While preparing to rig the shrouds, I note there are a vast array of different DIY jigs to assist in getting the separation of the upper and lower shroud deadeyes the same distance apart. While most of these are a reasonably good and foolproof method, in my measurement of the required spacings between shroud deadeye separations (from the BB and the Vasamuseet 1:100 scale plans), I need at least three jigs. Most of these methods appear to use a small length of wood with either two or three nails positioned at each end to slide into the deadeye lanyard holes. An example I show below from the Artesania instructions.
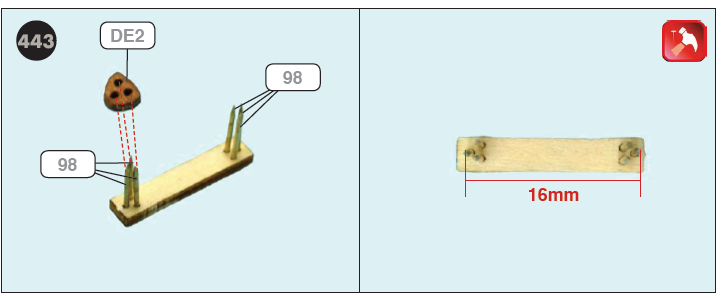
Other kits have similar jigs, but of course with up to three deadeye separation distances, you need multiple jigs. Taking the distance apart from the plans (and scaling accordingly, I bent some double lengths of brass and copper wire and then drilled holes in some scrap wood and placed the bent wire between them. I then soldered two 'support' pieces of wire to hold the jigs in place. Below are my 'rough' but effective jigs (I am not neat with a soldering iron). The mizzen deadeyes (one length) are a different distance to the main and foremast lower sections (second length), and the spritsail mast and topgallant/topmast separations are different again (third length).
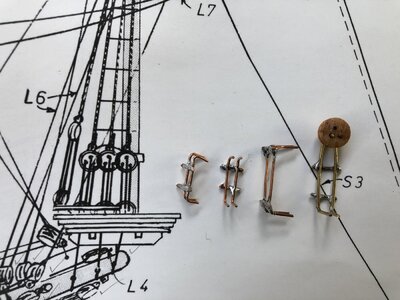
And below I show how it is used in a shroud rigging to set the deadeye separation distances to be the same height along the sides of the ship. Note too, that I am using three seizings which I think is correct from the real Vasa.
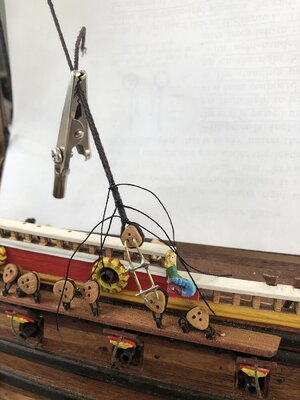
Time Elapsed: 1805 hours
Regards,
PeterG
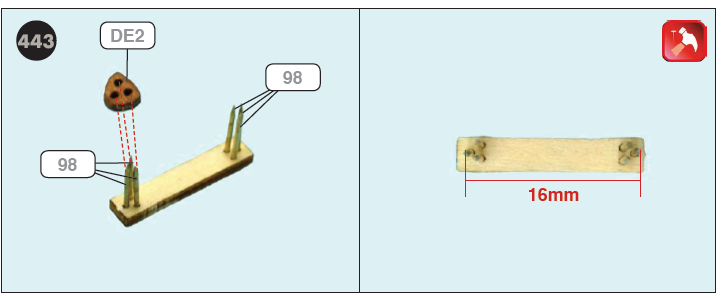
Other kits have similar jigs, but of course with up to three deadeye separation distances, you need multiple jigs. Taking the distance apart from the plans (and scaling accordingly, I bent some double lengths of brass and copper wire and then drilled holes in some scrap wood and placed the bent wire between them. I then soldered two 'support' pieces of wire to hold the jigs in place. Below are my 'rough' but effective jigs (I am not neat with a soldering iron). The mizzen deadeyes (one length) are a different distance to the main and foremast lower sections (second length), and the spritsail mast and topgallant/topmast separations are different again (third length).
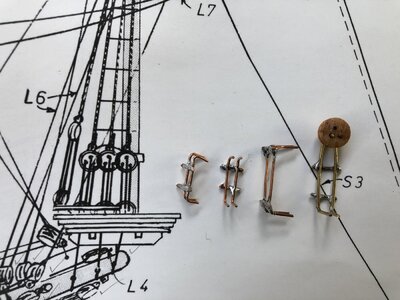
And below I show how it is used in a shroud rigging to set the deadeye separation distances to be the same height along the sides of the ship. Note too, that I am using three seizings which I think is correct from the real Vasa.
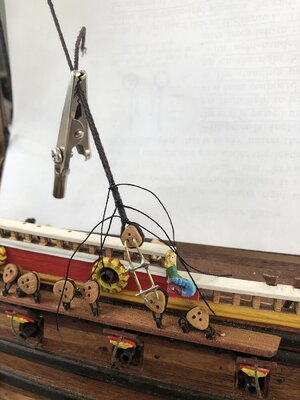
Time Elapsed: 1805 hours
Regards,
PeterG
Attachments
Last edited: