- Joined
- Oct 14, 2020
- Messages
- 275
- Points
- 323
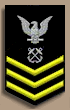
Hi Glenn, sorry for the confusion, we will update the windlass to make the resin part invisible, I have also updated the instuction to make less confusion.
The reason we did not cut out the rabbets of the windlass base are beacuse modellers might have slightly different height for the lower platform, cutting it out might make the fit not so well. We have gave a paper mold of the windlass base for modellers to try and cut, then transfer it to the wooden part, but surely more reminder we should put.
The reason we did not cut out the rabbets of the windlass base are beacuse modellers might have slightly different height for the lower platform, cutting it out might make the fit not so well. We have gave a paper mold of the windlass base for modellers to try and cut, then transfer it to the wooden part, but surely more reminder we should put.