Hello everyone! I was surfing Craig's List today and found a half completed OLD Panart San Felipe for sale. I got it for $5.00 USD! Unfortunately the former owner is deceased, (that's stone dead for all you in Rio Linda, CA). I only had to drive 8 miles to pick up the model Lucky me. I made repairs to damage like a punctured an badly water stained deck and broken railings. Three decoration castings and all but one of the cannon trucks are missing, but the rest of the kit appears to be there. Too bad San Felipe was a fictional vessel. This vessel is too late in features for 1690. Was Panart confusing it with the Real Felipe of 1732? The hull is straight and planked well, but there are dagger planks where there should be drop planks. Much of the kit is plywood, not good hardwood. The wood is very dry and most of the brass fittings are tarnished brown. It must have been purchased many decades ago. The instructions were typed on a mechanical typewriter and copied. Included was an English translation of the Italian instructions that Frank Mastino wrote for Model Shipyard back in 1983. I wonder how the builder got that? The first two cannon decks have false cannon barrels (YUCK!). I can't go back and install cannon trucks at this stage without ripping off planking, and I'm not that devoted to this vessel for that. Rumor has it that Panart (Mantua) made changes to this kit to make it easier to get the positions of the cannon ports correct. On this model, cutting them will be a lengthy, slow and careful affair. This ship will sit on the shelf until after La Couronne and HMS Sovereign of the Seas are done.
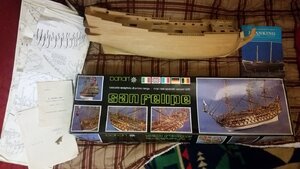
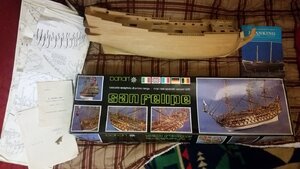