- Joined
- Oct 15, 2017
- Messages
- 1,177
- Points
- 443
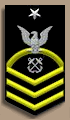
Thanks to everyone for the input, comments, and likes.
So when I finished the first round of tests, I realized I've learned quite a bit about the process, and from a couple of mistakes made in critical areas, specifically the final etching step. As the oldest of 8 kids, I was the first to get a bicycle when I was a young boy. But, with 8 kids, my parents could not afford "training wheels" for my bicycle. So wanting so badly to ride my new bike, I fell, got up, fell, got up, Band-Aids on my knees, fell, etc. The point is, I never quit. I sure didn't have "training wheels" for this process.
So I will be making some adjustments in metal thickness and final etching time. Along with rectifying the mistakes, I will attempt to improve the final products.
But ever curious, I decided to take the sub-par parts created and see how bad they looked if I used them in their current state on the ship. Not on the ship, but on a test panel created for the "treenail test" I conducted a few weeks ago.
For the bolt washers, I created a simple jig to hold the washer in place so the square bolt could be pressed through it. This is the first time I've worked with parts this small. The square bolt is 0.85mm in diameter, and the washer is just 0.2mm thick and very fragile. The gun port hinges are 0.35mm thick.
Some photos on the bolt, washers, and stop pin construction.
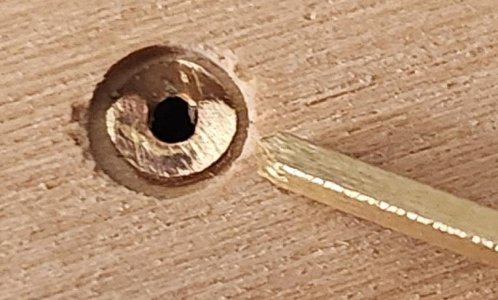
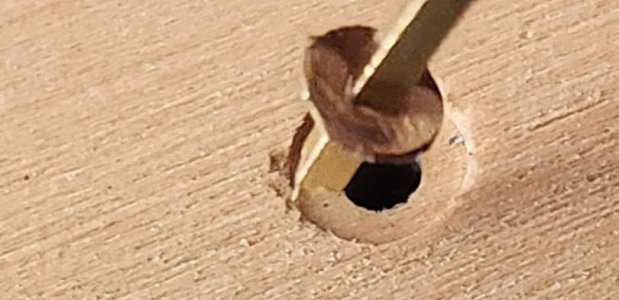
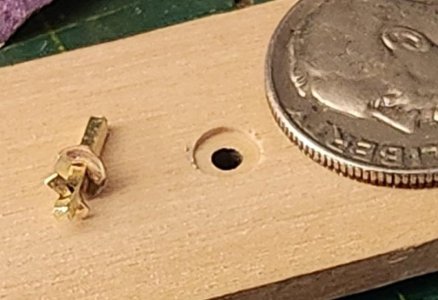
Another lesson learned during this exercise: in the future, I will dry fit the components, disassemble and blacken them individually. In this case, I assembled and blackened them as a unit, which made it very difficult to buff and remove the residual blackening agent. With all the tools I have, I have none small enough to do that.
The test is to see what the finished parts look like in scale, using sub-par components. If they are close, then the thought is that improvements in the quality of the components may suffice in creating a finished product for the gun ports.

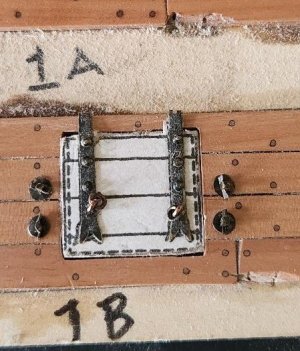
Observations:
Under magnification, the parts are borderline. With that said, if I can improve them a bit, I think they would be acceptable for use.
Once again, guys, I don't see this through the lens of success or failure. It is simply a feasibility test, and actually fun for me.
Thanks again for stopping by and providing your experienced input! Till next time...
Cheers!
So when I finished the first round of tests, I realized I've learned quite a bit about the process, and from a couple of mistakes made in critical areas, specifically the final etching step. As the oldest of 8 kids, I was the first to get a bicycle when I was a young boy. But, with 8 kids, my parents could not afford "training wheels" for my bicycle. So wanting so badly to ride my new bike, I fell, got up, fell, got up, Band-Aids on my knees, fell, etc. The point is, I never quit. I sure didn't have "training wheels" for this process.
So I will be making some adjustments in metal thickness and final etching time. Along with rectifying the mistakes, I will attempt to improve the final products.
But ever curious, I decided to take the sub-par parts created and see how bad they looked if I used them in their current state on the ship. Not on the ship, but on a test panel created for the "treenail test" I conducted a few weeks ago.
For the bolt washers, I created a simple jig to hold the washer in place so the square bolt could be pressed through it. This is the first time I've worked with parts this small. The square bolt is 0.85mm in diameter, and the washer is just 0.2mm thick and very fragile. The gun port hinges are 0.35mm thick.
Some photos on the bolt, washers, and stop pin construction.
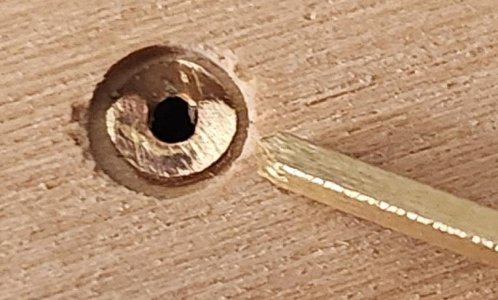
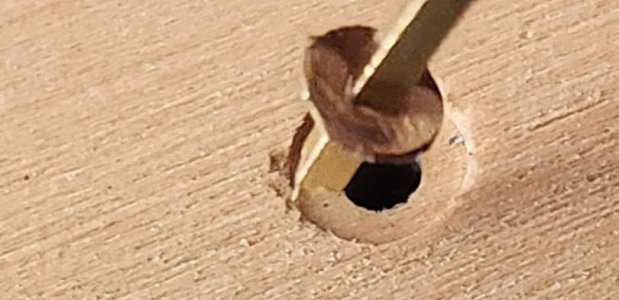
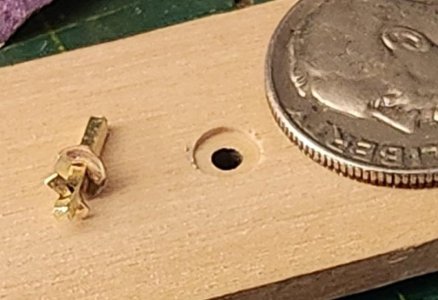
Another lesson learned during this exercise: in the future, I will dry fit the components, disassemble and blacken them individually. In this case, I assembled and blackened them as a unit, which made it very difficult to buff and remove the residual blackening agent. With all the tools I have, I have none small enough to do that.
The test is to see what the finished parts look like in scale, using sub-par components. If they are close, then the thought is that improvements in the quality of the components may suffice in creating a finished product for the gun ports.

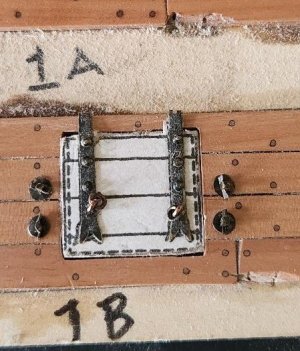
Observations:
Under magnification, the parts are borderline. With that said, if I can improve them a bit, I think they would be acceptable for use.
- The washers are slightly out of scale, being a bit too large in their diameter. Their size will be reduced.
- The hinge bolt holes will be moved a bit lower, especially the eyebolts holding the rings.
- Hinge bolts are scaled well, but the heads of the bolts stand too proud. This cannot be seen very well in the photo, but from the side it is obvious.
Once again, guys, I don't see this through the lens of success or failure. It is simply a feasibility test, and actually fun for me.
Thanks again for stopping by and providing your experienced input! Till next time...
Cheers!