Time seems to fly by so quickly, it surely must be a function of age or is it panic?

.
I feel I haven’t done much on the Syren in the past ten days or so but I’ve been working away on the hull, slow but steady. By the time I measure, cut, soak, let dry, glue and wait it seems the day disappears. Then of course there is the wifely call “Roger, can you….”
I have continued my efforts at laying realistic plank lengths for each strake. As I said before I am also following a sort of mixed butt pattern. To recap, I am only doing this as a practice exercise knowing it will get covered up with copper plates. Time consuming yes but I am actually learning a lot. I read a lot and follow many of the builds on this site by some very accomplished modellers.
A couple of things that I have learned. Heinrich gave me some advice (see earlier) on how to lay the planks and not get overly befuddled (my expression) on measurements and bands. I am doing that but still find I am measuring the space left to fit my estimate of planks needed. As I “close the gap” I’ll get a better idea but his advice is sound.
The kit is supplied with 1/8” by 1/16” wood for the hull planking. At a scale of 1:64 I can understand that the upper hull planks need to be a realistic 8”, but my goodness does it ever take a long time to plank this hull with those 1/8” strips. Since the hull is copper plated I think if I was to do another similar model I’d exchange and use wider strips for the mid and lower hull to speed up the build.
Continuing on from that, I know kit suppliers must think of cost but basswood is not my favourite wood to work with. I am starting to call it “crumblewood”

.
Anyway, a photo of progress. It really isn’t much but it shows other newbie builders that it all takes time. Hopefully I’ll get the hull planked in a week or so. Thanks for following my build.
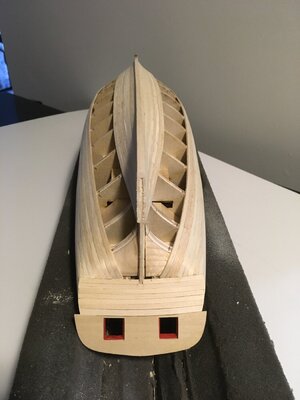