- Joined
- Sep 23, 2021
- Messages
- 228
- Points
- 143
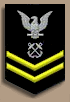
Hi,
The ship is coming along very nicely. Interesting discussion on the bending of ply laminates. After some experiments I found the best and safest way is to just use a hair dryer with medium/hot setting depending on how thick the ply is (thin ply only needs medium heat) fitted with a narrow nozel without any wetting. Just fix one end with clamps and then gently warm the ply and bending it with a little pressure by hand running the hair dryer along the bit that you want to bend. The resin will soften and you can form the laminate with no risk of scorching or the laminates coming apart (if the hair dryer has a cold air button you can just blow some cold air over it and it will fix to shape in seconds). works a treat.
If you didn't see the little cutting/drilling/grinding pen that I mentioned in my log, I can really recommend this little tool. I have more or less been using it for everything since I bought it - cutting and trimming wood/brass, shaping and also drilling. It is so small and easy to use it has become my go to tool and I have hardly used any of my other tools. Bought off ebay model Ant-Xin D1. There are a few not so good generic versions but this one is pretty good and only cost £20 and I have bought a set of additional bits and cutting heads for it
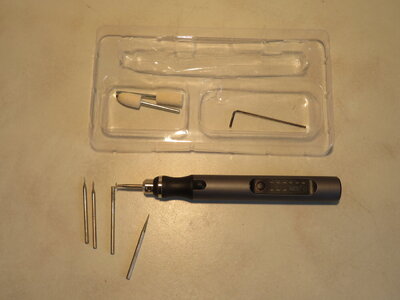
The ship is coming along very nicely. Interesting discussion on the bending of ply laminates. After some experiments I found the best and safest way is to just use a hair dryer with medium/hot setting depending on how thick the ply is (thin ply only needs medium heat) fitted with a narrow nozel without any wetting. Just fix one end with clamps and then gently warm the ply and bending it with a little pressure by hand running the hair dryer along the bit that you want to bend. The resin will soften and you can form the laminate with no risk of scorching or the laminates coming apart (if the hair dryer has a cold air button you can just blow some cold air over it and it will fix to shape in seconds). works a treat.
If you didn't see the little cutting/drilling/grinding pen that I mentioned in my log, I can really recommend this little tool. I have more or less been using it for everything since I bought it - cutting and trimming wood/brass, shaping and also drilling. It is so small and easy to use it has become my go to tool and I have hardly used any of my other tools. Bought off ebay model Ant-Xin D1. There are a few not so good generic versions but this one is pretty good and only cost £20 and I have bought a set of additional bits and cutting heads for it
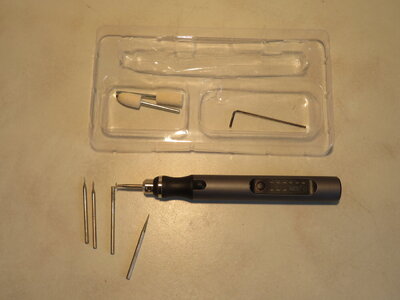