@dockattner ...OK. Before you all laugh at me or shake your heads in dismay recall that this is my first build and anyone with a pinch of common sense would never have started with a ship this large. But I have run up against an issue. I was going to lay out the second layer of hull planking...but when I placed this test strip and kept it flush/flat against the hull it completely ignores the flow of the ship. No way I can edge bend a strip this thin. What am I missing?
View attachment 193537
Cut your boards into smaller lengths, like planking a deck. Stagger your joints as well. Smaller boards will follow curve without bending, however you may have to miter the edges a hair (angle cut to average curve). Pick a board or scribe a line to set the curve you want to follow with the smaller boards. You already have nice vertical lines to determine where board ends will stagger. I did a two to three bulkhead span for average board length. 3 bulkheads in middle of ship with less or no curve, and smaller 2 bulkhead span for length of boards towards bow and stern where there is more of a curve. And you will need to taper boards towards the bow and probably use a stealer or two at the stern. And remember the boards at the keel will be straight for a few rows, then you will end up with tapered boards where they all meet from the bulwarks coming down to the rows at the keel. You want them to meet under the bulkhead where it is not visible from the side, if possible.
Just remember, no sharp corners, if you have to ...come back and radius where two boards meet at an angle with a small file. That way your next row will flow around a smooth and hopefully large radius!
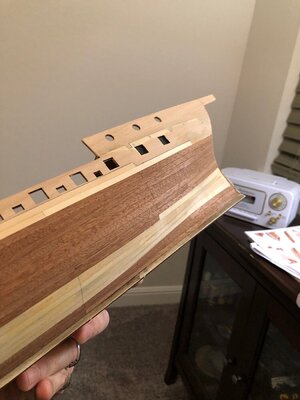
Hope all that makes sense. My ship is smaller and has less curvature.
Think of the boards as rectangular teeth going around in a curve to form your bite....lol

Last edited: