The slow progress continues with accompanying mistakes and attempts at recovery.
The Syren manual says that the first three strakes against the keel should be the garboard, then two broad strakes. I did this some while back and have since continued with lower hull planking. I laid the next five strakes working up the hull but didn’t really notice a problem developing when that fifth plank aft was glued in position. (Counting up from the keel that would be the eighth plank). There is a small, but to me, noticeable droop as the planks lay at the stern.
I realised I had to straighten things up. So I temporarily laid the next plank against that fifth one and found a classic wedge shaped gap became evident. As I sighted along the already fitted strakes I could see that I should have used a stealer earlier. Probably around the time I laid the third or fourth line of planks up from the broad strake. Rather than rip off those planks I decided it was time for a stealer and some reading on how to do it. A bit of head scratching and I thought if I increased the size of a stealer to 3/16” at the aft end it might solve my problem. That would be a 12” plank in full scale, which I thought realistic. So I trimmed, I fitted and sanded, and glued my first stealer in place. The stealer and adjacent plank is no less than 50% of plank width. Unfortunately it does have to twist very slightly so I soaked and clamped it to shape first.
Laying a sixth test plank against the stealer it runs fairly but I can see how yet another stealer will be necessary as planking progresses up the hull. So my mistakes? I should have used a stealer earlier. I should have used a full stealer (not sure) instead of a half stealer because I think it might save me some issues later. I should have temporarily laid the two adjacent planks where the stealer was to be fitted, making it far easier to cut the shape out.
The for’d end of my stealer lands on a bulkhead above a previous butt. Would this be done in actual practice?
Yes it will all get covered up but the learning continues….
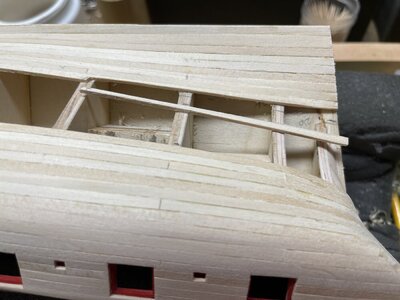
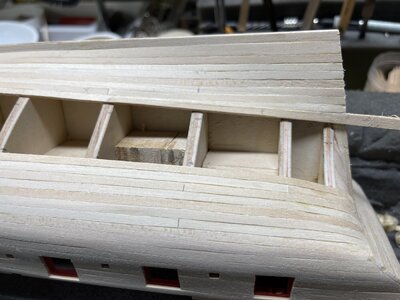
The Syren manual says that the first three strakes against the keel should be the garboard, then two broad strakes. I did this some while back and have since continued with lower hull planking. I laid the next five strakes working up the hull but didn’t really notice a problem developing when that fifth plank aft was glued in position. (Counting up from the keel that would be the eighth plank). There is a small, but to me, noticeable droop as the planks lay at the stern.
I realised I had to straighten things up. So I temporarily laid the next plank against that fifth one and found a classic wedge shaped gap became evident. As I sighted along the already fitted strakes I could see that I should have used a stealer earlier. Probably around the time I laid the third or fourth line of planks up from the broad strake. Rather than rip off those planks I decided it was time for a stealer and some reading on how to do it. A bit of head scratching and I thought if I increased the size of a stealer to 3/16” at the aft end it might solve my problem. That would be a 12” plank in full scale, which I thought realistic. So I trimmed, I fitted and sanded, and glued my first stealer in place. The stealer and adjacent plank is no less than 50% of plank width. Unfortunately it does have to twist very slightly so I soaked and clamped it to shape first.
Laying a sixth test plank against the stealer it runs fairly but I can see how yet another stealer will be necessary as planking progresses up the hull. So my mistakes? I should have used a stealer earlier. I should have used a full stealer (not sure) instead of a half stealer because I think it might save me some issues later. I should have temporarily laid the two adjacent planks where the stealer was to be fitted, making it far easier to cut the shape out.
The for’d end of my stealer lands on a bulkhead above a previous butt. Would this be done in actual practice?
Yes it will all get covered up but the learning continues….

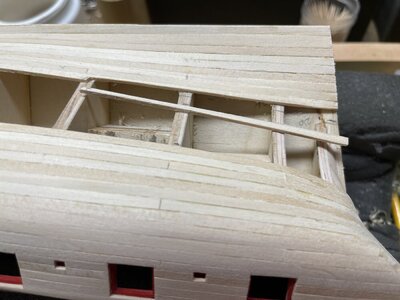
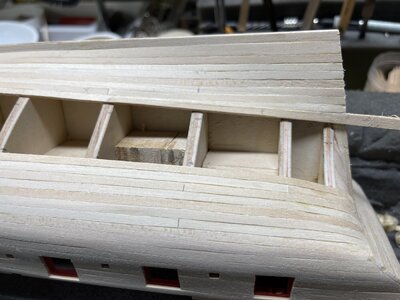