- Joined
- Dec 3, 2022
- Messages
- 1,442
- Points
- 443
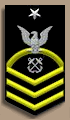
Hmm. I've done a lot (like, a LOT) more plastic modeling than wooden ship-building
Same. Sixty years worth. I ran out of subjects !
and I rarely use anything but Vallejo for airbrushing. It's true that it suffers from the same drawbacks as all other acrylics, but
It’s always intrigued me how modeller A will do brilliantly with a particular paint rands while modeller B can take it or leave it and Modeller C will hate it like sin. That’s why I’m trying not to push my own favorites too much here.
I prefer acrylics because it's easier to spray and cleanup indoors without generating a bunch of HAZMAT.
My children made me stop using enamels. They said I might kill the dogs!
That said, start with a good primer coat (I use automotive primer in a rattle can and you don't need to worry about adhesion (at least for a model).
Lacquer? Ew, smelly. I use Stynylrez acrylic polyurethane through the airbrush straight from the bottle. Mmmm…. Tasty.
I believe Cat is starting with a sealing coat of varnish. Hopefully not an oil based gloss or nothings going to want to stick.
I recently sprayed Stynylrez over a sealing coat of shellac and it looked so good I didn’t bother with the topcoat. I’m now wondering whether I could use it as a one stop sealer/primer/topcoat?
I will say I've had some bottles of Modelair that shot straight, and others that required a bit of thinning. A drop of retarder medium really helps flow and prevents tip clogging.
Retarder. Indeed that’s useful stuff especially in Australia in summer.
Another good thing to have handy is flow improver.