Just a little update, which forces me to keep on track and be self accountable.
I spent some time trying to sort out the construction method for the ass end (am I allowed to say that?). I tried to keep the original transom curve each side by increasing the thickness of the fashion pieces but ended up staying with the excellent instructions. It means the transom straightens out somewhat but I think it looks ok. Like a lot of other Syren builders I found I had to build up and adjust that area in preparation for the mid and lower wales, and aft cap rail.
I used the kit supplied second upper transom piece (black in my photo) but broke it sanding the edges before fitting it. It’s very flimsy but I had made a cardboard template just in case so made another piece. I stained that one, broke the darn thing again and made another. Then looking at Novastorms Syren build I found really liked his interpretive painted black piece. It adds something to that area. Since no-one knows what the aft end of the Syren really looked like I decided to follow suit.
Then it was aft cap rail time. I had already made another of my pine wooden templates (I think I was a shoe maker in a past life

) and then soaked a cap piece that bent reasonably well but, to me, it was not good enough. I broke that accidentally so made another. That one turned out well so that is what I will use. No wonder making this model takes me forever, my excuse anyway.
The mouldings that I had I carved are now fitted as you can see, I made a couple more as a backup. (I now wear a carving glove in case you are reading this
@Jimsky Jim ).
That’s it for now, the cap rail is only temporarily fitted in the photo. I have to shape it and round the edges tomorrow. By the way my foamy dry-dock shown in the images is recycled from a computer packaging box. It’s quite soft on the model and holds the model well as I rotate, turn and invert it.
I am starting to wonder if I write too much in these posts but maybe it will help other new modellers get some ideas, as I have from others.
As always thanks for comments, advice, likes and just looking in on my build.
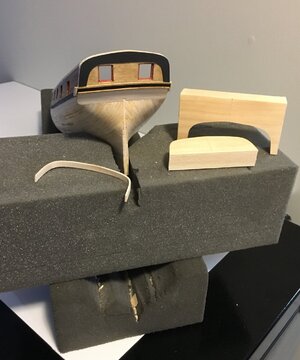
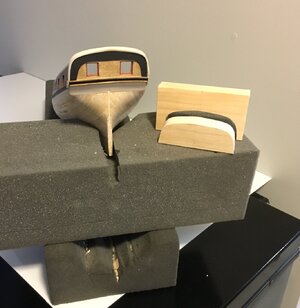