Metalwork - Pumps and Gratings
There are 75 days left in the year and it's now clear to me that I won't be starting my next project on New Year's Day. In fact I'm so mindful (living in the here and now, man), that all future plans have been erased and I don't even know what the next project will be yet. I'm just aiming to enjoy a little boat building somewhere in the day. And today was fun, fun, fun as I occupied myself with two of my favourite things - corrosive chemicals and fire.

The chemical was antiquing fluid. I have no idea what it is but it blackened these hatches and the nameplate in seconds with one application. I polished the nameplate afterwards, thinking of brass nameplates sometimes found on doctors doors where the brass has been polished so often that the background plate also begins to shine.
The Fire was the best bit.
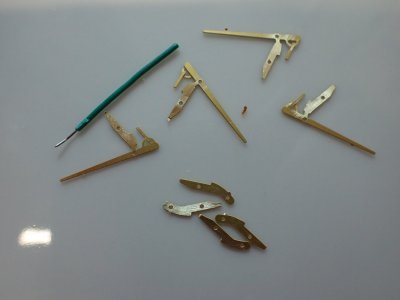
These are the parts of the elm tree bilge pump upper mechanisms. The centre parts, the handles came with two spares. I guess this is due to their extreme fragility. It seemed sensible to anticipate disaster and use two pieces soldered together. With the outside 'cheeks' of the pump soldered to the outside of the two center parts the pumps would be a good sturdy sandwich of brass and lead and perhaps they won't get broken at all.
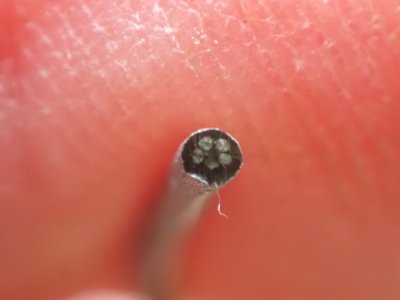
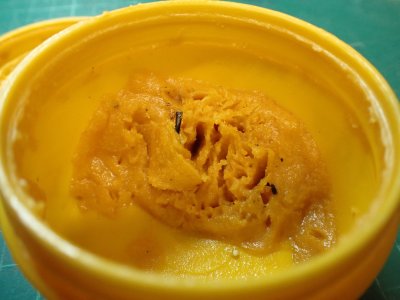
My solder comes with flux built in but that's not enough. Before that can melt and flow, I will already have applied heat to the brass, causing oxidation which will prevent the solder sticking. Flux needs to be applied to the brass first. I've had this snotty potful of flux for 40 years now and don't expect ever to use it up.
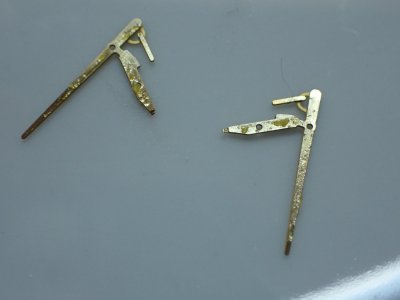
There's two of the centre elements polished clean with a glass fibre contact cleaning pen and fluxed on their mating surfaces only. We can use the oxidation of the other side of the pieces to keep solder away from places we don't want it. It went very well although I haven't done any soldering for a year or more. I find that it's like riding a bike, uncomfortable and dangerous, but easy to remember.
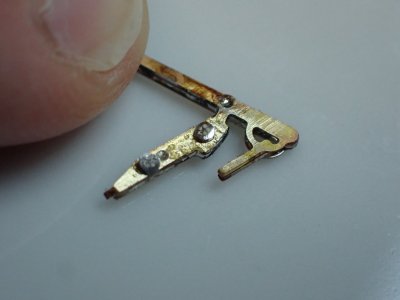
This is the two centre sections soldered together having a cheek piece applied. The mating areas have been cleaned once more. I cut some slices from my solder and stuck them into the flux. There are two here though for the larger centre section joints I used four. I don't use much as it will flow very well when melted and I don't want any overflow. (That's the corner of my fingernail, top left, for scale.)
This is the good stuff, real proper LEAD solder which again I've had for decades. It flows infinitely better than whatever rubbish they have to make the lead-free junk out of.
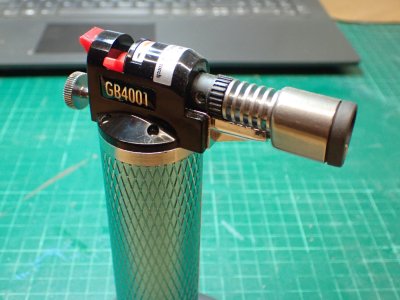
If I was using a soldering iron, I'd have to find a way to hold the parts together while my aged and trembling hands brought the iron into contact. Instead, whenever I can I use a soldering torch. It is so much easier than an iron and since the flame is only on the job for such a short time, fractions of a second, it can even be used for soldering strops around blocks with no damage to the wood. I'll show you that later in the build.
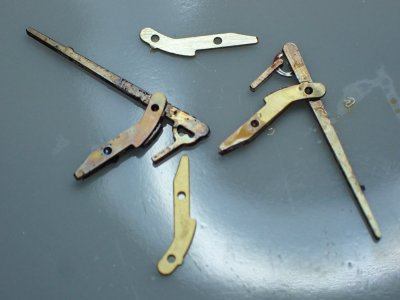
This shows the first cheeks in place with the final layer of the sandwich about to be soldered on the other side.
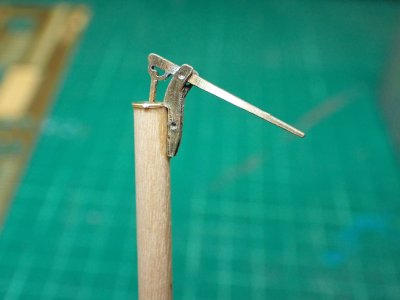
And there it is, cleaned up and superglued to the top of its elm tree. They actually used the whole trunk of the tree, bored out and fitted with a two valve mechanism like a stirrup pump, to lift water from the bilges to the deck and then over the side. Elm was favoured for the job for the same reasons it was used for keels. It was straight, strong and very water resistant.
Next update should show the rough tree rails in place. What a wonderful name that is!
Last edited: