Photo Etching Part 2
The next step, building the UV Light Box used to expose the film. It is a DIY effort. Now I know when it comes to building things, my skills don't come close to the mad scientist skills possessed by my friend Stephan, I just hope my efforts produce something that works.
Materials
Ignore the glass dishes and photo roll (black tube). Also, not shown is the UV LED strips' hardware (in the box) and electrical connecting wires that run the series.
- Bamboo box, only 3.5 inches deep, but I can always increase the distance of the lights from the prints manually.
- Aluminum tape
- 1/8in x 8.5in x 11in plywood
- UV LED strips, with remote control dimming and timing, which I thought would come in handy, and at $16, I could not pass up.
- LED strip connectors (I chose these to eliminate any need to solder)
First things first. Use the aluminum tape to cover the plywood, which provides some UV reflective value.
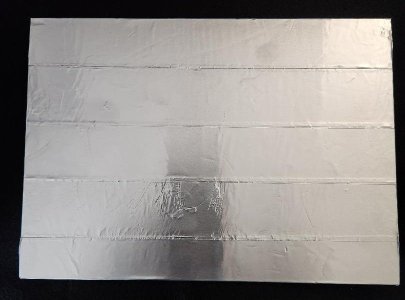
I then mapped out the LED strips and staggered each row to provide a little room when making connections. Since there were two power connectors were provided I decided to use each one to power only 1/2 the bank of LEDs, ensuring sufficient power to all LEDs.
Testing, 1, 2, 3. Oh, wait, I mean POWER UP! It's important to understand not to look directly into real UV light, as it most certainly can damage eyesight.
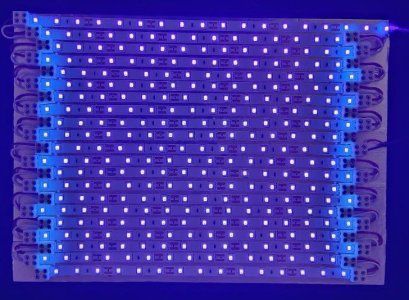
.
In the box. The LED board is held in place using two large Velcro strips. I wanted the ability to remove if I had to work on it in the future. I almost grabbed the Hot Glue Gun...

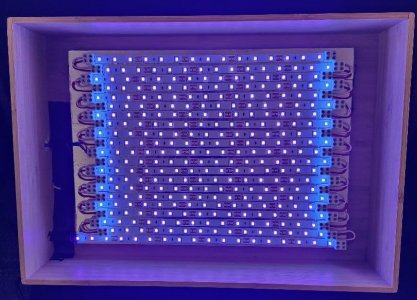
Outside box, with power and controls.
Ok, now that the light box is ready, it's time to prep the test samples, bolt washers first. I take the two identical test pieces of artwork, tape the first one, printed side UP, to the desktop. Then its partner and place it on top of the first one, printed side DOWN. Then, using three small pieces of tape, tape the two pieces on three sides, only after I've ensured the registration marks are aligned. The fourth side remains open, forming a pocket. The brass test sheet is inserted into the pocket.
Note: The arrows below point out anomalies in the ink coverage on the artwork. This can happen during the printing process or, more likely in my case, when I inserted the brass sheet into the pocket, scraped the ink. In either case, these can be covered up with a black Sharpie, EZPZ.
To ensure all three elements remain in place, I create a sandwich with two pieces of Plexiglass being the "bread".
I've read so many tutorials online, each having its own set of variables when it comes to this step. There are really three variables that directly affect the exposure.
- The power of the LEDs or light
- The distance of the sample from the light source
- The time of exposure
Being my first run, I had no point of reference. So I decided, based on everything I read, to create my own point of reference for the exposure step.
- Full power of the UV LEDs
- 5 inches of proximity from the sample
- 6 minutes of exposure, each side
I did that for both samples and ended up pleased with the results of both. The exposed film seemed to take on a muted purple color after being cured, bolt washers below.
Tight, crisp lines. I'm

