@Peter Voogt Thanks, nice to see you around here. No nothing to stop me.
And everybody else thanks for the likes and visit.
Today the rabbet.
Little tutorial how I do it.
First, I mark the rabbet line with pencil and for that I use a piece of wood along a board. The piece of wood indicates where the pencil line will be.
Note! This is a keel of a Dutch ship. It is not straightforward. So to make a construction in my Proxxon milling machine is not possible. It has to be done by hand and this is also a nice tutorial for those who do not have a milling machine.
So back to the line, see picture how this looks.
After applying the pencil line, I go over this pencil line to cut one in with a knife. Sometimes I can use a ruler, but in the curves I have to do this freehand.
Do not cut too deep, it is only meant as a mark and as a guide for the cutter.
In my handdril I use this cutter. That I can hold along the keel with my finger and cut a small line in the keel on the place of the line I cut before.
When this is done, I take another cutter, a cone shape.
I use this to go deeper in the rabbet line.
BUT TAKE ATTENTION
Only move the cutter in
forward movement. Don't pull it back in the wood. And don't let the tip go in the wood. Only thit way makes a smooth slot. Pulling it back it will change direction and don't follow the line you make first.
Here a picture with an arrow how to move
I always start with the smallest cutters I have. 0,9 mm tip is the best for this job. On a high speed it won't catch in the wood. And keep in mind, don't use force, just let the cutter do the job.
0,9 mm is some times to small for the rabbet, if you need a wider rabbet you take the next cone shape cutter. like a 1,2 mm.
Take small steps with the cutters till you get the width you need on your rabbet. After that is done you go for the max. depth and smoothing the cut. I use the drop shape cutter for this. Note use the thickness of the last use cone for this job. In my case a 1,2 mm. drop shape cutter.
And this one is one of my favourite cutters, you can move this one for and backwards in the rabbet line.
Finish of with a piece of sandpaper to smooth it out.
End result:
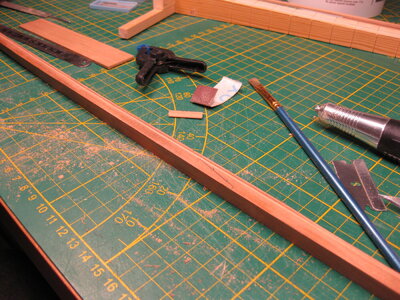
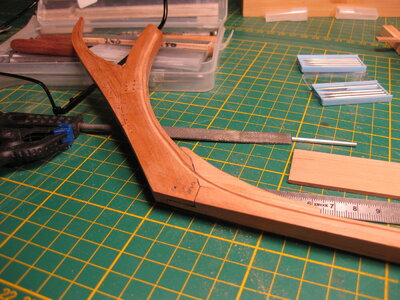
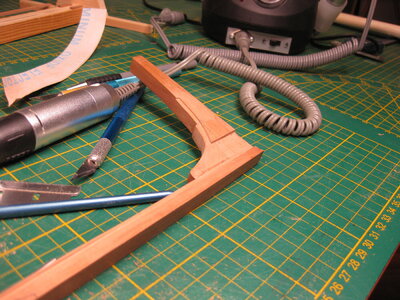
When I'm done on both sides I show you the end result.
Thanks for visiting my build report.
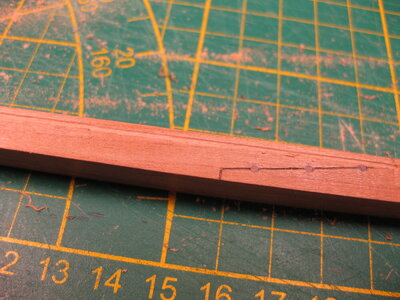