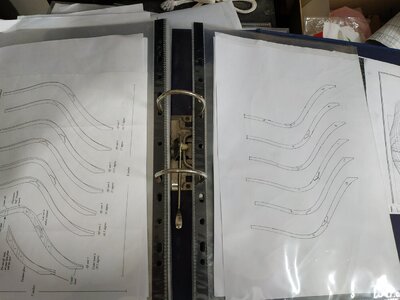