- Joined
- Sep 10, 2024
- Messages
- 571
- Points
- 308
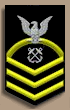
Would be interested in what boards were not nailed, I only have a general idea. Also I wanted to ask if you had any idea on the possibility of how to show the rove that would be visible on the inside of 11 and 12th plank ? Scale size would be 1 mm square.
Until I can get permission to post drawings from the book, I will describe the locations as best as possible.
Each "room" is a space between bitis. The locations are based on the position of the mast. I have moved my mast forward one room as it is located in the full sized ship, therefore you will have to decide where you want to place the un-nailed boards based on where you are placing the mast.
The rooms immediately forward and immediately aft of the mast are unfastened. Then, going aft, there are 3 rooms of fastened boards and then 1 room of unfastened boards. The rest aft are fastened. Forward, the last two full length rooms at the stem are unfastened. So, if you moved your mast forward there are 4 rooms of fastened boards forward. If you left your mast in the center, there would be 5. I hope that is clear enough, but please ask if not.
As for the roves, well, I've been thinking about that a lot. Most were square, but some were rhombic. I thought about cutting small squares of black construction paper, gluing them on and drilling through it to place a nail with a smaller head than those used for the rivet heads.
I really want to use some of the nails from Dry-Dock Models and Parts, but I'm still on the fence a bit. For one, the quantity needed to represent actual scale would be quite expensive - I'd have to file a special requisition with the Admiral. Second, by the looks of it, at this particular moment, they are out of stock of all but one size.
Olha used a black putty and wiped it into the holes. There would inevitably be some left in the surrounding wood grain, but I suppose if your finish were dark enough, that would be hidden.
Another idea I have entertained is to drill the holes and use a 3D pen to push black molten plastic into them, then sand it flush, although you wouldn't get the effect of a rivet head. With either of these last two methods, you could drill a hole and with a small diameter rod that has been ground to a square taper, you could push it into the holes and effectively make them square. The filler would then take on that shape, giving the illusion of roves.
As I said, still working it out in my head.