.
Up next....
The Wash
Note: The final steps involve caustic chemical agents. I wear gloves, protective eyewear, and even an apron. While both of the agents I use, Sodium Hydroxide (Lye) and Ferric Chloride, are on the low end of the caustic spectrum, both will cause skin burns or serious eye damage. It's always slow and steady. I chose these two chemicals BECAUSE they are the milder choices. Other tutorials prefer other more caustic agents. The difference in the choices is straightforward. The more caustic the chemical agent, the faster the metal is etched, and the more harmful they are if mishandled. I can wait 1.5 hours for the final etching, compared to 15 minutes.
Ok, the "Wash" is the step that washes away the unexposed, uncured areas of the photo film. The first step is to remove the outside protective film that is still in place on BOTH sides of the brass sheet.
BOTH sides, Einstein!!!! More on this later.
Once the film is removed, a wash bath is created by combining Sodium Hydroxide and Demineralized/Distilled H2O. While many people online state the ratio does not have to be exact, once again, working with chemicals, I always start conservatively on the "mild" side, always with the option of strengthening the solution if it isn't as effective as expected.
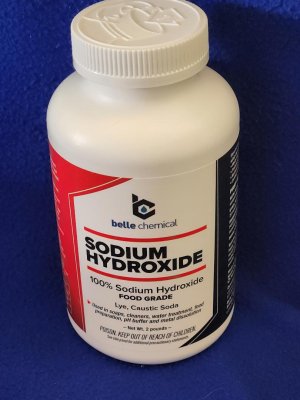
My wash ratio was 5 grams of Sodium Hydroxide to 150 ml of distilled H2O. This worked fine. So after thoroughly mixing, I submerged both samples into the wash and let them sit for a minute. Then, with an old, soft, small paintbrush, I gently stroked the bass sheets for about 30 seconds. Looking carefully, you can see the film slowly being washed away, leaving the purple cured film.
After doing for both samples, both sides, they are removed from the wash and put into a container of distilled clear water, which stops the wash process.
My results were mixed, but valuable.
So, again, for the final etching step, every area where you can see brass, that metal will be etched away, the blue will remain and after a final wash, leave us with tiny identical parts, hopefully. At first glance, everything looks great, but....

The sprue connectors that the arrows point out have delaminated from the metal. I'm ok with this. The reason I'm conducting this test is to identify and resolve any issues before the real production runs.
So, I believe that there are a few reasons the cured film would delaminate from the brass.
- The metal was not cleaned sufficiently, and dirt or debris prevented the film from adhering completely
- The sprue connector was too thin to provide the same adhesion
- The temperature of the lamination process was not hot enough to achieve the same
It could be all three. No worries here. It is not a deal breaker. Now, if 80% of the sprues did not adhere, I would have a big problem, but this one is manageable.
Next step...
Etching
Etching is the removal of the unprotected metal, leaving you with the areas that are protected by the cured photo film. The etching agent I used is Ferric Chloride, 40% solution, which I used straight out of the bottle. This is not some crazy caustic, like Fluoroantimonic acid. Still, I'm very careful. Again, I chose this agent to preserve safety over expedience.
Below you can see the "bolt washer" test plate in the Ferric Chloride solution, diluted. I later realized I needed to use it at full strength and adjusted. (Sorry, no photo). Ok, so the final results for the "bolt washers" test were compromised by my wandering mind. I referred to this earlier in the post, with the "Einstein" comment. When preparing the brass test sheet for washing, I forgot to remove one side of the protective film. It was still in place during the final etching, affecting the removal of metal. Instead of the etching taking place on both sides at the same time, resulting in the removal of metal uniformly, one side was protected from the etching agent, resulting in over-etching in some areas and not in others.
I had no predisposition for the outcome of this test. Success or failure, the truth lies in the feasibility. Can I use this process to create my own uniform, tiny, metal ship parts, or not?
Note: This is not the all-or-nothing solution. Keep in mind, I can still create the artwork and then send those Vector images to a 3rd party service that will create them for me. I can't remember who, Ondras or another master builder, does just this, measuring the value of time and effort. The only downside here is being at the mercy of the lead time of that company, which is not a big deal, as I can be working on many things while waiting.
Ok, after all the exposed metal is etched away, you are left with these parts, albeit covered in cured photo film, again, sorry, no photos.
So what is needed is a final wash, same as the first wash, just let them soak and brush away the film. It just takes about 7 minutes.
WARNING: The next photos are explicit and may be disturbing. Viewer discretion is advised!
Gun port hinges.
Pros
- All parts were fabricated, that's it.
Cons
- Uneven etching
- Side etching, resulting in rough edges, that will need to be worked (sanded, filed) to make smooth.
With these observations, it's important to note, the photo is magnified and the end result, with a little work, is acceptable, in my view on the ship with human eyesight.
Bolt Washers
Pros
- Not many. Some washers turned out well, others not so much. Concern is the lack of uniformity of final product
Cons
- Many, however, I cannot attest to the efficacy of this test as I screwed a few things up
Leaving the protective film was a biggie. Additionally, the sheet thickness being 0.2mm left me with little or no room for error.
So what now?
Observations
The process of photo etching metal, brass, or copper is feasible. I'm not at all discouraged by the results I achieved, knowing nothing. I honestly feel the shortcomings of the final product can be rectified with a little practice and honing down the variables.
The process, when first read or even first practiced, seems very involved, but actually, it is not. There are dependencies that need to be followed, but overall, it is very logical.
This exercise was eye-opening for me. I think my final decision as to whether I will photo etch my own parts or not will depend on whether the quality meets my expectations, on the ship, in scale, and not a magnified photo. The other option is outsourcing the actual process after creating the artwork. The last option seems very viable at the moment.
Before I make a decision, I will take it to the next step, once I'm bored of planking again. I will adjust the variables that I believe caused some issues and see if the final product is of a higher quality.
Secondly, I will take these parts I made and work a little bit with a file and sandpaper and see how they present in their application on the ship (test hull).
Thanks for looking in. Don't be discouraged, I'm not
Cheers