Now, while I thought I had answered Paul's question, it turns out I hadn't - So, Paul got back to me with the following:
PAUL
Hi Peter,
I feel terrible but if I pointed to the main topsail brace, I didn't mean to. I am trying to figure out the run for the mizzen topmast stay - there is one on each side (bilateral).
Where does the green line terminate as it approaches the deck?

Paul
PETER RESPONDS
My apologies Paul - This was not the line I was looking at (however we eventually got there). This line of standing rigging caused me a bit of consternation at the time too!! Below is the museum plan of this line.
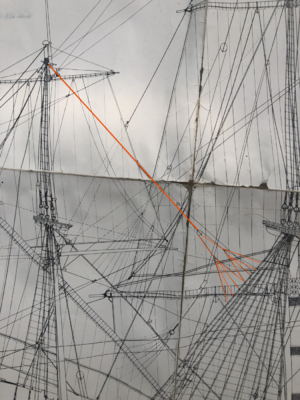
So, from just above the upper top of the mizzen, two stays come forward to two larger single blocks. On both the port and starboard side, the lines running through these blocks, go down to four euphroe blocks (two each side) to the crowsfeet attached to the mainmast aft shroud starting just below the main mast lower futtock stave.
So, that's what the plans say. I had a problem with this as this meant that there was no adjustment for tension to be applied at either end of this rigging. The upper stay pendants at the mast head cannot be tightened, nor can the lower crowsfeet attachment at the shrouds, so I went looking for an alternative. I found it on Page 123 (Fig 135 and Fig 137) of R.C. Anderson. In this description of the Norske Love rig of 1926, he adds a second block below the mizzen stay pendants on both the port and starboard sides. You will also find this arrangement on Clayton's rigging I think.
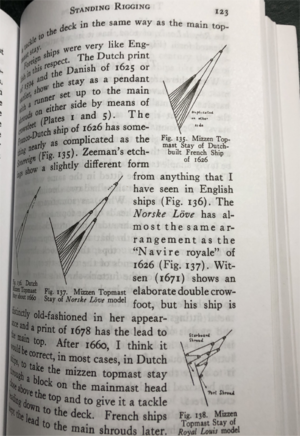
Having the second block, meant that a line could then be transferred to deck to tension these stays and the crowsfeet as part of the standing rigging. Personally I think this may have been an error in the museum's Rigging Plans.
This arrangement (from Anderson) is how I have rigged it on my Vasa (see below):
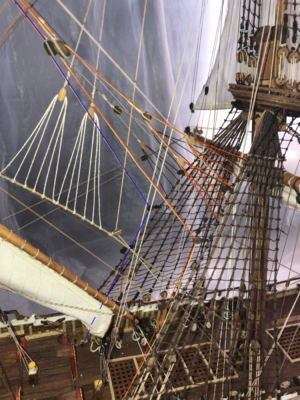
I have shown the starboard lines in red, port in blue. Let us discuss only the port, as you can see the deck belaying point whereas it's hidden on the starboard side, but the starboard side is exactly the same.
From the crows feet blocks, a loop of line goes through a single block which then has a securing line running up through a second single large block supported by the pendant coming down from the mizzen head. The line running through this large block is then led to a single block attached to the aft mainmast shroud just below the lowest crowsfoot line attachment point. From here the line for port, goes to the port side deck belaying point just beside the main deck steps leading down from the gallery deck (note in the photo above, the line goes behind the mizzen sail so I have drawn it with dashed line). This securing point has a block with becket and hook secured to an eyebolt in the deck against the bulwarks. The line after coming out of this block then goes to a cleat mounted on one of the bulwarks. You can see this arrangement in the photo where the line returns from the deck mounted block and up to the cleat with a coil of the excess line tied off around the cleat.
This solution worked well for me and although it was tricky getting the eyebolt and block into the cramped location against the side of the deck, it was out of the way and did the job of allowing tension to be applied to the stays. You of course have to do the same rigging arrangement on both port and starboard sides.
I hope this helps Paul.
Regards,
PeterG.
PAUL
Hi Peter,
I feel terrible but if I pointed to the main topsail brace, I didn't mean to. I am trying to figure out the run for the mizzen topmast stay - there is one on each side (bilateral).
Where does the green line terminate as it approaches the deck?

Paul
PETER RESPONDS
My apologies Paul - This was not the line I was looking at (however we eventually got there). This line of standing rigging caused me a bit of consternation at the time too!! Below is the museum plan of this line.
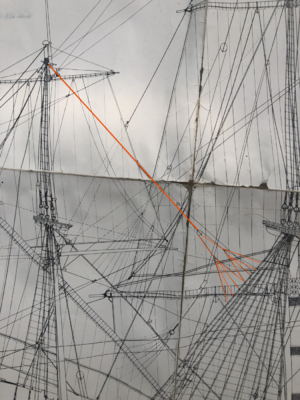
So, from just above the upper top of the mizzen, two stays come forward to two larger single blocks. On both the port and starboard side, the lines running through these blocks, go down to four euphroe blocks (two each side) to the crowsfeet attached to the mainmast aft shroud starting just below the main mast lower futtock stave.
So, that's what the plans say. I had a problem with this as this meant that there was no adjustment for tension to be applied at either end of this rigging. The upper stay pendants at the mast head cannot be tightened, nor can the lower crowsfeet attachment at the shrouds, so I went looking for an alternative. I found it on Page 123 (Fig 135 and Fig 137) of R.C. Anderson. In this description of the Norske Love rig of 1926, he adds a second block below the mizzen stay pendants on both the port and starboard sides. You will also find this arrangement on Clayton's rigging I think.
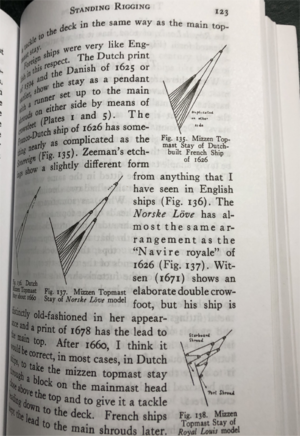
Having the second block, meant that a line could then be transferred to deck to tension these stays and the crowsfeet as part of the standing rigging. Personally I think this may have been an error in the museum's Rigging Plans.
This arrangement (from Anderson) is how I have rigged it on my Vasa (see below):
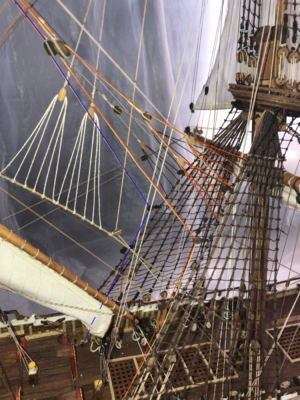
I have shown the starboard lines in red, port in blue. Let us discuss only the port, as you can see the deck belaying point whereas it's hidden on the starboard side, but the starboard side is exactly the same.
From the crows feet blocks, a loop of line goes through a single block which then has a securing line running up through a second single large block supported by the pendant coming down from the mizzen head. The line running through this large block is then led to a single block attached to the aft mainmast shroud just below the lowest crowsfoot line attachment point. From here the line for port, goes to the port side deck belaying point just beside the main deck steps leading down from the gallery deck (note in the photo above, the line goes behind the mizzen sail so I have drawn it with dashed line). This securing point has a block with becket and hook secured to an eyebolt in the deck against the bulwarks. The line after coming out of this block then goes to a cleat mounted on one of the bulwarks. You can see this arrangement in the photo where the line returns from the deck mounted block and up to the cleat with a coil of the excess line tied off around the cleat.
This solution worked well for me and although it was tricky getting the eyebolt and block into the cramped location against the side of the deck, it was out of the way and did the job of allowing tension to be applied to the stays. You of course have to do the same rigging arrangement on both port and starboard sides.
I hope this helps Paul.
Regards,
PeterG.