15th and 16th Oct.
(originally tried to post on friday, but after writing it all out, deleted instead of submit - "you pressed the wrong button,bacon brain"-Miss Piggy)
Anyway, with timberheads removed, reduced the height of stem/bowsprit grove to its high point of 14.5mm (using the sliding sander)
Reposition timberheads with reference to aft aspect of rabbet and lower foot . Luckily (rabbet's foot-ha!ha!) reworking to follow curve is easy. The bowsprit aperture remains the same. Although the bridging chock remained in place, each side needs to be aligned separately. New pin guides are needed.
Result is my timberline is 2mm higher than the plan- ? good enough.
Refit 1st cant -had to reread TFFM as forgotten already although it was only a few days ago.
I had to add a slim shim to "sole" of timberhead . This wood has quite a marked grain pattern so as long as additions are in parallel, they blend very well. In any case, most will be hidden. Probably just me and my conscience know and care.
As others have remarked, surprisingly small changes/variations can have significant effects. On the other hand, wood can be very forgiving and adaptable - don't be frightened dismantling and making corrections.
At last, returning to #2 hawse piece:
The lower part of the opening is at 11.8mm -just 1mm below the markings on my cut out plan. Go with TFFM and use the master plan reference.
As advised, place the upper locator pin below the are which will become the air space (about 4.24mm above hawse hole).
Good and detailed advice about how to file the groove. No so simple as I have a tendency to "rock" and the groove dips ao one or both ends).
Extend lines on copy fore area, place piece lining up the rabbet and clamp both to table. Given the thickness of the piece and wanting to form groove of depth 3.18mm, blocks of thickness 5.25 were taped on either side.
This groove is 2/3 of total (its neighbour #3 is 1/3). My file is 3.17 diam.-the depth of the groove. So when to top is flush with the piece, I've done the job.
The clamping to the table and the direction (slope) outlined on the plan, make this much easier.
My next problem is how to widen the the diameter of the groove to 3.98mm but I do not have a 4mm file. I'll proceed and think of a solution later (or some kind reader can tell me).
The piece has upper and lower air spaces on inner and outer faces- the lower at same height as its partner on the timberhead (and extending to end of piece) the upper starting 18mm above it.
The required 0.4mm is removed by milling -ensuring the parts are supported by a 0.4 shim when milling the second side
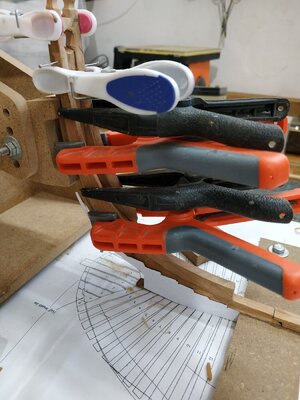

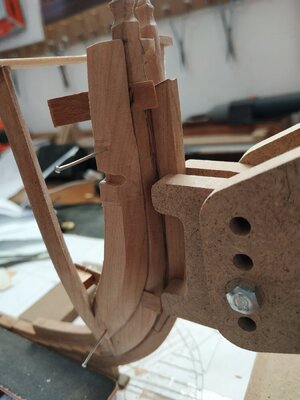
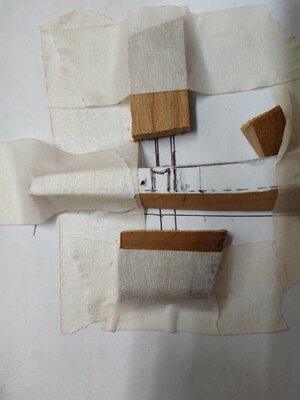
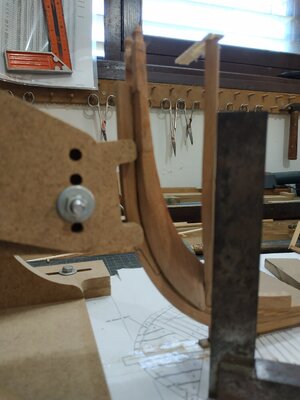
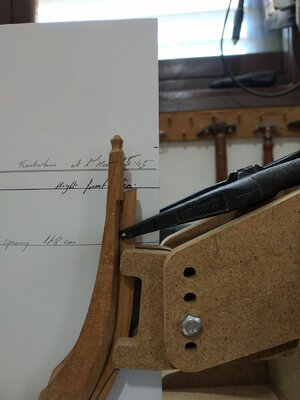