On with the rails which are pre-painted 1mm x 4mm strip. First the straight bits -
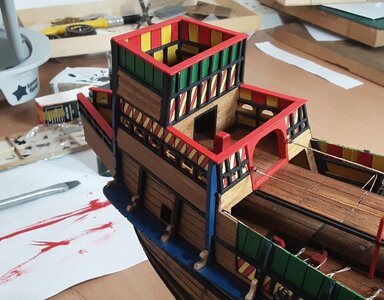
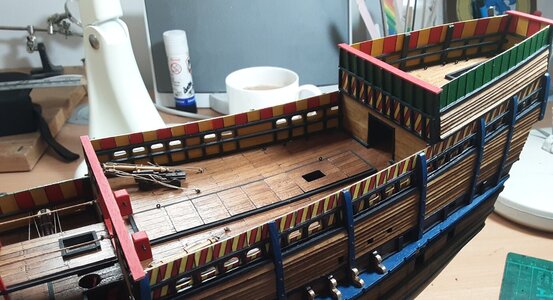
Now we need to bend some wood. I measured the deflection of the curve at the widest point and clamped to that. Wood soaked in very hot water for a couple of minutes.
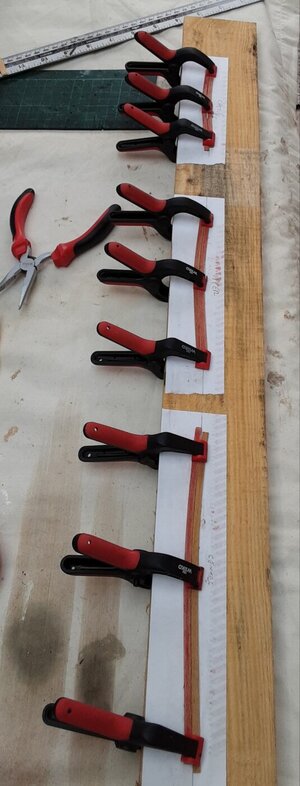
All finished -
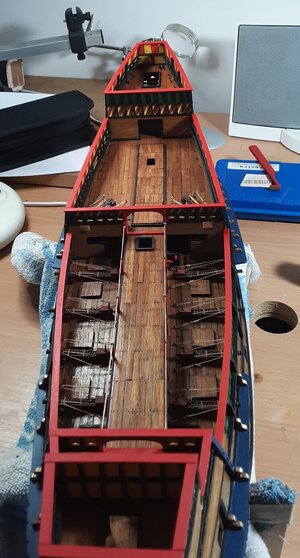
Outboard belaying rails fixed in place -
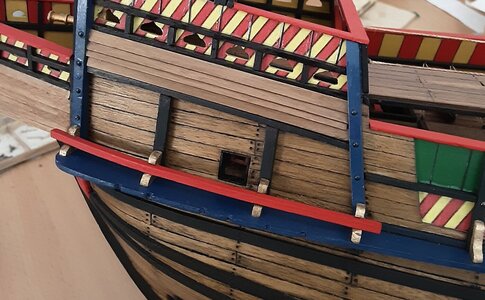
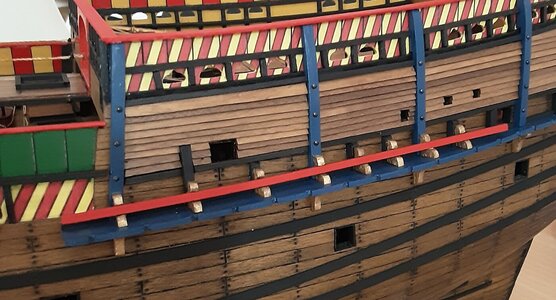
Next are the anti-boarding netting supports. I am now out of CA glue and my local model shop is closed due to the lockdown in my area. Seems it is not an essential business, but at the moment it's pretty bloody essential to me and my sanity! However, I am sure Amazon will come good by the time I have shaped the supports. We live in strange times, eh?
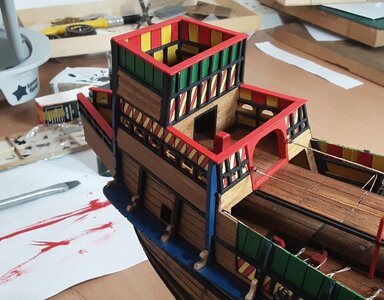
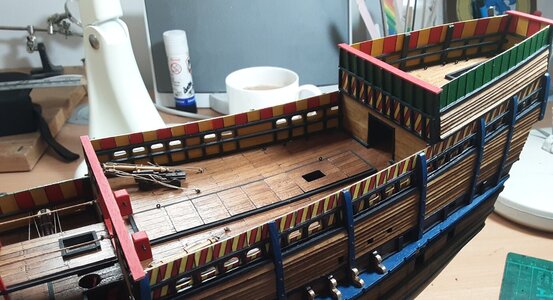
Now we need to bend some wood. I measured the deflection of the curve at the widest point and clamped to that. Wood soaked in very hot water for a couple of minutes.
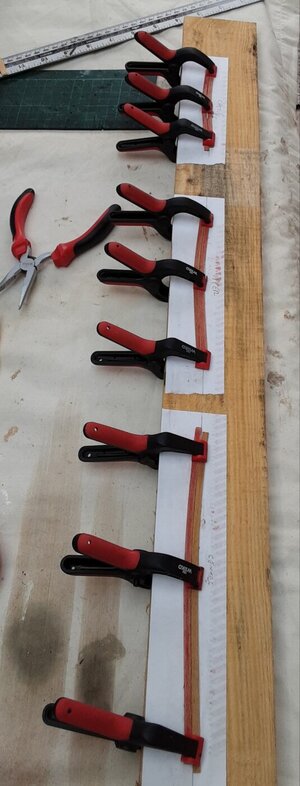
All finished -
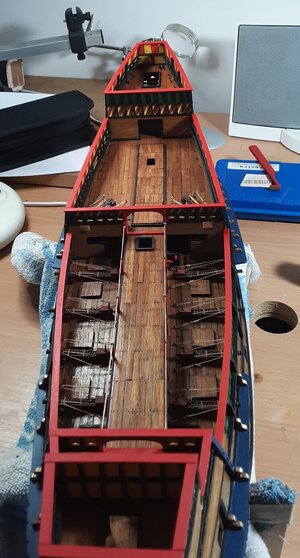
Outboard belaying rails fixed in place -
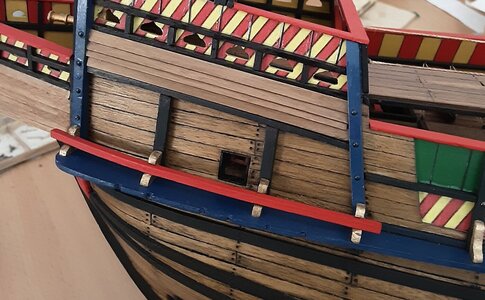
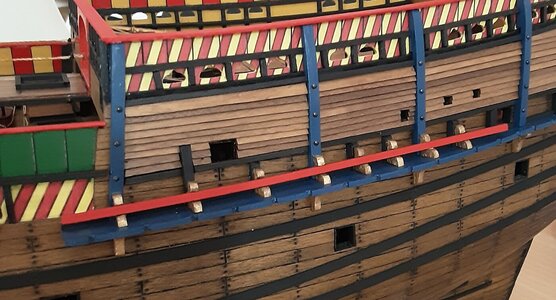
Next are the anti-boarding netting supports. I am now out of CA glue and my local model shop is closed due to the lockdown in my area. Seems it is not an essential business, but at the moment it's pretty bloody essential to me and my sanity! However, I am sure Amazon will come good by the time I have shaped the supports. We live in strange times, eh?