Now it is time for the big surprise, this was the reason for me to buy this kit.
We are ready for the big cut.
With my Japanese saw I cut my hull in half.
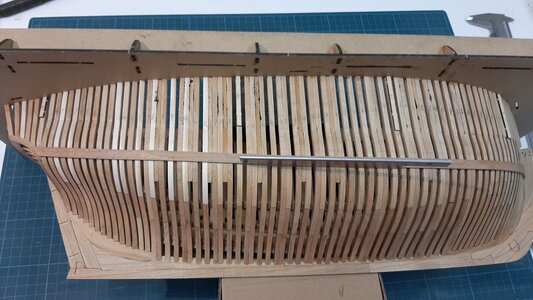
This saw blade is ony 0,4 mm so easily cuts through without a lot of loss of material.
I start in the middle and work towards the bow and stern on both sides. The bow and stern are kept untill the end to maintain rigidity during sawing.
I cut the below the main wale and on the bow slightly below that as the inner shelf clamp is lower placed then the outside wale.
Then I saw towards to bow.
Until half way the stem before finally cutting through.
On the stern I am not cutting through so here I dissollve the PVA with some nail polish remover to loosen the glue joint between the upper transome and the stern.
I also loosen the joint of the upper transome to the frames with a saw and a cutting blade.
Giving some room at the bow to loosen the stern, slowly it is getting loose.
Now the two hull parts are separated. And this is the way I will display the model, so you are able to look into the hull.
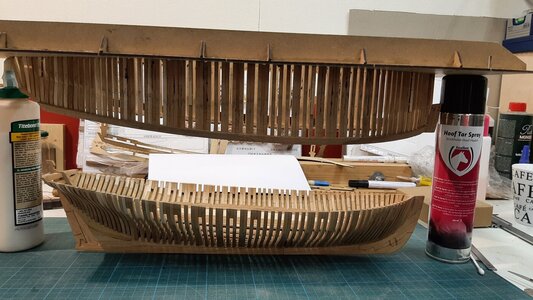
The lower section is now easy to work on and rigid like a block of steel.
Upper and lower part together.
And the upper part.
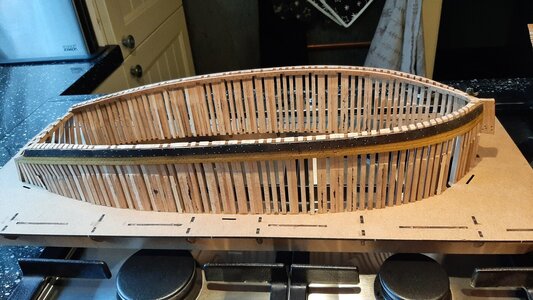
This is how to change your cutter into a viking ship.
Now I have to finish the cutting surface, finish the inside ceiling, outside planking and then fit the copper bolts.
But that is next.
This was the inspiration the contempory model of the Granado.
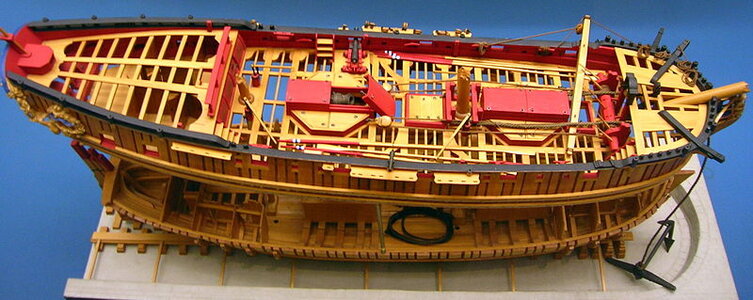